Introduction
Industry Analysts are predicting that vehicle miles traveled globally will double to 20 trillion miles by 2030. The trend towards CASE – Connected, Autonomous, Shared and Electric – mobility will drive this growth as the number of shared vehicles is expected to increase total vehicle utilization, even though new vehicle sales may decrease. Tire Original Equipment Manufacturers (OEMs) and Vehicle OEMs are always looking to satisfy customer demands, while optimizing their supply chain, accelerating innovation to remain competitive, offering TaaS (Tire as a Service), better manage raw materials (performance and cost) and increase their operating margin by reducing their production costs.
The advanced methods development detailed herein, for Cleat Impact, enables Tire OEMs and Vehicle OEMs to comply with ever-increasing regulations like:
- Virtual Tire Submission: exchanges between tire manufacturers and vehicle OEM with IP control. This includes reduced-order tire models for vehicles dynamics concept evaluation and compliance. In case exchanges are not possible, this set of solutions includes tire reverse engineering for vehicle OEMs.
- National Highway Traffic Safety Administration (NHTSA) Performance Requirements: including multibody simulation for full vehicle dynamics with full fidelity modeling as well as component level response (impact to chassis).
Moreover, this workflow i) enables rapid development of reduced-order tire models for vehicle dynamics simulation and vehicle durability assessment, and ii) minimizes late-stage design changes.
This blog will be organized as follows:
- Results Primer
- Materials and Elements
- Reinforcements
- Methodology
- Option-1: Abaqus/Standard *SST Free-Rolling to Abaqus/Explicit
- Applicable for only Ribbed Tire geometry
- Methodology and Results provided
- Option-2 (Stay-tuned!): Abaqus/Standard Centrifugal Loading to Abaqus/Explicit
- Applicable for both full 3D Tread geometry and Ribbed Tire geometry
- Methodology provided. Results will be provided at a later date.
- Option-1: Abaqus/Standard *SST Free-Rolling to Abaqus/Explicit
- Conclusions
Results Primer
This Workflow provides very good correlation with experimental results, per image below.
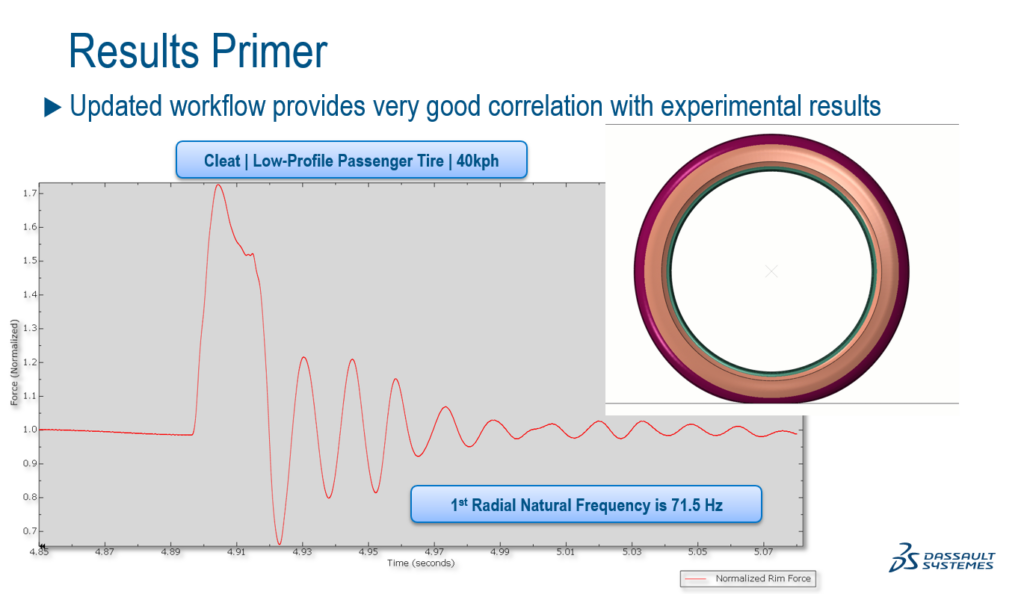
Materials, Reinforcements and Elements
The hysteretic response is shown below for a typical Tread Cap compound.
