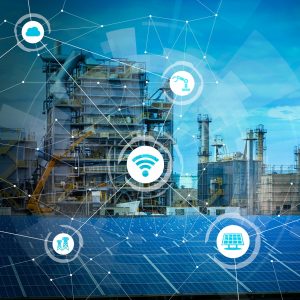
Manufacturers are reeling from the impact of the coronavirus pandemic on their operations and supply chains. Production plans have been disrupted due to changes in demand, raw material supply and workforce availability. Many automotive plants have had to temporarily shut down production or repurpose their assembly lines to produce medical devices such as respirators.
As manufacturers transition to recovery phase, the search is on for the fastest way to ramp up production while still respecting all safety regulations. In these uncertain times, the need for digital transformation is greater than ever. Digital acceleration allows manufacturers to create optimized contingency plans that take into account real-time data and conditions. It helps them understand the impact of disruptions on supply chains and manufacturing operations. This is where the virtual twin has a major role to play.
The Virtual Twin Experience, an executable virtual model of a physical system, brings in learning and experiences taken from REAL world processes to update the digital model. As an accurate representation of working conditions that uses real-time data, it allows manufacturers to assess changes virtually, before implementing them in the real world. They can also set KPIs to measure performance in real time and adjust operations accordingly without having to be physically present at a production plant.
For example, manufacturers that want to repurpose their resources and deliver higher value with a limited workforce can explore the use of automation in their plants. With the virtual twin, manufacturers can review production data and make adjustments to ensure best use of the automation capabilities.
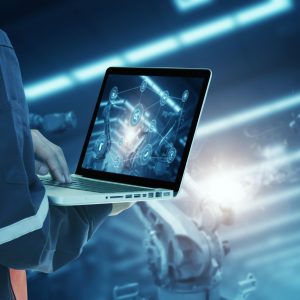
The accuracy of the virtual twin relies on the data gathered from resources and operations on the production floor. Even though data from the shop floor can be captured easily thanks to Industrial Internet of Things (IIoT), simulating the production flow for specific processes such as the movement of materials, worker movements and operational schedules requires hands-on knowledge. Therefore, the virtual twin on the 3DEXPERIENCE® platform is an enabler for capturing knowledge and collaboration for better data accuracy.
Let’s look at some of the advantages for manufacturers that utilize the Virtual Twin Experience:
Factory planning
By creating a virtual twin of the entire factory, manufacturers can manipulate and evaluate the placement of infrastructure and resources within a 3D workspace. This allows them to define and validate the layout of their production floors without needing to step inside. They can also avoid costly layout redesigns by enabling users to collaborate and come up with optimal 3D layouts.
Factory layout
Manufacturers can scan the facility and develop a virtual twin of entire factory to optimize the final layout of a complete cell (machine, conveyor and stocker). They can look for potential layout issues and validate the use of robots and machinery before implementation. The virtual twin also minimizes the risk of negative impact on health, personal or environmental performance due to layout decisions.
Production flow simulation
Simulation allows continuous improvement of manufacturing flexibility and agility. Manufacturers can compare factory layouts and multiple production scenarios. They can also optimize process performance by testing alternate product routings and by integrating robotic and human tasks into the production model. To incorporate social distancing into the production flow, manufacturers can evaluate productivity scenarios based on worker capacity and safety distancing norms.
Workplace safety simulation
Enforcing social distancing is part of ensuring a safe workplace in the new normal. Manufacturers must evaluate how workers move through the facility and identify potential areas that could create bottlenecks and avoid unwanted gathering spots. With the virtual twin, they can create a safety envelope around each worker to simulate social distancing and the flow of worker movements through the plant. As a result, manufacturers can adhere to health and safety regulations for workers regardless of country.
Manufacturing operations must become agile in the face of disruptions. Our Virtual Twin Experience. powered by the 3DEXPERIENCE® platform, is designed to ensure business continuity, employee well-being, manufacturing flexibility and reduced short-term costs.
With Virtual Twin Experience, manufacturers can easily plan and evaluate various scenarios based on simulation data, while being compliant to new rules and restrictions. Furthermore, they can leverage cloud solutions to support nearshoring of manufacturing to address supply chain challenges.
To find out more about our Virtual Twin Experience powered by the 3DEXPERIENCE platform, watch our on-demand webinar by clicking here.
Please note, this post by Lucie Drescherova orginally appeared on The DELMIA Blog.