Sustainability is becoming a top priority for more and more manufacturers, who need to adapt their processes to comply with increasing regulations and meet customer demands for products with a lower environmental impact.
Eighty percent of a product’s environmental footprint is determined during its design phase. This raises several questions: What can manufacturers do to improve the sustainability of their products during the design phase? And what about the other 20% – what else can be improved?
According to a recent survey, less than 40% of manufacturers who have a sustainability mandate are able to measure and improve the environmental impact of their product at any point of its lifecycle – from design, to manufacturing, usage, end-of-life and recycling. That’s where cloud-based product lifecycle management (PLM) solutions come in.
In a recent roundtable, ENOVIA CEO Stéphane Declée and NETVIBES CEO Morgan Zimmermann discussed how cloud PLM is advancing sustainability in product development with PLM Global Green Alliance co-founder Jos Voskuil. Here are the key takeaways from their conversation.
1. Transforming product development
With the help of cloud PLM, designers and engineers can adopt sustainability-driven innovation practices from the start of the design process and all throughout development. This shift is creating new products and services but also processes, regulations and cultures.
“For organizations, for many years, sustainability was a report,” says Morgan Zimmerman, CEO of NETVIBES. ”Now it is a purpose-level transformation. They need to reinvent themselves.”
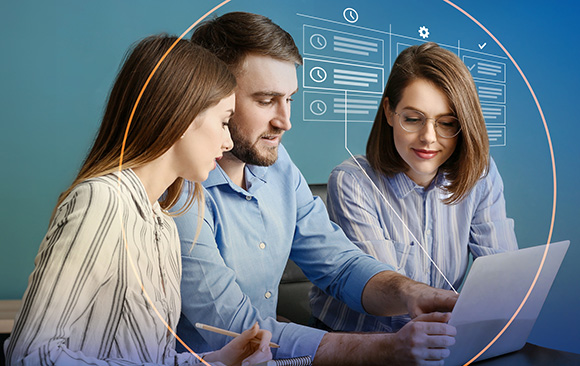
Sustainable design
Products must become more durable and repairable, so designers and engineers need to keep in mind the manufacturing, usage and recycling stages from the beginning of the project. Material, energy and water usage must be optimized to reduce waste, produce as efficiently as possible and comply with regulations.
Changing mindsets
Shifting to sustainable development practices is also transforming the workforce. Integrating sustainability in company cultures is preparing employees to thrive in rapidly changing environments, and access to the right tools and information empowers them to make decisions towards increased sustainability.
It’s the democratization of information that we need to support our behavior change.”
Jos Voskuil, Co-founder, PLM Global Green Alliance
Supply chain
Companies that report greenhouse gas emissions are able to limit scope 1 and 2 emissions – emissions created by facilities, vehicles and purchased energy for example. But it is more complicated for them to limit scope 3 emissions – indirect emissions related to upstream and downstream activities such as transportation and distribution. In the future, manufacturers must strive to produce, source and deliver products locally. PLM, by providing reliable data that can be analyzed and leveraged, is helping them to reach this goal.
Manufacturer responsibilities
Extended producer responsibility programs (EPR) are emerging more and more, making manufacturers accountable for their products well after their usage is over. This is also contributing to a shift towards more service-based business models and the creation of sustainable cross-industry networks.
“We used to do optimal design for manufacturing,” says Stéphane Declée, CEO of ENOVIA. “Going forward, we need to do optimal design for usage and recycling.”
Business models
Sustainability-driven innovation is not just about managing constraints to comply with regulations, it’s also creating new opportunities. Manufacturers who apply the three “R”s principle – reduce, reuse, recycle – are evolving towards new business models and engaging in the circular economy.
2. Using the right tools to manage increasing complexity
It can be challenging for manufacturers to shift towards better sustainability while continuing to innovate. Combining cloud PLM with other tools enables manufacturers to manage increasing product complexity and go further in adopting sustainable practices for every single aspect of product development.
Centralizing all product development, collaboration and data management tools on an innovation platform such as the 3DEXPERIENCE® platform on the cloud allows manufacturers to easily connect data, science, modeling and simulation in one place with Virtual Twin Experiences.
Virtual twins are a digital replica of the product that simulates its behaviors in real-world conditions. This allows manufacturers to measure their product’s environmental impact at any time, helping them make the best choice of materials for example, ensure traceability throughout the entire supply chain, and implement a systems-thinking approach to product development.
By facilitating sustainable product manufacturing, usage and recycling, virtual twins are also empowering manufacturers to go beyond the experience economy, participate in the circular economy and rethink their business models.
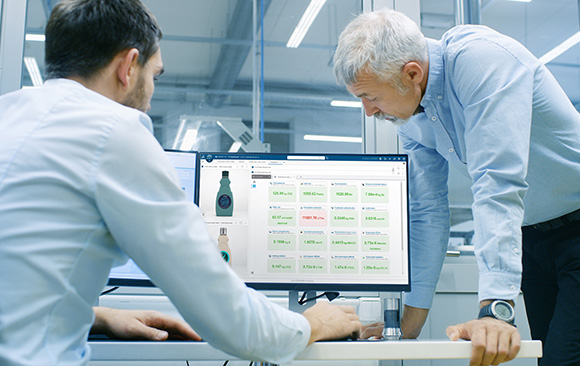
3. Creating new business models and opportunities
Several business models have emerged in parallel with the development of sustainable product development:
- Performance-based models: paying for the outcome or performance of a product rather than owning it encourages manufacturers to create longer-lasting products. Think of car sharing in cities where owning a car is not practical for example.
- Product-as-a-Service: leasing a product instead of buying it. This promotes better maintenance, reuse and recycling – examples go from furniture to electric vehicle batteries.
- Closed-loop supply chains: consumers give a deposit and get it back when they bring back the product after they’re done using it. This optimizes the use of resources and enables better recycling and remanufacturing. This model could limit waste in the fashion industry for example.
- High customization and on-demand production: produce only what is needed to reduce waste.
- Integrated ecosystem services: connecting different sectors to create sustainable solutions that benefit the entire ecosystem. Waste created in one factory could be repurposed and used by another if these networks were developed.
Product development is evolving towards better sustainability, durability and repairability thanks to cloud-based PLM and Virtual Twin Experiences, enabling manufacturers to engage in the circular economy and create new business models.
If you want to learn more about implementing sustainable product development practices with cloud PLM and virtual twin technology, watch our roundtable, Advancing Sustainability with PLM: Four Key Business Transformations.
Learn more:
- Reimagining Sustainability: Virtual Twins at the Wheel
- Present and Future Outlooks of PLM in Manufacturing Industries
- How Manufacturers are Using the Power of Cloud-Based PLM to Drive Innovation
- What’s Next in PLM? with Stéphane Declée of ENOVIA
- Sustainable by Design: The Virtual Twin Advantage
- Customer story: csi entwicklungstechnik