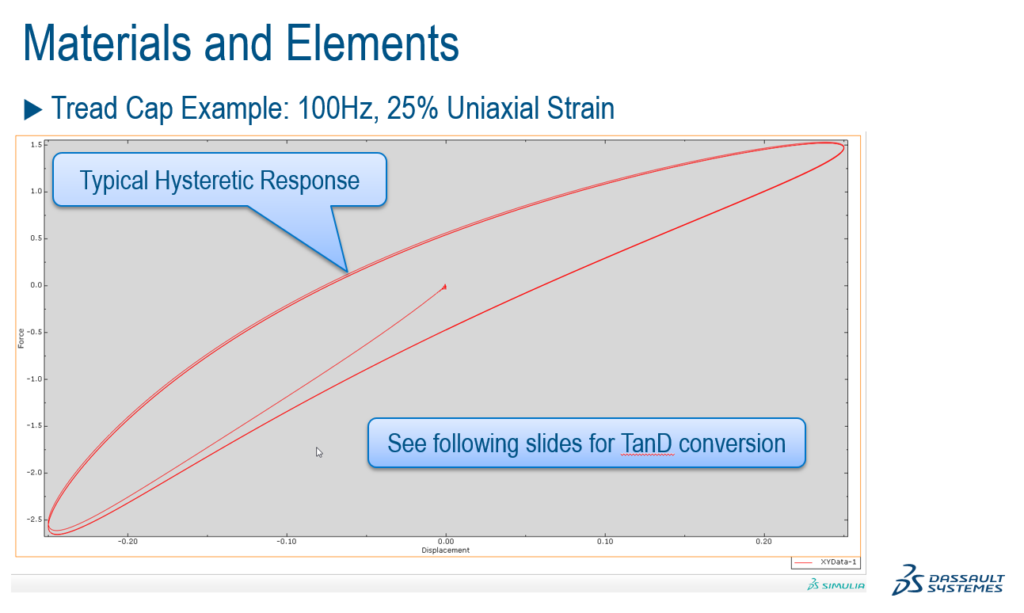
Materials and Elements:
- Updated Model
- Hyperelasticity: Neo-Hooke. Employed to eliminate variability and accelerate fundamental understanding.
- D1 defined à nu = 0.49 for all elastomeric compounds. This is quite typical and eliminates the need for Hybrid formulation elements.
- Solid, reduced integration, non-hybrid elements employed
- Surface elements employed for reinforcements
- *ELEMENT,TYPE=SFMGAX1
Materials
Hyperelastic response: if one curve-fits the data provided in [Engineering with Rubber 3E: How to Design Rubber Components, Book by Alan N. Gent], we can easily create neo-hooke C10s from Shore-A.
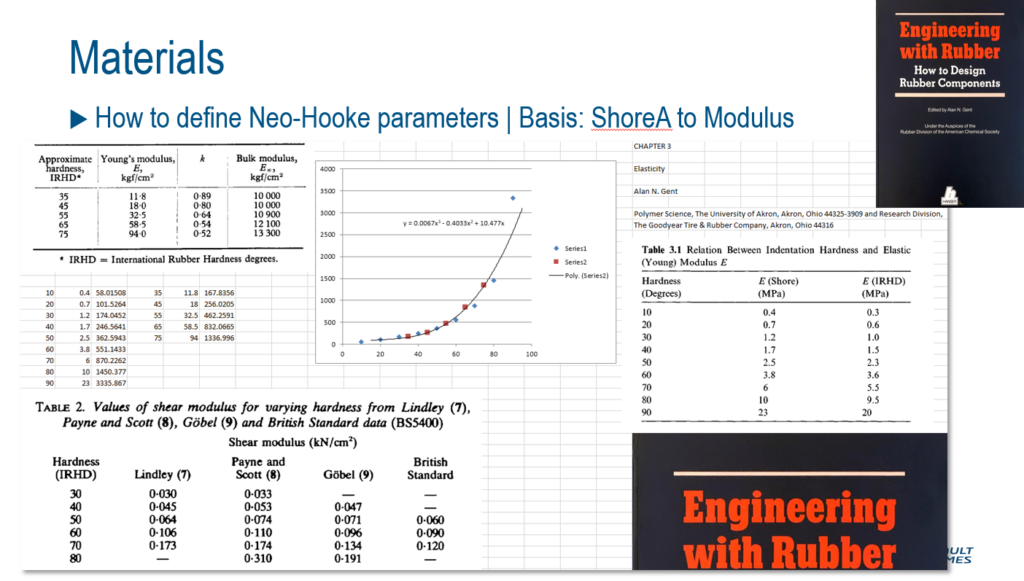
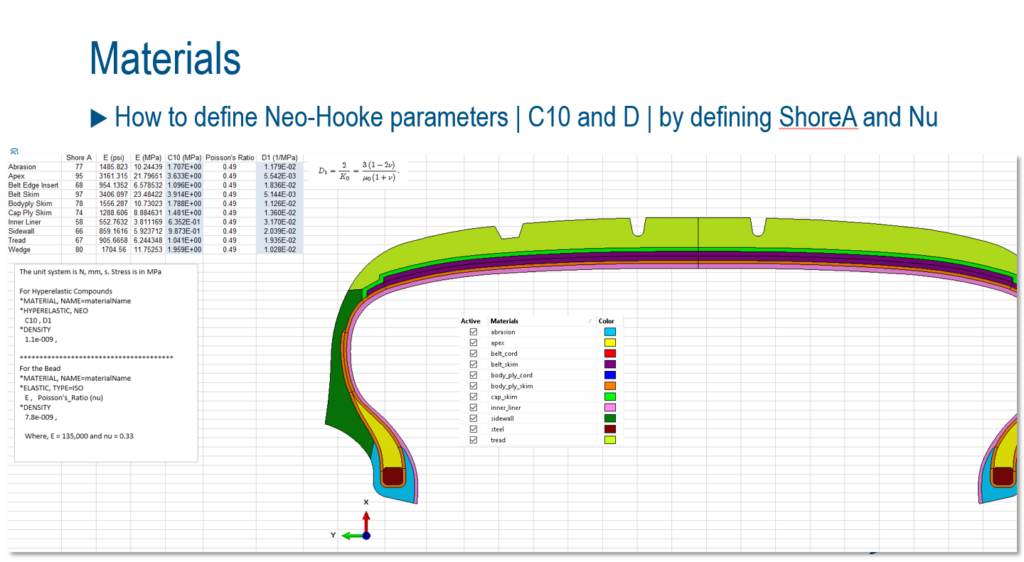
Viscoelastic response: we will generate a PRF material model for the abrasion, apex, belt-skim, bodyply-skim, cap-skim, inner-liner, sidewall and tread via conversion from a 2-term Prony model. The frequency domain and TanD representation is shown below, along with the G and Tau table used to create it. The first image is the Prony response, the second image details the conversion process.
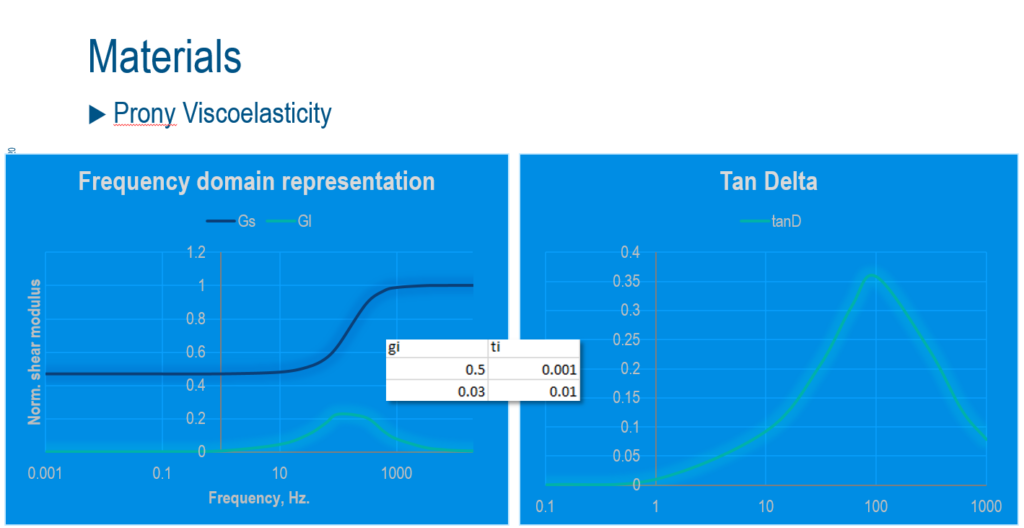
