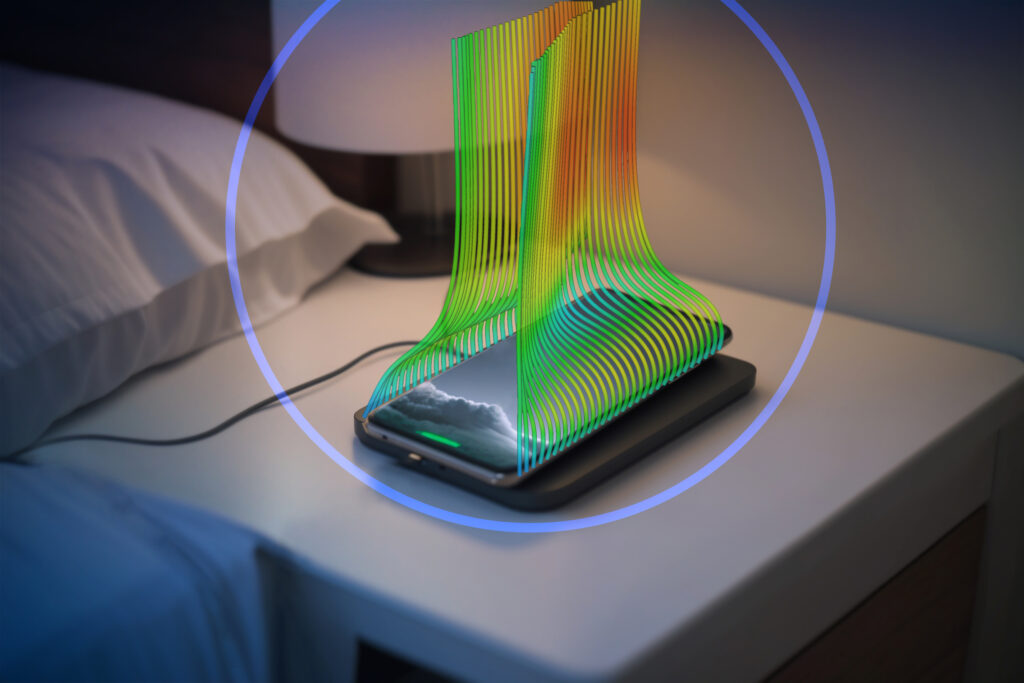
Shrinking Pains – The Challenges Facing the High-Tech Industry
The High-Tech industry is built on complexity. Ever more performance and functionality is being packed into small, lightweight devices. “The risk of failure is higher because of the complexity,” says Jonathan Oakley, SIMULIA High-Tech Industry Process Director. “Being able to get that first, prototype to work first time is really important. It’s more important than ever, because it may be difficult to identify the cause of a problem, or even to fix the problem.”
Bryan Hurlbut, SIMULIA Global High-Tech Industry Process Expert, notes that wearables from smartwatches to virtual reality (VR) and augmented reality (AR) headsets are putting particular pressure on manufacturers to find innovative solutions to minimize size and weight. Using the example of a smartwatch for skiing, he says “the device knows that I’m on the mountain, and it tells me what my exercise rate is, it communicates with each lift to tell me how many lifts I’ve taken and what my vertical skiing for the day is. All of the different antennas – 5G, Bluetooth, GPS – interact with the environment that you’re in to supply you with data, and packing all that in there and having it all communicate reliably is what’s driving a lot of these challenges.”
In particular, Bryan notes “The battery can be one of the largest single consumers of space, so optimization from a physical size and performance perspective is necessary.” (For more information, see “Innovating better batteries for electronic devices”)
With so many components in a single device, finding the best trade-off between different KPIs can be a challenge. A change that improves the performance of one subsystem can easily have a negative impact on another, but the interactions between different components and subsystems can be hard to quantify. Despite this, there is a lot of pressure to turnaround optimal designs rapidly to remain competitive and bring products to market faster.
David Johns, Global High-Tech Industry Process Expert, adds “There’s also the technical challenge of designing components that can handle the super-high speeds of modern data rates.”
In addition, a complex device requires a complex global supply chain. Geopolitical tensions and other unexpected events are pushing up energy, shipping and materials costs, meaning manufacturers must keep costs as low as possible.
What is Multiphysics Simulation?
Simulation is well-established in the industry as a way to inform design, optimize performance and identify and resolve issues. By simulating a Virtual Twin of the device, engineers can analyze the performance of a design without the costs associated with constructing and testing a physical prototype.
