Philippe Bartissol, VP of the Industrial Equipment industry at Dassault Systèmes, and Morgan Zimmermann, CEO of NETVIBES, explain why virtual twin technology is the next game-changer for manufacturers as they tap into new after-sales revenue streams. They explore how virtual twin experiences can be used to manage complex equipment in operation and optimize its performance.
Picture the scene. An essential piece of machinery in an automotive production line is running with a faulty component. If left undetected, the first time the automotive manufacturer might become aware of it is when the component fails and the line goes down, costing significant time and money. However, thanks to virtual twin technology, the Industrial Equipment manufacturer that built and supplied the machine is able to monitor and track all its operational equipment in the field. It identifies the same issue in another machine and automatically flags up all others that might be affected – fixing the issue well before it becomes a bigger problem.
Virtual twin experiences provide the capability to represent, visualize and explore virtual replicas of products, processes and operations in astonishing detail. This transformative technology empowers companies to model and simulate complex systems, ranging from electric vehicles and aircraft engines to elevators and machinery, to see exactly how they will perform in an almost limitless range of scenarios throughout their lifecycle.
Within the Industrial Equipment industry, manufacturers increasingly use virtual twin experiences to monitor and actively manage operational equipment in the field. This allows them to:
- Revolutionize after-sales and tap into new revenue streams: There is a huge after-sales revolution underway in the Industrial Equipment industry as manufacturers capitalize on new business models such as equipment as a service. The virtual twin supports this by virtually monitoring the behavior, health and performance of equipment in the field so that manufacturers can offer a host of new value-add after-sales services such as performance optimization and real-time assistance to reduce downtime.
- Plan maintenance and repairs: Virtual twin, artificial intelligence (AI) and machine learning (ML) capabilities come together to deliver new levels of predictive maintenance by monitoring and detecting patterns in the behavior of equipment. Thanks to NETVIBES data science solutions, manufacturers can easily locate assets in the field to determine how they perform, any maintenance and repair work they might need, and which parts might need replacing. They can also simulate all manner of scenarios, proactively flag similar issues that may arise in the field and automatically identify spare parts.
- Improve customer satisfaction: In addition to enhanced after-sales capabilities, Industrial Equipment manufacturers can also use the virtual twin to improve how they respond to their customers’ needs. Repairs can be researched and planned by field technicians ahead of time in the virtual twin. They can pull up the right work instructions, identify available spare parts, and take advantage of natural language processing to ask appropriate questions ahead of going onsite, making them much more efficient and ensuring they fix the issue there and then – all the information they need is on screen in front of them.
- Boost innovation: By linking the real and virtual worlds, manufacturers can better visualize and integrate highly complex systems, anticipate issues before they arise, and problem solve to develop a new generation of equipment that is more innovative and sustainable. Learning from past issues and feeding that information back into engineering empowers them to develop equipment that performs better and lasts longer than its predecessors.
Boost performance in the field
The move from generic virtual twins for design and engineering to specific virtual twins linked to specific pieces of increasingly personalized equipment in operation promises to radically transform how Industrial Equipment manufacturers develop and manage their products and serve their customers. Eventually, we’ll see millions of serialized virtual instances of robots, machinery, elevators and more being monitored, optimized and maintained on an ongoing basis.
Through the operational virtual twin experience – connected to each customer order and serial number – manufacturers can manage their entire installed base and see everything that is happening to each piece of equipment throughout its lifespan. This enhances their ability to engage with their customers, presents new opportunities to tap into incremental revenue streams, triggers the right sales opportunity at the right time for the equipment based on its usage, and facilitates the feedback loop to engineering.
Because everybody can see exactly what is happening, manufacturers can leverage the precise engineering and service definitions for each piece of equipment in operation. This empowers them to meticulously plan field technicians’ interventions and promptly narrow down to a particular issue by getting contextual information and looking for similar cases across the installation base, drawing upon current and historical data. And once a change is implemented in the field, it is reflected in the in-operation virtual twin. This approach not only enhances efficiency but also offers a responsive and adaptable solution to ensure seamless operations for OEMs’ field services.
AI and ML capabilities build on this, providing manufacturers with even more opportunities to pre-empt performance issues and detect anomalies of equipment in service to ensure uptime. They’re increasingly able to accurately estimate each asset’s future health status and customize maintenance task planning based on residual life predictions. AI-driven part sourcing and forecasting also improve the way spare parts are managed and stocked. New insights empower manufacturers to standardize parts catalogs, competitively source components and more easily identify opportunities to reuse parts.
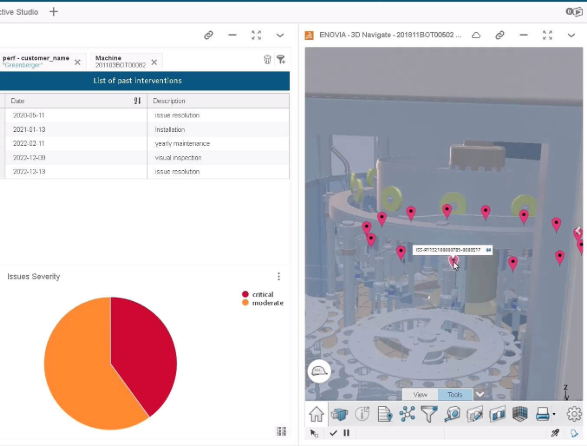
Accelerating the shift to more efficient, sustainable equipment
Virtual twin experiences powered by the 3DEXPERIENCE© platform are already having a positive effect on the way that IE manufacturers develop and manage equipment throughout its lifecycle. As we increasingly move towards sustainable circular economy business models, manufacturers must think even more carefully about the environmental impact of their products, beginning in design with the types of materials they use all the way through to how equipment is operated, maintained and dismantled at the end of its life.
Making more considered choices requires manufacturers to retain comprehensive knowledge of how equipment is designed and engineered, as well as how to repair and replace parts. Within the virtual twin, they can store all this information to transfer knowledge and know-how, and track the health status of equipment and parts to improve reliability, extend their lifespan and, ultimately, boost customer satisfaction.
The same goes for enhancing the operational efficiency of equipment in the field. An endless stream of data coming from the industrial internet of things gives manufacturers a better view of equipment energy consumption and carbon emissions. They can deliver tangible value to their customers by helping them to determine the best times to operate machinery, how fast to run it using minimal resources and how to modify it to incrementally enhance performance and reduce its environmental impact.
We can expect to see more of these types of initiatives gain traction as the emphasis continues to shift towards forward-thinking, customer-centric product development, proactive maintenance and sustainably driven production and operation of industrial equipment. We think you’ll agree that this is a particularly exciting time in the IE industry. And with the most advanced virtual twin and data science capabilities, we are right here to support and accelerate the industry’s transformation.
To learn more about how you can improve the OEE of your equipment in operations, have a look at this article titled Data-Driven Approach to After-sales Services.