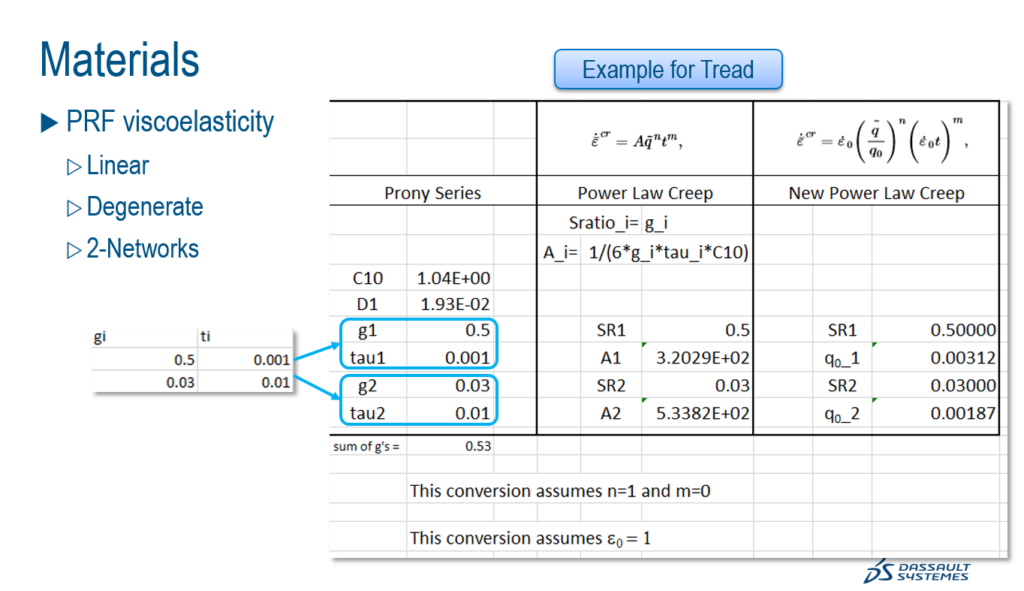
Stay-tuned! I will add more information about reinforcement behavior, bending in rebars and tension-compression behavior in 1Q2023.
Methodology | SST2XPL | Abaqus/Standard *SST Free-Rolling to Abaqus/Explicit |
- Abaqus/Standard | Axisymmetric
- Run with *STATIC, LONG TERM
- Ensure proper *SECTION CONTROLS for solid elements (both elastomeric and reinforcement)
- Step-1
- Rim-mount and inflation
- Step-2
- Change Friction from 0.02 to 0.6
- Abaqus/Standard | 3D Footprint | *SMG *SRT
- *SMG à *SYMMETRIC MODEL GENERATION
- *SRT à *SYMMETRIC RESULTS TRANSFER
- Run with *STATIC, LONG TERM
- Step-1
- Do-nothing equilibration step with completely consistent boundary conditions from axisymmetric state
- Step-2
- Displacement control
- Step-3
- Load control
- Abaqus/Standard | 3D SST | *SMG *SRT
- Run whilst including viscoelastic effects
- Step-1
- Braking
- Step-2
- Find free-rolling conditions via subroutine
- Abaqus/Explicit | 3D | *IMPORT Abaqus/Standard 3D state
- *IMPORT, STATE=YES, UPDATE=NO (Python script developed for ELSETS import)
- Execute in a single Step
- Velocities are imported by default
