There is a good reason why hydrogen is being touted as a key enabler of the transition to a zero-carbon economy. The most abundant element in the universe, hydrogen is a versatile energy carrier, extremely energy dense, light and can be stored for long periods of time. It also produces no carbon emissions, generating only heat and water when burned. However, the vast majority of hydrogen used today is actually highly polluting because of how it’s extracted. Around 96% of hydrogen produced globally is “grey,” which means it’s made using fossil fuels such as coal and natural gas, emitting vast quantities of carbon emissions into the atmosphere. Only green hydrogen, produced with renewable electricity, is a truly clean energy solution.
Green hydrogen is made via a process called electrolysis, where electricity powers an electrolyzer, which splits water into hydrogen and oxygen. For hydrogen to be considered green, the electricity used must come from renewable energy sources such as solar or wind.
Hydrogen is already used across the chemical and refining industries. Breakthroughs in electrolyzer technology mean that it could also become a viable alternative to fossil fuels in the so-called heavy industries, which are more difficult to electrify – think steel and concrete production, long-haul transportation and aviation.
Overcoming the barriers to green hydrogen production
Steelmaking – which also happens to be one of the largest CO2 producers than any other heavy industry – is one of the top candidates for green hydrogen. Through a breakthrough manufacturing process using green hydrogen, it’s possible to create green steel, which could reduce carbon emissions by as much as 95%. However, there is a huge amount of work to be done for green steel to achieve industrial scale. For one, steel manufacturers will need access to abundant supplies of net-zero hydrogen.
McKinsey predicts that demand for green hydrogen could grow to upwards of 600 million metric tons a year by 2050. Today, the total planned production for green and blue hydrogen (the latter of which is produced with natural gas) is around 26 million metric tons annually by 2030.
To successfully scale up green hydrogen, costs need to come down so that it can compete in price with fossil fuels. At the moment, green hydrogen costs up to four times as much as grey hydrogen, ranging anywhere from €3 to €8 per kilogram, compared to just €1 to €2 per kilogram.
Key challenges of green hydrogen production:
- Cost of production
- Scalability
- Electrolyzer efficiency
- Safety
- Cost of equipment maintenance management software
Ramping up green hydrogen production and achieving the necessary economies of scale requires hydrogen makers to rapidly expand electrolyzer capacity. According to the International Energy Agency (IEA), in 2020 global electrolyzer capacity was 0.3 gigawatts (GW). By 2026, global electrolyzer capacity should reach almost 17 GW. Capacities are expected to continue to grow as costs fall and technology developments gain momentum.
The role of virtual twins in building electrolyzers
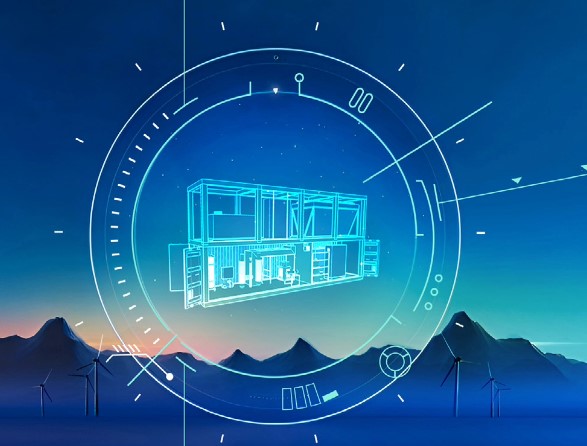
At first glance, the process of creating hydrogen – using electricity to split water into hydrogen and oxygen – seems relatively straightforward. However, electrolyzers themselves are a highly complex piece of equipment that can’t be bought off the shelf. Depending on their use case and type, they can vary significantly in terms of their design, set up and operation, and are usually one of the biggest cost components in green hydrogen production.
Electrolyzer equipment manufacturers must consider everything from material costs, module sizes, set up variability and suitability for specific industrial applications, while taking into account durability and stack degradation rates. Electrolyzers have an expected service life of anything from 5,000 to 80,000 hours, making it essential to have the capabilities to monitor assets throughout their entire lifecycle.
