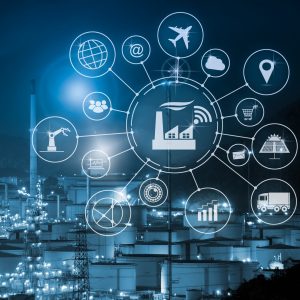
While most people are homebound during the COVID-19 situation, many are still on the frontlines. Essential workers don’t just include hospital staff. This classification extends to the manufacturing facilities and personnel keeping us fed and supplied. These individuals are ultimately helping to turn the tide in the global pandemic.
Doing more with less is more critical in manufacturing than ever. Manufacturers of medical and cleaning supplies, as well as the specialists overseeing trucking, delivery and logistics companies, might have to make do with limited supplies and labor. They might even find themselves conscripted into manufacturing essential products under the Defense Production Act.
As important as this sector is right now, it’s also a significant contributor to material waste and carbon emissions.
Whether you represent a metal fabrication company, a consumer goods manufacturer or a paint, fiberglass or paper producer, you have several ways to make the operation a more sustainable one. Here are a few of them:
1. Perform Energy Audits Regularly
In 2018, the U.S. Energy Information Administration identified the following manufacturing sectors as the largest energy consumers:
- Bulk chemical manufacturing: 28%
- Refining: 18%
- Mining: 12%
Each of these sectors can benefit greatly from frequent energy audits. Audits identify where energy is going to waste in the facility and uncover other opportunities to streamline processes or make changes.
One such change that’s still viable even in the face of a global pandemic is switching to clean energy. Some manufacturers, including Tesla, have shut down the production of solar equipment to focus on medical supplies. Others, like First Solar, are still rolling their products off the assembly line.
2. Replace Equipment and Make Facility Improvements
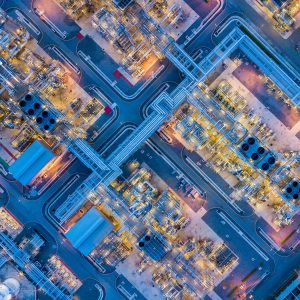
After performing your energy audit, it’s time to single out work zones with wasteful processes and equipment with outsized energy budgets. In-house or third-party reviews identify opportunities to change workflows and make smart investments regarding energy savings. Manufacturers dealing with skeleton crews of essential personnel on the factory floor will be especially keen to use space, energy and labor more economically and efficiently.
Worthwhile investments include adding newer and more efficient machines, as well as replacing lighting and HVAC equipment with automated systems. Checking for worn-out dock seals, window weatherstripping and other areas experiencing unnecessary heat or A/C loss is also a good idea.
Estimates from EnergySage indicate commercial property owners could slash their energy expenses by 75% if they switch to solar. Going this route is a win for the company’s bottom line as well as the natural environment. Automated lighting and HVAC can help as well by ensuring unstaffed areas don’t waste energy.
3. Use a Larger Percentage of Recycled Materials
Any company that wants to make its manufacturing facilities more sustainable must incorporate recycled materials in the supply chain. There are several notable examples of companies that have done precisely this:
- California-based Green Toys recycled some 55 million milk jugs in its first decade in business. The company also uses soy-based ink on its packaging, which breaks down four times faster than petroleum ink.
- Allbirds and Rothy’s specialize in creating footwear that approaches or achieves 100% recycled status. Allbirds uses recycled cardboards and plastics as well as ethically sourced wool, while Rothy’s uses recycled plastics to create breathable, flexible shoes.
- Recover Brands uses waste from its factory floors and recycled third-party materials to create its clothing lines and outdoor gear.
Taking factory-based trash separating and recycling more seriously is the first step. Once the company knows how much and what types of waste it generates, it becomes easier to return these materials to the supply chain.
