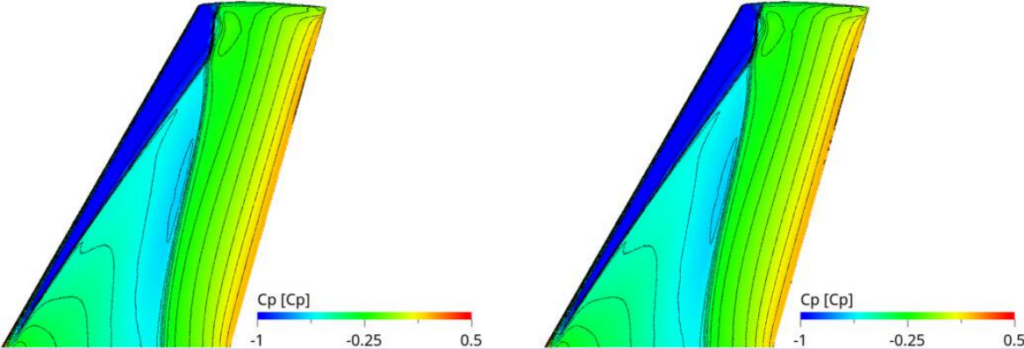
Why Does Transonic Flow Require Special Simulation Techniques?
In fluid dynamics, the speed of sound in a medium is one of the most important parameters. The speed of sound, Mach 1, marks a sharp threshold in the behavior of flows, and the transition region (typically Mach 0.8 to Mach 1.2) is known as the transonic region. Hallmarks of transonic flows include high compressibility, much higher drag and the formation of shock waves. Airliners typically cruise at Mach 0.8 or above, and the airflow locally around structures like engines and inlet ports can exceed Mach 1.0. Understanding transonic flows is crucial to understanding the aerodynamics and noise profile of aircraft.
Computational fluid dynamics (CFD) can be used to simulate air flows around bodies such as aircraft. Well-established methods exist for simulating subsonic (below Mach 0.8) and supersonic (above Mach 1.2) flows. However, the transonic region is more challenging, especially as subsonic and supersonic flows can coexist. The simulation methods for subsonic flows cannot capture the behavior of flows around and above Mach 1, while the methods that can simulate highly-compressible flows have much higher computational costs and can suffer from increased numerical dissipation (Figure 1).
To tackle this problem and allow transonic flows to be simulated accurately but efficiently, SIMULIA PowerFLOW has introduced a new hybrid simulation method specially designed for the transonic region.
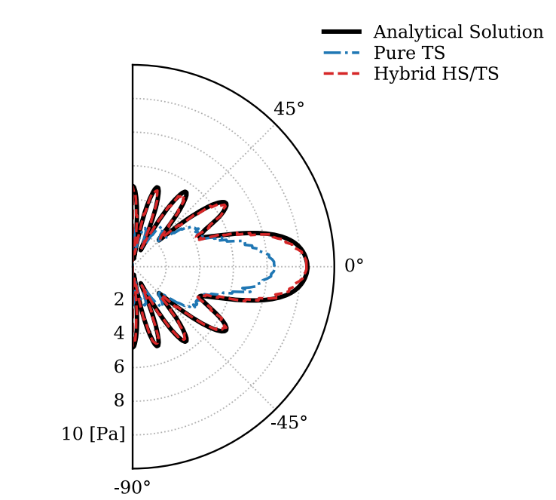
Transonic Simulation in SIMULIA PowerFLOW
SIMULIA PowerFLOW is an industry-leading CFD tool widely used for aerodynamic and aeroacoustic simulation in industries such as aerospace, automotive and wind energy. PowerFLOW uses the Lattice Boltzmann method (LBM) technique with Very Large Eddy Simulations (VLES). LBM is an efficient and accurate method for simulating flows around large and complex geometries.
There are different formulations of LBM tailored for the simulation of different types of flow. High-subsonic (HS) flows that are weakly compressible can be simulated by single-layer lattice models, while multi-layer lattice models are more suitable for the highly compressible transonic (TS) flows above Mach 0.95.