- Instantiate the road at the correct vertical position from free-rolling SST
- Apply translational velocity to the road
- Remove rim contact and declare Bead and rimNodes as rigid body. Next image to detail
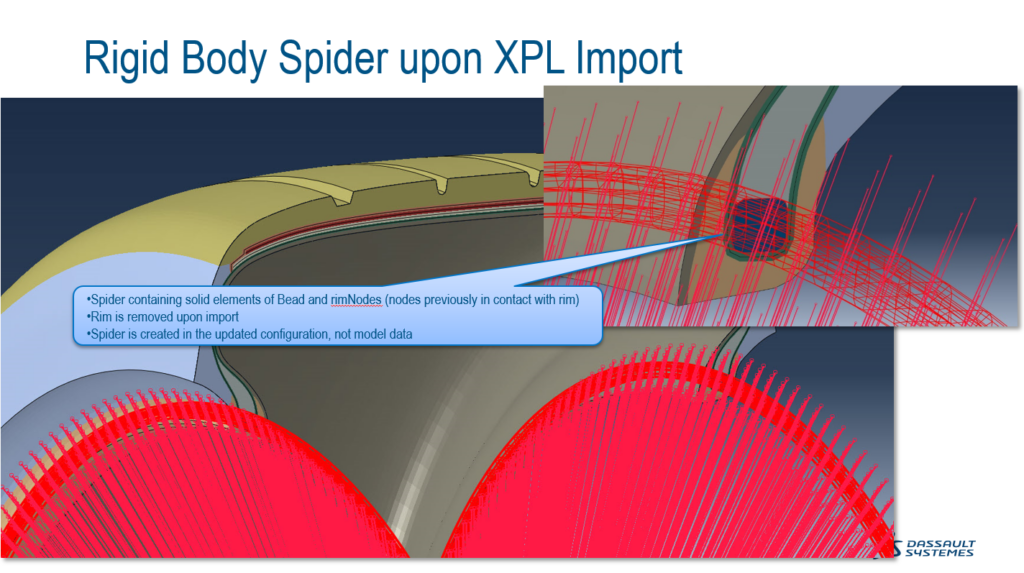
Results
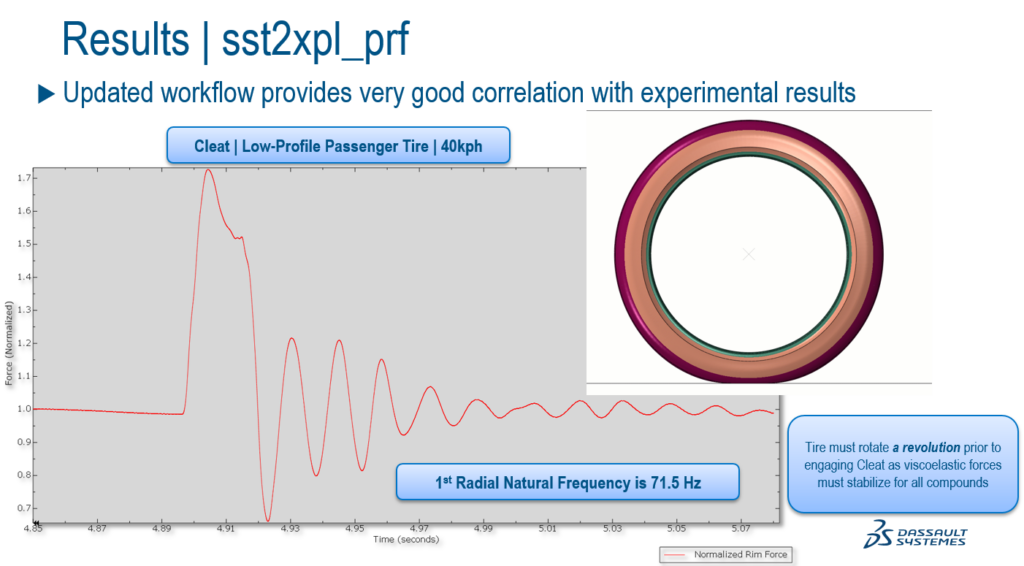
Conclusions
- Two (2) Methodologies have been presented (Stay-tuned for Option-2); both of which show excellent correlation with physical test data.
- Option-1: Abaqus/Standard *SST Free-Rolling to Abaqus/Explicit
- Applicable for only Ribbed Tire geometry
- Option-2 (Stay-tuned): Abaqus/Standard Centrifugal Loading to Abaqus/Explicit
- Applicable for both full 3D Tread geometry and Ribbed Tire geometry
- Option-1: Abaqus/Standard *SST Free-Rolling to Abaqus/Explicit
- Accurate and realistic Viscoelastic material properties are essential, for all compounds.
- Stabilized rolling must be achieved prior to engaging Cleat
To wrap-up: The advanced methods development detailed herein, for Cleat Impact, enables Tire OEMs and Vehicle OEMs to comply with ever-increasing regulations like:
- Virtual Tire Submission: exchanges between tire manufacturers and vehicle OEM with IP control. This includes reduced-order tire models for vehicles dynamics concept evaluation and compliance. In case exchanges are not possible, this set of solutions includes tire reverse engineering for vehicle OEMs.
- National Highway Traffic Safety Administration (NHTSA) Performance Requirements: including multibody simulation for full vehicle dynamics with full fidelity modeling as well as component level response (impact to chassis).
Moreover, this workflow i) enables rapid development of reduced-order tire models for vehicle dynamics simulation and vehicle durability assessment, and ii) minimizes late-stage design changes.
Join a community of simulation enthusiasts focused on advancing the use of SIMULIA simulation solutions in science and engineering! It’s free and easy. Start a discussion with other members of the SIMULIA Community. Talk through your simulation questions with peers, SIMULIA experts, and SIMULIA Champions. Apply to be an author to create posts, share useful tips you discovered for SIMULIA software, and establish yourself as a thought-leader. The SIMULIA Community is home to both SIMULIA product users and SIMULIA subject matter experts around the world.