Today, in most industries, product design still relies on multiple design analysis cycles and physical prototyping. The speed of innovation is only as fast as the handover of information between these siloed processes. Unified modelling and simulation, known commonly as MODSIM, promises to change that.
This emerging collaborative approach to design and simulation aims to significantly accelerate design exploration, optimization and validation cycles. And it’s being brought to life by technologies such as the 3DEXPERIENCE platform, which seamlessly brings together the capabilities of CAD and simulation software – CATIA and SIMULIA – within a centralized environment.
What is the purpose of MODSIM?
At its core, MODSIM is about reducing any friction or barriers between two previously disconnected disciplines – modeling and simulation – and making the exchange of data between the two as seamless and convenient as possible. Compared to existing design techniques and methods, it creates a streamlined workflow between design and testing so that companies can experiment with new designs, analyze their performance in limitless real-world virtual scenarios, use those simulation results to inform their designs, and then only take the best, most feasible designs through to the next stage. It essentially means that by time designs are finalized, there should be no surprises further down the line.
The concept of integrated modeling and simulation, sometimes referred to as simulation-driven design, has been around a while. What’s different today is technology like the 3DEXPERIENCE platform brings together all the required CAD and CAE tools so users can carry out both design and simulation within a common environment. This removes the need to switch between applications or export, import and convert data. The result is more innovation. Companies now have an opportunity to develop highly optimized products without having to expend vast resources on physical prototypes, meaning they can launch better products to market faster than ever, and reduce waste and costs in the process.
Key benefits of MODSIM
Providing a continuous, digital thread between modeling and simulation brings about greater synergies between designers and analysts. Design models and simulation results are fully associated with each other, which means that simulations can directly inform design features and parameters, and any changes between the two automatically update. This makes it easier and faster to try out new designs and test their feasibility.
Companies that adopt a MODSIM approach can expect to achieve a variety of benefits:
- Faster time to market: Dramatically reduce development time from months to weeks
- Reduce physical prototypes: Bringing simulation early into the concept phase allows designers to test form and function and reduce the need for costly prototypes
- Lower costs: Companies report the ability to improve efficiency by up to 40% and reduce overall costs by around 8%
- Boost innovation: By embedding simulation within the design process, engineers can accurately predict product behavior and develop more complex designs faster
- Avoid late-stage errors: MODSIM brings verification and validation earlier into the design phase, reducing the risk of costly late-stage failures and rework.
How MODSIM supports sustainability
Across all industries, the sustainability imperative has become a critical business driver. It’s forcing companies to adapt in many ways, from embracing circular economy principles to sourcing renewable raw materials and energy. At the same time, products are becoming more complex, requiring the integration of mechanical, electrical and software disciplines.
Both the need to become more sustainable and develop increasingly sophisticated products ultimately requires more testing and validation throughout the product development cycle. And it’s important that’s done at the earliest possible stage, not just in terms of keeping costs under control, but also for embedding eco-friendly principles into product designs.
“80% of a product’s impact on the planet is defined in the concept stage,” said Olivier Sappin, CEO of CATIA, as he opened the 2022 MODSIM Conference. “We need to concentrate on the design, modeling, and simulation stage to reduce that.”
By introducing simulation into the design process, designers and product developers gain the insights they need to balance sometimes conflicting requirements, make the right tradeoffs and put sustainability at the core of what they do.
In the consumer packaged goods (CPG) industry, for example, designing more sustainable packaging has become a high priority for virtually all companies. This can mean everything from using new, sustainable materials, consuming fewer materials, or developing entirely new packaging designed exclusively for ‘direct-to-consumer’ ecommerce. Through MODSIM, companies can test their products in unlimited virtual scenarios so that they have a better understanding of how they’ll perform in the real world and get answers to the following questions:
- For new materials: Will the package protect the product adequately? Will the shelf life be impacted? Will it recycle or biodegrade appropriately? Will the weight change? Will the new material alter the performance of the formula inside. Will the material ‘bleed’ into the formula or change the smell? Will the consumer usage of the product be impacted?
- For material weight: Can less material be used and still protect the product? Will it hold up during transportation? Can the walls be made thinner? How much packaging is needed to survive the increases in ‘touches’ in a warehouse environment?