To allow the efficient simulation of transonic flows, PowerFLOW has recently introduced a new hybrid solver method. This uses the TS solver with high-order multilayer lattices only in specific regions with high-speed TS flow, while using the HS solver with a regular single-layer-speed lattice in the rest of the simulation domain containing low-speed flows. The interface between the two guarantees conservation of mass, momentum, and energy, and gives accurate flow transition between fixed and rotating reference frames and meshes. This ensures robust, reliable hybrid simulation.
Hybrid HS/TS simulation offers results that are in line with both experiments and with the results from a full TS solver simulation (Figure 2 and 3), at much lower computational cost. In some cases, it offers even more accurate results due to the lower numerical dissipation (Figure 1). For more information about the implementation, see the paper “Hybrid Lattice Boltzmann Approach for Simulation of High-Speed Flows”.
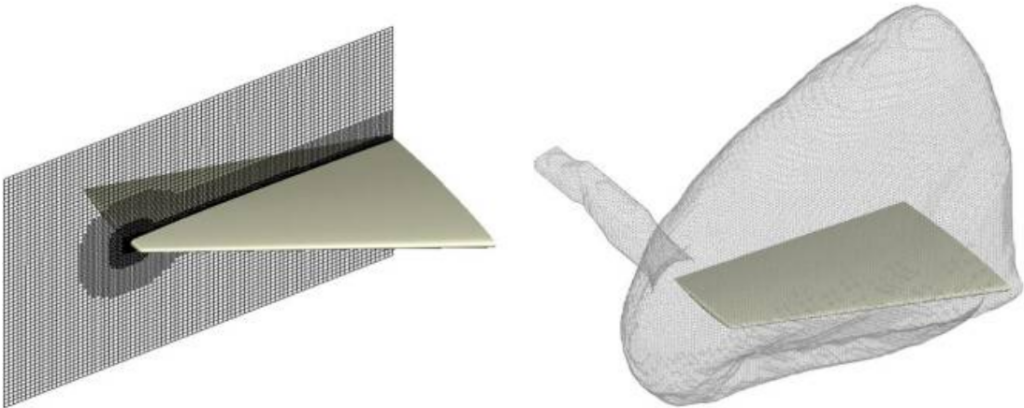
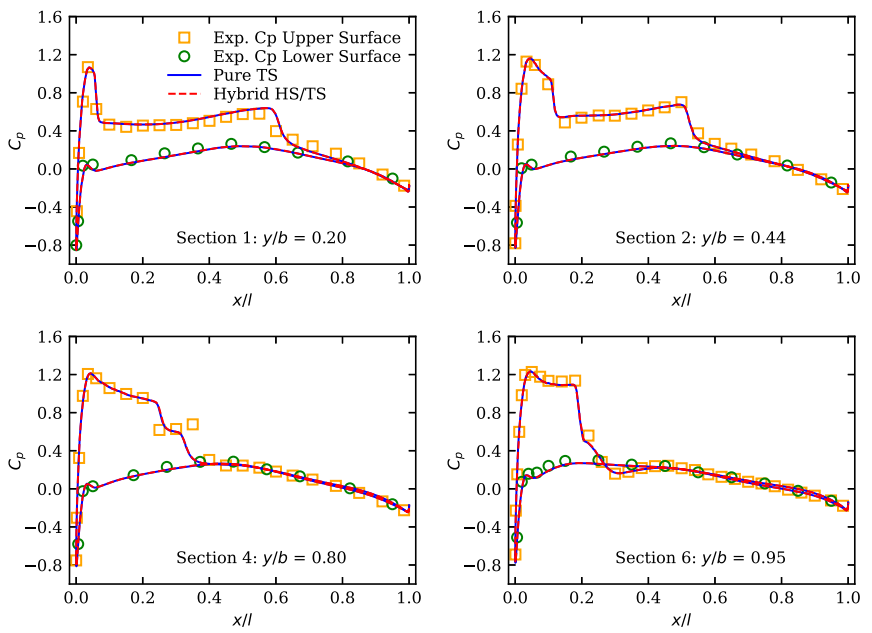
Applications of Hybrid Simulation of Transonic Flows
This hybrid simulation approach has many applications for aerodynamic and aeroacoustic challenges. For instance, aircraft community noise is a significant concern for airlines and airports. Opposition from local communities due to noise often leads to limitations being placed on airports such as reduced operating hours or restrictions on certain aircraft. Careful design can reduce noise and increase community acceptance of aircraft.
