The take-make-waste model isn’t cutting it anymore, for the planet or for business. Did you know that the OECD estimates just 9% of the plastic waste we produce each year gets recycled? The United Nations Environment Program did the aftermaths: that’s 36 million tons of the 400 million tons of the plastic waste we produce annually. The remaining 364 million tons gets incinerated, or finds its way into landfills or the oceans. By 2050, Ellen MacArthur Foundation estimates there could be more plastic in the seas than fish!
Plastic isn’t the only problem: Our steel, concrete and carbon-based energy production industries are all based on extracting raw materials, with very little thought given to what happens when we’ve finished using them. Even extracting those materials imposes environmental costs. Take copper: To get 2kg or less of copper out of the ground, 100kg of earth needs to be moved, refined and disposed of.
There are clear business implications for this as well. All this waste also represents massive value leakage from our supply chains. According to research from the WEF, transitioning to a circular economy could be a $1 trillion (€913.64 billion) opportunity.
But in order to build a circular economy – that is, an economy that prioritizes sustainable design, waste minimization and material reuse – we need solutions that will allow organizations across industries to make the changes they need to integrate circularity right across their business. For many of the businesses I speak to, circularity remains a great theory – less something easily put into practice. But where there’s a will, there’s a way. We just need to show that way. We need to see circularity in action.
What’s putting the brakes on the circular economy?
It’s become clear from recent conversations with business leaders that, while sustainability remains a high priority, recent global events and disruptions are getting in the way of progress. It’s harder to justify a green premium during a pandemic or in the middle of a cost-of-living crisis.
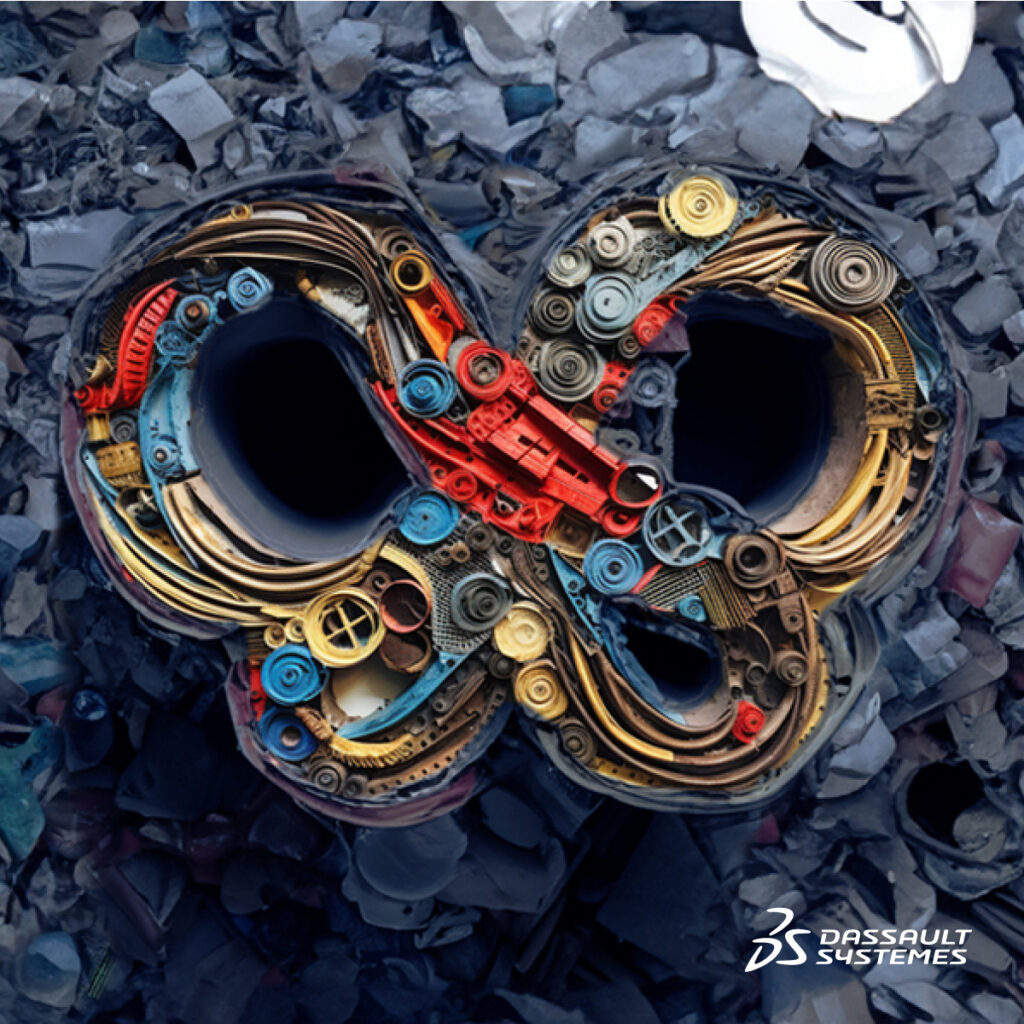
Then there’s the sheer complexity of reorienting a complex global business. Moving from a linear model to a circular economy involves creating new roles and reskilling existing ones, developing new internal processes, and integrating different technologies. That’s a whole lot of “new.”