To manage the complexities of designing, manufacturing and running green hydrogen facilities, companies need to be able to model, test and optimize electrolyzers within an entire operation setup in the virtual world. Dassault Systèmes’ 3DEXPERIENCE platform delivers the end-to-end functionality manufacturers need to achieve this.
Using the 3DEXPERIENCE platform’s virtual twin capabilities, hydrogen equipment manufacturers can track the equipment throughout its full lifecycle—from commissioning to maintenance. This enables early integration of maintenance needs, optimization of cell stacks, and virtual testing for structural integrity, pressure, and failure analysis. By capturing all asset data, they can reduce costs, prevent installation issues, minimize downtime, and improve worker safety.
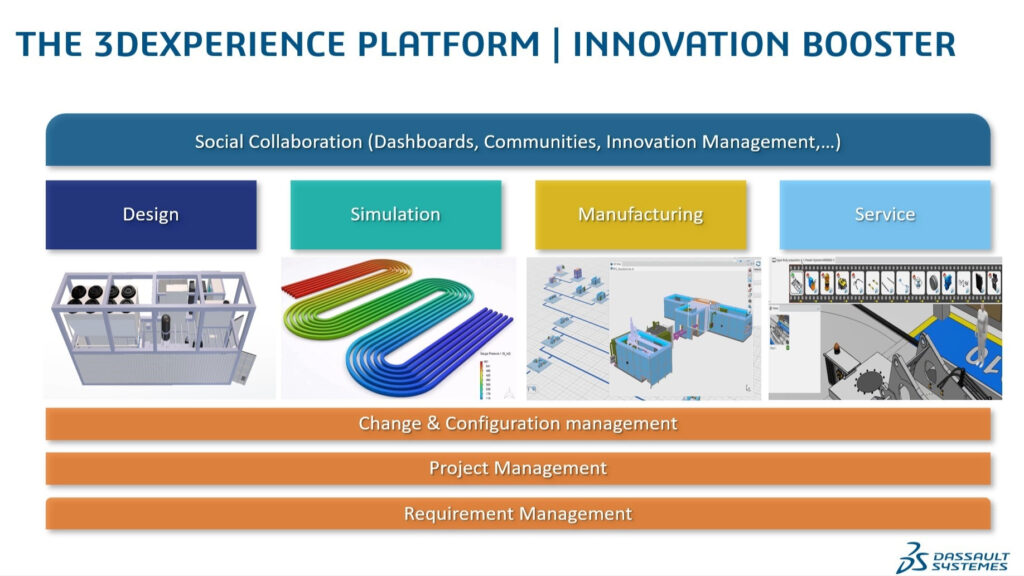
Scaling up green hydrogen production
Green hydrogen targets set out by the likes of the European Union and the United Nations will continue to drive renewable energy capacity globally and help to bring down the associated costs of green hydrogen production. The UN Green Hydrogen Catapult initiative, for example, is almost doubling its goal for green electrolyzers from 25 gigawatts in 2020 to 45 gigawatts by 2027.
Aside from industry cooperation and funding, the industry also needs the digital capabilities to drive product development efficiencies. Companies like McPhy Energy are increasing the competitiveness of their electrolyzers and low-carbon hydrogen refueling stations by managing all their processes on the 3DEXPERIENCE platform on the cloud. This allows them to:
- Standardize processes and design and simulation applications
- Centralize data and project management
- Facilitate collaboration internally and with suppliers worldwide.
- Improve electrolyzer performance, quality and safety
By managing product lifecycles and virtually modeling manufacturing with the 3DEXPERIENCE platform, McPhy aims to reduce time to market and enhance equipment performance.
As the world moves away from fossil fuels, innovation in electrolyzer technology is key to scaling green hydrogen. According to Dr. Emanuele Taibi of IRENA, green hydrogen costs could be halved by 2030, making it competitive and widely available within the next decade.
Watch Experts Reveal Hydrogen Production Insights here