Noise is often a result of transonic phenomena, and hybrid simulation helps simulate it accurately and efficiently. One example where this hybrid approach is very useful is for the analysis of cavities on aircraft. Resonances inside cavities – for example, ducts or other openings – can produce significant noise and also cause oscillations that lead to fatigue failure.
The Mach number across the simulation domain can vary significantly, with local supersonic and subsonic flows. Complex flow behavior can arise within the cavity. Supersonic jets of air cause Mach wave radiation, where eddies propagate convectively with supersonic velocity relative to the surrounding gas. These lead to shear-layer instabilities with supersonic phase velocity.
Using the hybrid solver reveals these effects accurately and efficiently. For example, it can be used to model shock-induced buffeting around an airfoil or an aircraft. This is an inherently transonic phenomenon and requires simulation of subsonic and supersonic flows. The simulation results for shock-induced buffeting show close agreement to experimental data on standard benchmarks. For more information, see the published paper “Buffet Simulations with a Lattice-Boltzmann based Transonic Solver”.
Another application is for turbofan engine noise. The fan tips inside the engine can reach or exceed Mach 1.0 at full speed. Very slight variations in the orientation, position and geometry of the fan blades disrupts the symmetry of the airflow. This leads to interference within the engine and, when the blade tips reach sonic conditions, subharmonic components are radiated from the engine intake as multiple pure tones (MPT) – also known as buzz-saw noise.
Simulating buzz-saw noise requires the entire engine to be modeled, with random variation in the fan blades. Using the transonic solver, we were able to simulate transonic buzz-saw noise for the first time as part of a NASA Research Announcement project. To discover more about this project, see our paper “Fan Tonal and Broadband Noise Simulations at Transonic Operating Conditions Using Lattice-Boltzmann Methods”.
Conclusion
Simulating air flow in the transonic domain – for example, around aircraft and engines operating around Mach 0.85 – can be challenging. There are often regions of subsonic and supersonic flow, which are each best solved by different methods. PowerFLOW offers hybrid simulation methods, dividing the simulation domain so the best method can be used for each section of the flow. The PowerFLOW approach ensures that the interface between simulation volumes conserves mass, energy and momentum and gives an accurate flow transition. This makes the hybrid solver accurate and robust, while also reducing the computational cost and simulation time required. Published articles show a close agreement between the PowerFLOW hybrid solver and experimental data for standard benchmarks.
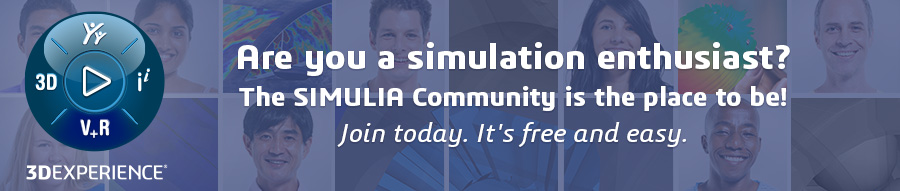
Interested in the latest in simulation? Looking for advice and best practices? Want to discuss simulation with fellow users and Dassault Systèmes experts? The SIMULIA Community is the place to find the latest resources for SIMULIA software and to collaborate with other users. The key that unlocks the door of innovative thinking and knowledge building, the SIMULIA Community provides you with the tools you need to expand your knowledge, whenever and wherever.