WHAT HAPPENS WHEN MODERN COLLABORATION MEETS HIGH-TECH DEVELOPMENT?
Today’s ever-changing High-Tech landscape demands agile workflows and seamless collaboration for efficient product builds. SOLIDWORKS® Integrated Design Environment helps teams reduce complexity and guesswork across the organisation, so more time can be spent focusing on the work that truly matters.
THE STATE OF HIGH-TECH:
AN INDUSTRY UNFORGIVING TO UNCERTAIN CYCLES
Uncertain product cycles are just not acceptable in high-tech development.
With increasing competitive pressures, shorter product life cycles and the advent of new technologies hitting the global market at an unprecedented rate, manufacturers need to adopt agile processes and policies in order to stay competitive.
COMPLEX PROCESSES SLOW DOWN PRODUCT DEVELOPMENT
As technology advances by the day, High-Tech product development have become intricately more complex and sophisticated. Miniaturization and precision-driven requirements further clog up lead times, accentuated by miscommunication and lag time between departments.
As a result, Time-To-Market (TTM) is often delayed, leading to costly extensions and unnecessary confusion.
MULTI-FACETED DEMANDS
Not only do High-Tech teams and manufacturers need to consider the growing demands of the consumer, competitive firms today must meet stringent government standards and address safety, sustainability and recyclability concerns.
However, traditional methods, disparate software and manual processes stitched together make it hard for companies to react and adapt to changing needs.
UNCERTAINTY LEADS TO ERRORS
Uncertainty breeds errors, which are often costly and difficult to rectify.
Electrical, electronics and mechanical engineering teams act on outdated or miscommunicated information, stored across a diverse and disparate array of software. This further increases the chances of errors down the line.
The end result is a chaotic and under-managed High-Tech product development cycle that is not operating at full capacity.
COLLABORATION: THE KEY PILLAR OF SUCCESS
In a complex environment full of uncertainty and ever-changing requirements, High-Tech teams need every advantage on product development and iteration cycles.
Competitive advantages, however, diminish the moment collaboration is inefficient, scattered, or improperly set up within organisations.
Establishing and maintaining a compelling lead in today’s High-Tech world, therefore, requires precise and error-free collaboration between multidisciplinary teams who have access to an integrated and collaborative development environment so that they can develop innovative products more quickly, cost-effectively, and at higher quality levels.
Tech-Clarity’s Solving High-Tech’s Top Six Critical Business Issues eBook identifies the top six critical business issues that high-tech companies should address and how they can be overcome by enabling collaboration between interdisciplinary engineering teams. READ MORE.
———-
INTRODUCING SOLIDWORKS®, A UNIFIED DESIGN PLATFORM THAT ENABLES INTERDISCIPLINARY ENGINEERING TEAMS TO TRULY COLLABORATE
The key to enabling true collaboration within High-Tech firms lies in unifying mechanical, electrical, electronics and network functions into a single, dynamic ecosystem.
By integrating these seemingly-disparate but highly-interconnected processes into one single place, SOLIDWORKS® gives teams complete clarity and vital insights into the entire product life cycle, reducing guesswork and unnecessary conflict.
From concept to detail design to manufacturing, SOLIDWORKS® is your one single source of truth for fast, rapid development and deployment, ensuring that teams are kept in the loop of everything in between.
ALL-ENCOMPASSING HIGH-TECH PRODUCT DEVELOPMENT: FROM CONCEPT TO MANUFACTURING
High-Tech is already complicated; there’s no need for its engineering processes to be complex too.
SOLIDWORKS® was built from the ground up to unlock true collaboration between engineering teams, using a unified product data model and database that centralises the entire product cycle within one single native application.
Teams gain clarity into their entire product cycle through near-real-time updates, empowering them with the right, accurate information they need to push product development forward.
A SINGLE SOURCE OF TRUTH REDUCES UNCERTAINTY
SOLIDWORKS® eliminates the barriers of multiple file translations and out-of-date files that come from the use of disparate tools and data management environments from multiple suppliers.
In addition, users instantly get access to a design environment that natively houses and categorises mission-critical documents all in one place. That means less frustration and lag times due to incompatible software, leading to better collaboration and development.
STAY CONSTANT WITH CHANGE
SOLIDWORKS® features fully associative change updates without sacrificing time or error-prone translations. Mechanical, electrical, electronics and network design departments can better “talk” to one another, without confusion as to what updates in one department mean for the others.
SIGNIFICANT TIME AND COST SAVINGS
SOLIDWORKS® integrated mechanical, electrical and electronic solutions allow High-Tech firms to create and manage efficient collaborative design processes, empowering users to develop electro-mechanical systems faster by working more in parallel rather than a traditional serial process.
Let us bring you through a typical high-tech product development life-cycle with SOLIDWORKS®.