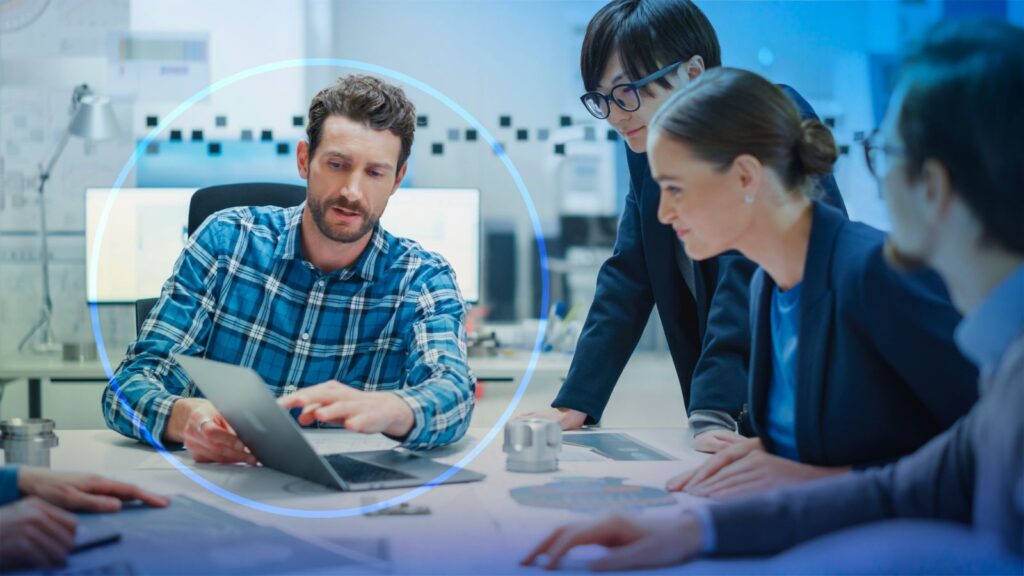
How Dassault Systèmes supports a MODSIM approach
The 3DEXPERIENCE platform brings MODSIM to life through its ability to integrate all product development functions in one centralized environment. All disciplines across an organization can access the modeling and simulation tools they need, and because everything is linked to the product lifecycle management (PLM) system, there’s no need for wasting time sourcing the data inputs for simulation and analysis. This connectivity not only boosts productivity, but also ensures that only the right data is used at all times.
Some of the world’s most innovative companies already rely on the 3DEXPERIENCE platform for MODSIM as they look to accelerate their product development cycles. From household brands to leading automotive manufacturers, there’s a clear trend in recognizing the power of an integrated approach to modeling and simulation as a way of boosting competitive edge.
Helix: Operating at the cutting edge of the automotive industry, Helix has built a reputation on its ability to develop high-performing electric motors and inverters and bring them to market as fast as possible. Through MODSIM, the UK company can bring simulation early into the design process, which helps to accelerate design cycles, reduce development costs and supports engineers to understand more about the product they’re working on. They can test several different designs, see how they perform virtually and then select the best ones to take to the next product development stage.
Metsä Board: The Finland-based paperboard producer uses the 3DEXPERIENCE platform’s MODSIM capabilities to simulate advanced packaging designs and validate them with the click of a button. These capabilities underpin a new 3D simulations service available to Metsä Board customers, where the company creates virtual twins of its customers’ existing packaging solutions and compares their performance to new packaging solutions in a variety of simulated environments. It’s helping to improve packaging designs and lower their overall environmental impact.
PepsiCo: Through MODSIM and advanced rapid prototyping, the popular soft drinks maker is saving hundreds of thousands of dollars per year and improving productivity and quality across several of its packaging development processes. By bringing simulation in house, PepsiCo can focus on developing more sustainable packaging solutions without compromising on robustness.
Renault: The automotive manufacturer uses an integrated modeling and simulation workflow to accurately predict the behavior of its vehicles, size each component, and quickly optimize technical definitions. By bringing simulation into the hands of its designers, Renault is successfully shortening design loops and achieving a seamless digital flow across its design, requirements and simulation models.
Unilever: As one of the world’s largest consumer goods companies, Unilever is constantly looking for ways to improve its packaging and become more sustainable. High up on its agenda is plastic reduction, and the company uses MODSIM to progressively optimize its designs and reduce material usage. Through MODSIM, its design engineers can test more variables and more quickly refine their designs.
MODSIM, as explained by Unilever packaging excellence leaders Mel Creasey, is about more than simply helping people work more productively and save their company money. It provides an opportunity to do things better.
“Advanced modeling and simulation approaches are proving key to supporting our teams as they look to address increasingly complex challenges and successfully balance conflicting requirements,” said Creasey. “By being able to test more, you can refine and improve and optimize that design to the next level.”
Learn more: