The Industrial Internet of Things (IIoT) is revolutionizing the factory floor with a proliferation of connected sensors and smart devices that can gather literally billions of data points from on-going activities. This data provides an unprecedented view of minute details of production events and activities – in real-time – to controllers and operators so that processes are documented, controlled, and managed for higher quality and efficiency.
Analytics are the Key
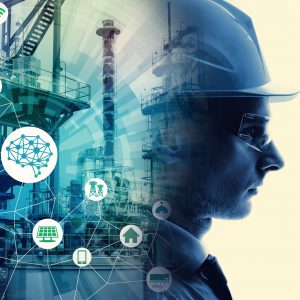
All of this data is not just thrown away after the process is finished. Collected, processed, and stored, a history of processes and measurements from a given machine can provide valuable information about performance and trends that can help engineers improve processes and spot potential problems. Furthermore, analytical programs can take the data from any number of similar machines and combine it together to get a better overall picture of how these processes work and how they may be better managed and improved.
Taking this idea a bit further, the combined historical data can drive maintenance activities that can prevent the production of bad parts thereby improving quality and reducing waste.
The idea of preventive maintenance – fixing a process or piece of equipment before it starts producing bad parts – is not new. Neither is the idea of predictive maintenance; using data and systems to anticipate the need for maintenance, whether it’s lubrication, adjustment, tool replacement or something more serious, based on usage and measurements rather than on a fixed schedule. IIoT data, like that mentioned above, turbocharges predictive maintenance through the power of analytics.
Data Analytics
Large data sets from some number of machines, and their individual experiences making a given part, are pooled together and analyzed, yielding a very detailed picture of how the process actually works in real life, including expected variation, and the record of how the process behaves as tools, and equipment age, wear, and break down. Based on these models (simulations), systems can compare actual performance measurements directly against the model of ‘normal’ operation for continuous monitoring as the work is proceeding. When a variation is detected, the analytics can compare the deviation to those experienced in the past and identify the likely cause. Additional data maps out the progression of the deviation, confirming the cause-and-effect relationship.
The analytics can then simulate how the process is likely to progress and recommend corrective action and the ideal time to make the correction. If the timing is not critical (detected early enough to allow some discretion in when to apply the fix), the maintenance request can be passed to the scheduling system to allow the scheduler to fit the maintenance activity in where it will cause the least disruption to production and the timely completion of parts and products.
Digital Automation
It is interesting to note that today’s analytics and artificial intelligence goes far beyond simple statistical and SPC analysis. It is not bound by the usual rules and assumptions and is free to use simulation to identify new insights. For example, tool wear data can be used to recommend tool sharpening or tool replacement activities, as you might expect, but the analytics might also suggest a change in the tool path that would reduce the rate of wear or the potential for tool damage or breakage.
There’s an unlimited treasure of potential intelligence buried in the flood of data that IIoT provides. Modern analytics uncover these opportunities in a way that helps manufacturers improve performance, reduce cost, and keep equipment producing quality parts and products more reliably.
Editor’s Note: Learn more about digital collaboration platforms and fueling innovation by registering for Dassault Systèmes 3DEXPERIENCE: A Virtual Journey. Our series of online, on-demand episodes deliver thought leadership, actionable content from industry influencers, Dassault Systemes experts, and customers who have implemented 3DEXPERIENCE to meet today’s manufacturing challenges.
Check out the session agendas, and register to watch anytime, anywhere.
3DEXPERIENCE: A Virtual Journey schedule:
- July 29th: Manufacturing and Supply Chain.
- August 26th: Fueling Innovation in the New Agile Enterprise.
- September 23rd: Modeling & Simulation.
- October 14th: Enabling Business Continuity Via the Cloud.