———-
HIGH-TECH PRODUCT DEVELOPMENT WITH SOLIDWORKS
STEP 1: CONCEPTUAL & INDUSTRIAL DESIGN
Bring Your Vision To Life With Best-In-Class Design Tools
SOLIDWORKS® equips you with a suite of modern, cloud-based design tools that allow you to bring your innovation to life in a collaborative environment.
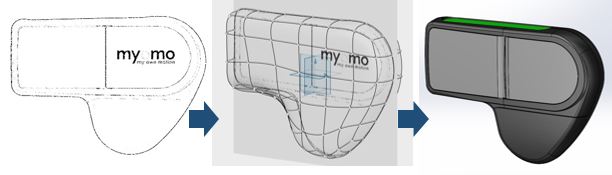
Product Designers can accurately transform their 2D designs into 3D parametric mechanical models and 3D detailed designs, while retaining key measurements and guidelines.
As a result, companies can now confidently develop, review and select concepts before committing vital resources to detailed design and manufacturing.
STEP 2: DEVELOP & INTEGRATE 3D MECHANICAL AND ELECTRICAL DESIGNS
Reduce Design Conflicts Using A Collaborative Design Workflow And Environment
Miscommunication during the design process leads to confusion, misunderstandings, and design errors, resulting in costly delays.
SOLIDWORKS® reduces design conflicts across multiple design disciplines (including Mechanical, PCB design, and Electrical) through a parallel design workflow and environment.
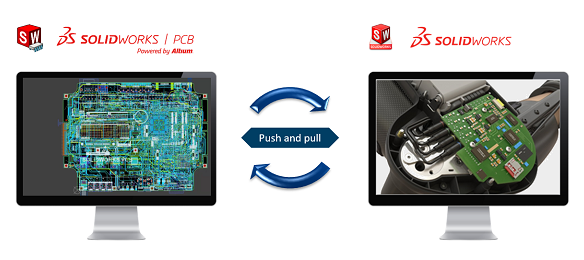
Additionally, SOLIDWORKS® facilitates ECAD/MCAD integration, allowing both mechanical and electrical engineers to quickly pinpoint any potential collisions between PCB and enclosure designs, sharing compatible design data across different systems to identify a solution.
Besides that, the integration also enables collaborators to strategically position key electrical components for optimal performance, using input from electrical, mechanical and industrial design departments.
SOLIDWORKS®’ simplified and cross-functional design environment shortens the design and innovation cycle, unlocking greater design quality, reduced costs and shorter time-to-market.
- Mechanical CAD (MCAD) Design mechanical structure using Surface and Mesh modelling techniques. Draft analysis can be done for both aesthetic design and future mold tool preparation.
- PCB Design (ECAD) Create preliminary circuit tracing based on MCAD layout
- MCAD and ECAD Collaboration Place Electronic/Electrical components precisely and review the placement in 3D for clearance check
STEP 3: VIRTUAL PROTOTYPING
Quickly Identify Design Flaws Using Real-World Simulations
Product changes, innovations, and updates are a constant in the fast-paced world of High-Tech. Companies cannot afford to launch ill-designed products that look great on paper, but fail in the real world.
A world-class product development tool must simulate how designs will stack up against real-world conditions, even before production begins, so costly mistakes can be identified and resolved upfront.
SOLIDWORKS® Simulation offers a robust, easy-to-use suite of analysis tools (FEA, CFD) for predicting a product’s real-world physical behavior by virtually testing CAD models to see how it performs under true-to-life scenarios.
- Shock and Vibration (FEA) Assess product performance and quality under static, thermal and buckling conditions
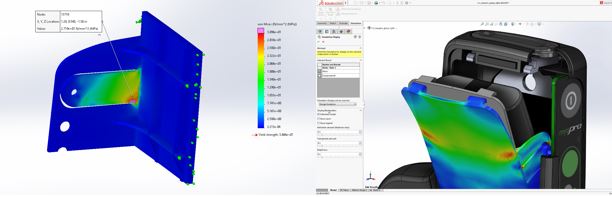
- Heat and Thermal (CFD) Simulate fluid flow, heat transfer, and fluid forces that are vital for design success
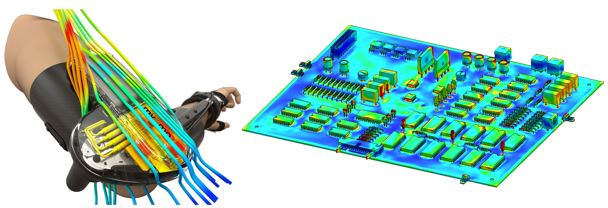
- Plastics & Parts
Accurately predict and avoid any possible manufacturing defects in plastic part and injection mold designs, thus eliminating costly rework, while improving part qualitySimulate Plastic Injection: Get valuable design insights including fill and cooling time, as well as understand part quality characteristics
Model Intricate Plastic Parts: Using existing geometry as a reference, mark locations for pins and hardware mounting bosses, while automatically creating Snap Hooks.