Alternatively, it may be possible to strike up a partnership with a nearby business. Some farms will gladly take sawdust from mills, for example, because it makes environmentally friendly and inexpensive bedding for animals. So long as mandatory social distancing protocols are observed, essential producers like manufacturers and farmers may find new ways to work together. They may discover many mutually beneficial strategies for sharing resources and supplies and helping each other minimize waste.
4. Switch to Domestic Sourcing or Manufacturing
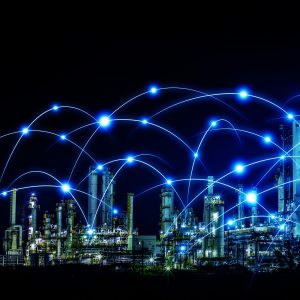
Any business serious about making itself more sustainable should examine its supply chain’s location and length.
Traditionally, moving manufacturing facilities overseas, or sourcing raw materials from afar, delivered cost and labor savings. Today, wages are rising around the globe and trade disputes add uncertainty.
Domestic sourcing and manufacturing are becoming more popular as companies reckon with their carbon footprints and attempt to bring jobs back to their home countries.
Even before COVID-19 subsumed the entire news cycle, these global pressures were causing manufacturers and their vendors to reconsider how they source and transport essential materials. Today, that kind of reconsideration is vital. New restrictions for shipping companies concerning points of origin and freight types may make domestic sourcing an inescapable conclusion.
Of course, when the pandemic is behind us, there will still be many sustainability benefits of going domestic in manufacturing. These include:
- Shorter supply chains are less susceptible to error and rework, which saves time and material resources.
- Transporting raw materials and finished goods across significant distances results in a sizable carbon footprint compared to domestic sourcing and distribution.
- Choosing domestic partners makes it easier to see who’s sticking to their sustainability commitments and who is not.
5. Design Longer-Lasting Products to Create a Circular Economy
Manufacturers and designers have a significant role to play in the circular economy. The circular economy embodies a concept of products designed for long lives, easy repairability and the chance to repurpose them in-house or give them a second life outside the company.
Some clothing manufacturers ensure long lifetimes for their wares by being choosier about the type of thread they use.
Electronics manufacturers create entire secondary markets for refurbished products reclaimed from customers. They study their products’ uses in the field, make it easy for customers to send back used goods and return any unsalvageable material to the supply chain.
Long-lasting product design extends to packaging, too. Companies increasingly find or design shipping and delivery cartons that can be reused before recycling.
Choosing long-lasting plastic pallets instead of wooden ones is just one example. There are others, including applying the “milkman model” to containers, cartons and other products shipped from factories.
It should also be noted that COVID-19 has stressed manufacturers of personal protective equipment (PPE), including face masks, to the breaking point. Responding to the pandemic with products that last through repeated uses will address shortages and keep patients, the public and medical practitioners safe. This process is also a dress rehearsal for the high-efficiency, low-waste supply chain and world economy that climate change demands.
To that end, many PPE manufacturers are designing new types of masks to replace single-use disposable ones. They boast of maintaining their effectiveness even after several uses and sterilizations.
Making the Business Case for More Sustainable Manufacturing
The U.S. Environmental Protection Agency is clear about the link between sustainable manufacturing and business success. Companies that produce less waste and do more efficient work each day:
- Are more stable over the long term compared to their competitors.
- Enjoy more predictable and controllable costs.
- Are better able to cultivate and keep the public’s trust.
- Are better positioned to respond quickly to new local and federal regulations.
From novel product designs to waste reduction and shorter supply chains, taking sustainability seriously in manufacturing is also a great way to keep the manufacturing sector responsive to threats like the coronavirus.
Sustainability is a shared responsibility, but the manufacturing sector has more pull than most. Improving profitability may be the biggest driver of change, but companies can also help the planet by helping themselves. There may be growing pains along the way, but they’re more than worth it for everyone involved. And if the world ever faces another threat like COVID-19, companies that take sensible steps today will be that much better off.
This post by Megan Ray Nichols originally appeared on the The DELMIA Blog.