There are many different types of simulation covering different aspects of physics. Some of these include:
- Structural simulation: Structural aspects such as stress, strain, deformation and fracture. Example use case: to ensure the device can withstand drops and impacts.
- Electromagnetic simulation: Fields and currents within and around the device. Example use case: to optimize antenna placement and reduce interference.
- Fluid simulation: The behavior of fluids such as air or water, including heat transfer. Example use case: to design air-cooling systems.
- Vibroacoustic simulation: The vibration behavior of structures and the propagation of sound. Example use case: to identify resonances in components that produce buzzing noise.
Many scenarios couple together different fields of physics: Jingsong Wang, SIMULIA Global High-Tech Industry Senior Specialist, gave another example of a vibrating capacitor: “The capacitor vibrates at the resonant frequency of the PCB – it is quiet but you can hear it hum. If we move the resonance a few hertz, the sound stops. So the resonant frequency is crucial to stopping the noise. To model this we have to simulate the electromagnetic and piezoelectric behavior of the capacitor, the resonant modes of the PCBs, and the radiated sound.”
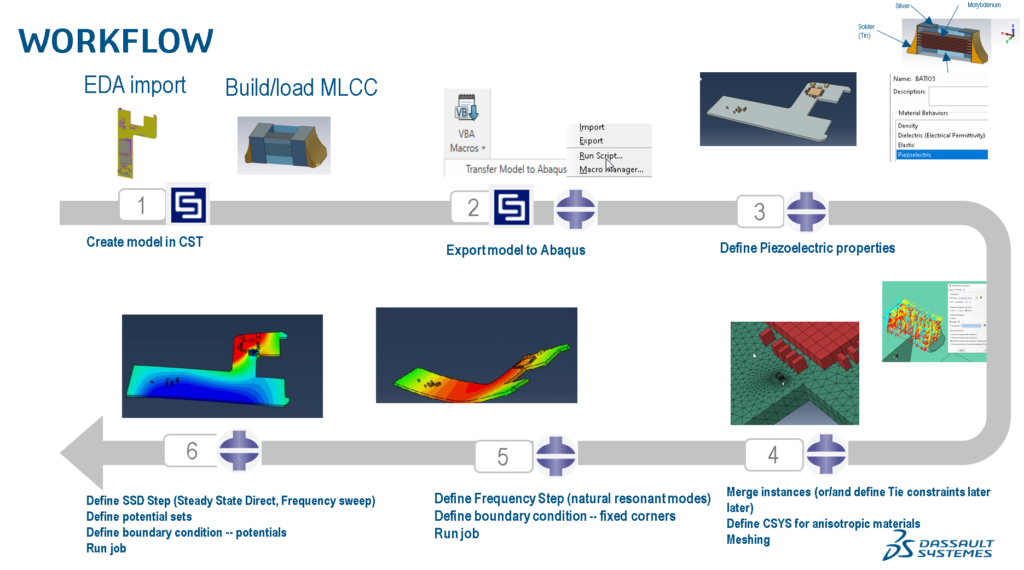
Even when there is no direct connection between disciplines, trade-offs can often involve balancing the results of several different types of analysis. David pointed to a USB connector as good example: “One critical aspect is the pins and springs that meet when you push the connector parts together. They have important electromagnetic design aspects for signal integrity – TDR, impedance, S-Parameters, and so forth. But there’s also the structural element of the retention spring, and that force needs to be just right to relieve the springs that slide over pins, but provide enough retention.
“If you change something from a structural point of view, it might have too much impact on electromagnetics and vice versa. So in that case the physics would not be coupled, but they would independently influence the design and there’d be some trade off.” For more information about the SIMULIA solution for connector design, see “High-speed Connector Design with Modeling and Simulation”.
Faster Regulatory Approval with Virtual Certification
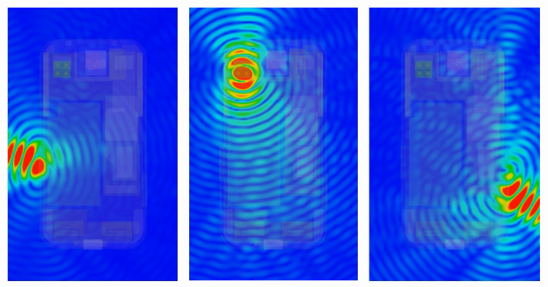
“Any radiating device has to comply with regulations in each geographical region, and this has to be demonstrated by certification before it can be sold,” Jonathan explains. The traditional way to get certification involves providing measurement data from a prototype to the regulator. However, the test regime for a complex device can be time-consuming and expensive – a beam-forming system as used in typical 5G phone can result in hundreds or thousands of different scenarios to test to ensure that interference and specific absorption rate (SAR) limits are not exceeded in any case.