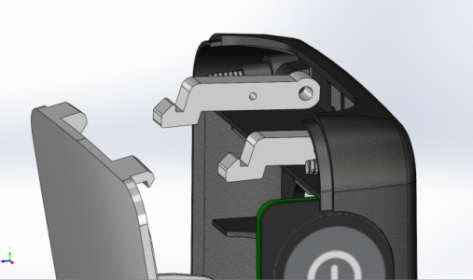
- Optimization Tools Modify multiple variables across iterative design changes, and concurrently set certain limits on other design parameters
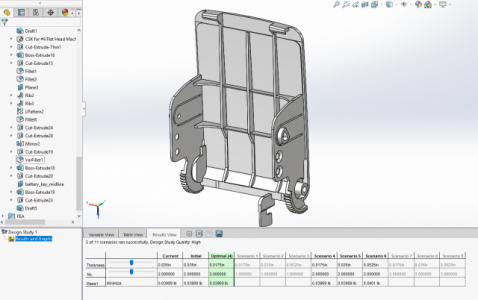
Have you ever wondered about the accuracy of computational analysis?
When testing your designs, it is crucial to use a tool that provides reliable results.
Read this report and see how SOLIDWORKS® Simulation provides highly accurate results for your virtual testing needs. The proof is in the analysis.
STEP 4: PRODUCT DOCUMENTATION & VISUALIZATION
Create In-Depth Documentation And Collaterals That Help People Understand Your Product With Clarity
SOLIDWORKS® isn’t just a design suite for your product – it’s also your indispensable tool in helping others understand it.
Create and autosave your technical documentation concurrently with your designs directly into the cloud.
Add further depth into your product documentation through high-quality illustrations, photorealistic images, and interactive animations directly from 3D CAD data.
From assembly instructions, marketing collateral, technical illustrations, interactive animations, to training materials, SOLIDWORKS® has you covered.
STEP 5: MOVE CONFIDENTLY INTO PRODUCTION
Minimise Translation/Interpretation Errors Using 3D Designs And Specifications That Are Clearly Understood
Manufacturing is a vital and delicate part of the product development process that many teams struggle with.
The current state of manufacturing from 2D drawings work, but are often open to misinterpretation, since they do not always match their associated 3D designs.
Studies show that the 2D-3D disconnect occurs up to 60 percent of the time, resulting in massive downstream production failures, inconsistent quality, and unnecessary waste. This disconnect could be avoided entirely with SOLIDWORKS®.
Our software accurately translates 2D drawings into information-rich 3D digital designs, leaving no room for misinterpretation by manufacturing teams.
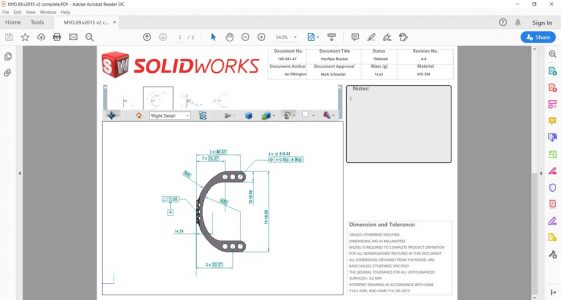
By automating the generation, organization, customization, and sharing of product manufacturing information (PMI) data, SOLIDWORKS® enables significant cost savings for users, giving them an edge in production efficiency.
STEP 6: PROJECT & DATA MANAGEMENT
A Single Source Of Truth For Every Aspect Of Your Project And Data For True Collaboration
SOLIDWORKS® is the easiest way for designers to collaborate without worrying about version control or data loss.
No more frantic searching through a myriad of files and folders scattered all over your organisation; SOLIDWORKS® stores and organises engineering CAD data and other documents in a central vault, so designers can find any file, any time.
Featuring an all-in-one storage relational database that allows users to search files and references, set users and group permissions, design sophisticated electronic workflow processes and more, SOLIDWORKS® is the single source of truth that powers your modern product development workflow.
WATCH THE ON-DEMAND WEBINAR
Watch the webinar and learn how your electronics designers and mechanical engineers can collaborate seamlessly with SOLIDWORKS!
TEST DRIVE SOLIDWORKS® TODAY
Take SOLIDWORKS® for a spin and see how our Integrated Design Environment can take your High-Tech development process further.
OR TAILOR YOUR SOLIDWORKS® EXPERIENCE
For more in-depth insights into understanding how SOLIDWORKS® can specifically help your use case, speak to our SOLIDWORKS® consultants now.