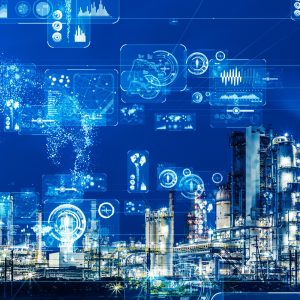
Today we are faced with unprecedented and widespread disruption. Manufacturing, supply chains, and the workforce at large have all been affected by the COVID-19 virus. Before the pandemic, much of manufacturing was moving to adopt new innovations, expand global connectivity, and reshape the business landscape from start-ups to established companies. Now more than ever, manufacturers must remain flexible, agile and operational. Fortunately, digital transformation has long been underway, and this reinvention of the manufacturing industry can help manage global disruptions while ensuring business continuity.
For example, 3D virtual experience twin technology effectively streamlines resource planning. It has the ability to rapidly validate normal production change requests or quickly pivot operations to alternative products as the result of disruptive events. Simulations allow managers to rapidly change plans for plant layout, validate the production line, and virtually commission machines and robots prior to sending them to the factory floor. With full digital continuity powered by the 3DEXPERIENCE platform – work is accessible anywhere, at any time and teams can better manage complex operations.
Dassault Systèmes’ Factory of the Future breaks down institutional silos empowering decision making and collaboration for global manufacturing whether in the factory or working remotely. Discover demos, white papers, webinars and more on how the Factory of the Future can connect the virtual and real worlds to help companies of all sizes collaborate, model, optimize and perform manufacturing operations.
Disruption, innovation, and global connectivity are all reshaping how manufacturers deliver in today’s experience economy. Competition, unexpected events, and consumer demand put relentless pressure on manufacturers. A world-class business platform can help digitally transform operations and enable companies to be prepared.
Read on for our curated collection of top posts on the innovations enabling the Factory of the Future and learn how digital transformation can address today’s operational challenges.
Digital Twin – What’s The Big Deal?
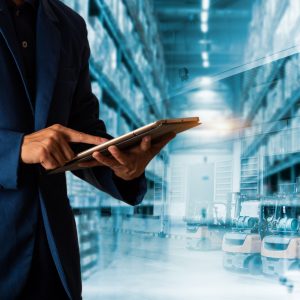
The real power of the Digital Twin comes from its connection to the real world. The proliferation of sensors and smart devices commonly called the Industrial Internet of Things (IIoT) allows us to closely monitor what happens in production and in the field. This data is added to the Digital Twin to allow the simulation to self-critique – compare what actually occurred to the prediction based on the engineering data. Any deviations are analyzed and the model updated to better reflect actual experience. In that way, the Digital Twin continues to grow and mature, getting more complete and more accurate as time goes on.
How To Transform Manufacturing With Edge Computing
Edge computing is the logical technology to empower the connections between the digital world and the physical world as Digital Manufacturing grows and matures. Edge computing refers to adding intelligence and computing power to the devices at the far reaches of the computing network. Rather than simply collecting data and passing it on, remotely installed devices (on the edge) can process the raw data, identify and pass on only the truly useful data, and either discard or process, condense and store the rest for future analysis or use.
Workforce Transformation In The Age of Digital Manufacturing
Manufacturing has changed dramatically over the last twenty or thirty years. Workers are more likely to be controlling and monitoring machines that do the actual work. And those that do perform manual tasks are likely to be assisted by automation, directed by computer, and reporting their accomplishments and measurements through data collection devices.
Digital Manufacturing Powers a Sustainability Transformation
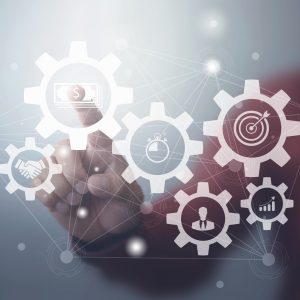
In today’s burgeoning Industry Renaissance, digital manufacturing is spearheading a global transformation in how we design products, learn skills, produce goods and deliver them worldwide. Digital manufacturing, through its ability to simulate and model beforehand, has become the proving ground for evaluating and executing sustainable material usage, production and delivery processes that lessen environmental impacts.
With the IIoT, the “Things” Mind Themselves
Smart manufacturing—digital brains controlling ops and crunching data where the rubber meets the road, whether it be banging metal, assembling components, or inspecting throughput. The result is a data-rich and more adaptable shop floor, “aware” of itself and able to communicate its needs—and better able to serve the larger goals and strategies of the overall organization, as companies pivot incessantly in response to changing customer demand, production or supply chain disruptions, and a fickle global business environment.
Will the Factory of the Future Find Data Security in the Blockchain Platform?
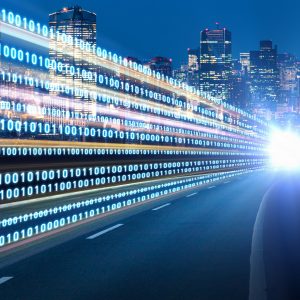
Blockchain is the common name used to describe a distributed ledger system which is a growing list of records, called blocks, that are linked together. Each block contains codes that tie to previous blocks, making the chain resistant to modification that would, in effect, break the chain. Blockchain allows users to record transactions in a secure, verifiable way that does not rely on a central authority like a bank to manage the data and its security.
5 Factory Uses for Sensors You Might Not Expect
Sensors are some of the most remarkable electronic devices available. Some of their applications in factories and manufacturing are a little lesser known right now, even as Industry 4.0 continues its disruptive march.
Future Technology Coming to Your Manufacturing Plant
Advancement in the areas of robotics, technology, automation and artificial intelligence are leading the charge in what Professor Klaus Schwab deems the fourth industrial revolution, or industry 4.0. Manufacturing plants are integrating methods and techniques that allow for cheap and autonomous production of goods. It’s undeniable that manufacturing is taking a step into new, uncharted territory, but what is the technology driving this change?
Learn more about the Factory of the Future, Manufacturing and Supply Chain topics by registering for Dassault Systèmes 3DEXPERIENCE: A Virtual Journey. Our series of online, on-demand episodes deliver thought leadership, actionable content from industry influencers, Dassault Systemes experts, and customers who have implemented 3DEXPERIENCE to meet today’s manufacturing challenges.