The encouraging news is that more and more stakeholders want companies to change and adopt more sustainable business models. Customers want it, investors want it, and employees want it. Of course, leaders want it as well – they’re just cautious about implementing what can feel like fundamental changes to their existing business model in the midst of uncertainty.
There’s also growing government support for change. The European Commission, for example, has promoted things like the Fit for 55 program, which aims to align EU policy with the target of 55% emissions reduction by 2030. They have also supported the circular electronics initiative, which lobbies for customers’ “right-to-repair” electronic goods.
The EU is also launching the Digital Product Passport, a digital record of an individual product’s complete lifecycle, which will help establish the traceability of components throughout the lifecycle.
And it’s not just in the EU. South Korea’s Green New Deal is planning to make available $17 million in subsidies to electric car buyers, and $33.5 million for hydrogen fuel-cell electric vehicles. Even more ambitious is the USA’s $800 billion Inflation Reduction Act, of which $369 billion has been earmarked for green energy and climate change mitigation initiatives.
Embracing the challenge, building the solution
It’s time for concerted action. If we want to make the circular economy achievable, scalable and profitable, then we need to embrace circularity across entire business models. This means embracing new, biodegradable, and recyclable materials. It means designing products that are optimized for reuse and repair. And it means shifting our enterprise value networks to prioritize circularity.
What’s really encouraging is that major industry players are also embracing circularity. One of the most inspiring examples of circularity in action I’ve come across is Renault.
Under CEO Luca De Meo, the company is shifting its identity from just being an ‘automotive brand’ to being a “technology, services and energy brand,” a move described as “Renaulution.” It represents a massive step toward a circular model and places a great emphasis on upgrading and maintaining vehicles that are already in use, alongside new sales.
The cornerstone of this new model is the Re-factory, Europe’s first plant dedicated to extending vehicles’ lifespans. In a move that has required a deep reorganization of its manufacturing operations, Re-factory will recondition more than 100,000 electric vehicles and convert diesel utility vehicles to 100% electric or biogas powered.
Of course, reorienting your whole value chain after years of take and make linear thinking can seem like a daunting task. Where do you even start?
The trick is to make the path clear for both you and your stakeholders. That means the first, critical, component of the transition to circularity is deepening your understanding of your existing value networks. Doing so enables you to plan, predict, and perfect potential changes.
For me, this principle has been brought to life through our work with Bouygues Construction. This ambitious renovation of a Paris sports complex used our 3DEXPERIENCE platform to connect stakeholders across the value chain and create a single source of truth for the whole project.
With proper visibility of the data in the ecosystem, Bouygues was able to take standard modeling a step further and create a virtual construction twin, which captures and models operational data in in real time, to test every stage of the project from purchasing materials through to the assembly of the building.
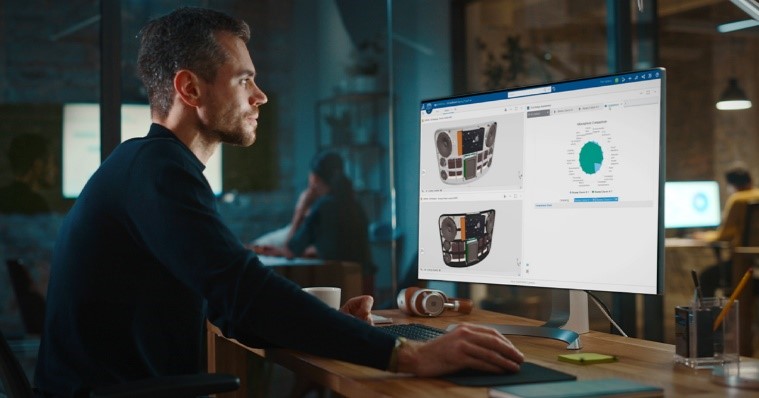
Another powerful way of exploring circularity is life cycle assessment (LCA). LCA approaches allow you to integrate operational and design data and explore, in granular, real-time detail, what’s happening at every stage of a product’s life. It means businesses can design more intelligently, take steps to tackle wasteful activities and make decisions that lead to more circularity.
For example, if you are manufacturing glass bottles you might think you’re making a sustainable product, but these products might be less recyclable in actuality.
LCA can shed light on crucial questions like: How is glass recycling supported in certain markets? What products can be recycled where? Are there any specific regulations I need to consider when I’m designing my logistics chains?
Armed with this information companies can be proactive and adapt operations to make their processes truly circular. After all, 80% of the environmental impact of a project is decided at the design phase. LCA lets you understand how exactly that impact ripples out through your value chain.
Just in time, we’ve woken up to the strains that industries are putting on the natural limits of our planet. Circular economies allow us to tackle resource scarcity, address pressure from regulators and customers, mitigate supply chain risk, and build truly resilient operations. We’ve only got one planet, and if we want to survive – and thrive – on it, then we need to make sure the future is a circular one.
You can see what it means to put circularity into action here.