“Regulators now increasingly accept simulation results for virtual certification, replacing measurements from test,” Jonathan adds. “To get realistic results for certification users need to simulate the entire device with all antennas.” To see a real-world example of simulation being used to support virtual certification, see “Simulation for 5G Smartphone FCC Certification”.
Get Results at Any Stage of Design with MODSIM
Unified modeling and simulation (MODSIM) is a concept where modeling and simulation are combined on a common data model. With MODSIM, designers have access to simulation data even at the concept stage the design, allowing it to be analyzed from the earliest stages of development.
“MODSIM allows you to go all the way from the ideation and the requirements through to full virtual prototype,” explains Jonathan. “And of course, it also allows you to do the connected physics, because the physics simulation is working on the same dataset and the same CAD geometry. You can deal with all of the physics at the same time and ensure the optimal trade-off is achieved.”
SIMULIA products can be integrated into a MODSIM workflow on the 3DEXPERIENCE platform. This acts as a ‘single source of truth’ for the whole team. David explains that “One of the major challenges is the inefficiency of the development process itself. Companies traditionally have used a very manual process, often emailing files around, and each analyst may develop different versions for their own use. Very quickly it gets out of hand, and there’s often confusion about which version of the model you’re working on, especially with multiple design iterations.” Keeping all model and simulation data in the same place ensures everyone is working from the same files and updates to the model can be automatically propagated to all teams. It also ensures traceability, with a digital thread providing a robust link between the model files and the simulation data.
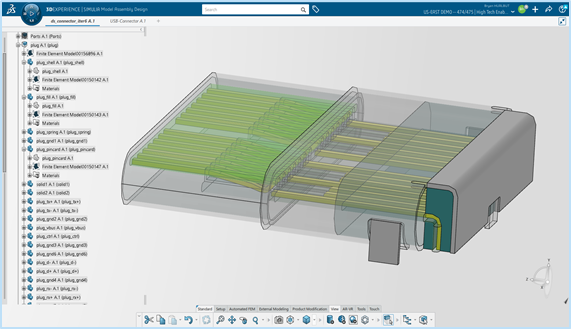
Even global teams with complex supply chains across multiple companies can collaborate seamlessly with MODSIM. Access to data can be restricted to protect confidentiality and trade secrets, and encrypted models can be used to share data for integration analysis without revealing sensitive geometry.
Conclusion
To remain competitive in the fast-moving high tech industry, manufacturers need to bring innovative new products to market faster, with less development cost and risk. Unified modeling and simulation (MODSIM) accelerates development by providing designers and engineers with the data they need to make informed decisions even at the earliest stages of design. Multiphysics simulation can be used to model the behavior of complex systems covering many physical disciplines and help engineers find the best trade-offs between competing design requirements.
By implementing MODSIM in their design flows, manufacturers can also streamline the design process to ensure the whole team is working with up-to-date files and any changes to the design are automatically propagated. Files can be shared with partners while maintaining confidentiality and protecting sensitive intellectual property. Traceability between the model geometry and the simulation data allows virtual certification, reducing the need for physical tests and making regulatory compliance faster and cheaper.
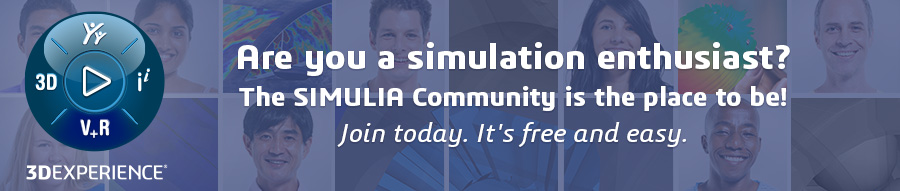
Interested in the latest in simulation? Looking for advice and best practices? Want to discuss simulation with fellow users and Dassault Systèmes experts? The SIMULIA Community is the place to find the latest resources for SIMULIA software and to collaborate with other users. The key that unlocks the door of innovative thinking and knowledge building, the SIMULIA Community provides you with the tools you need to expand your knowledge, whenever and wherever.