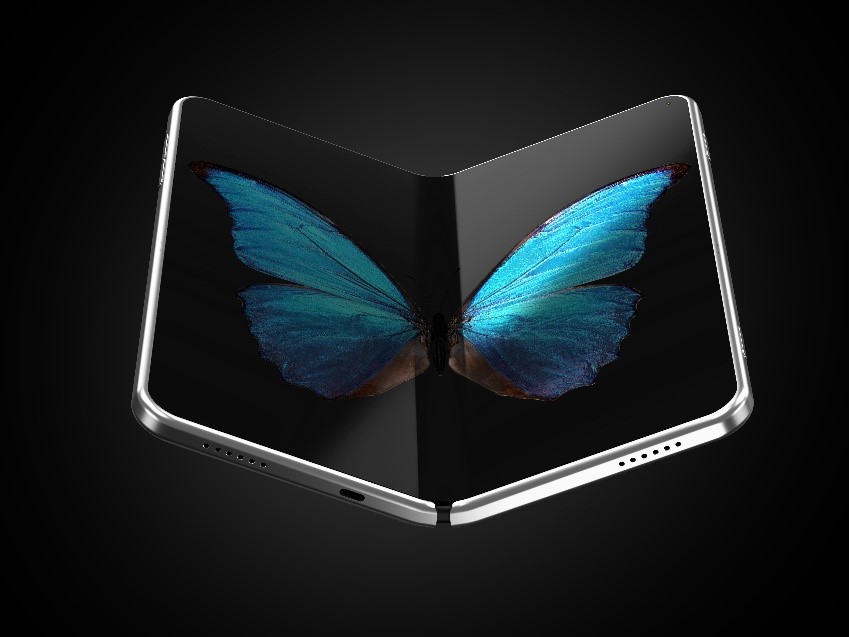
We see more foldable screens appearing in the market for smartphones and larger devices. Designers face new types of challenges because foldable displays are typically built with multiple, flexible functional layers, bonded with optically clear adhesives (OCAs). Any of the individual functional layers can fail, either by plastic deformation, or cracking, including the cover glass. Damage to the electrical structures within each layer can also occur.
In addition, each of those layers is bonded together with OCAs which can de-bond or de-laminate, creating an opaque area in the display, as was seen in some of the early foldable phone designs. It’s critical to model and simulate the folding action of the screen so that each one of these phenomena can be investigated during the design phase of the device.
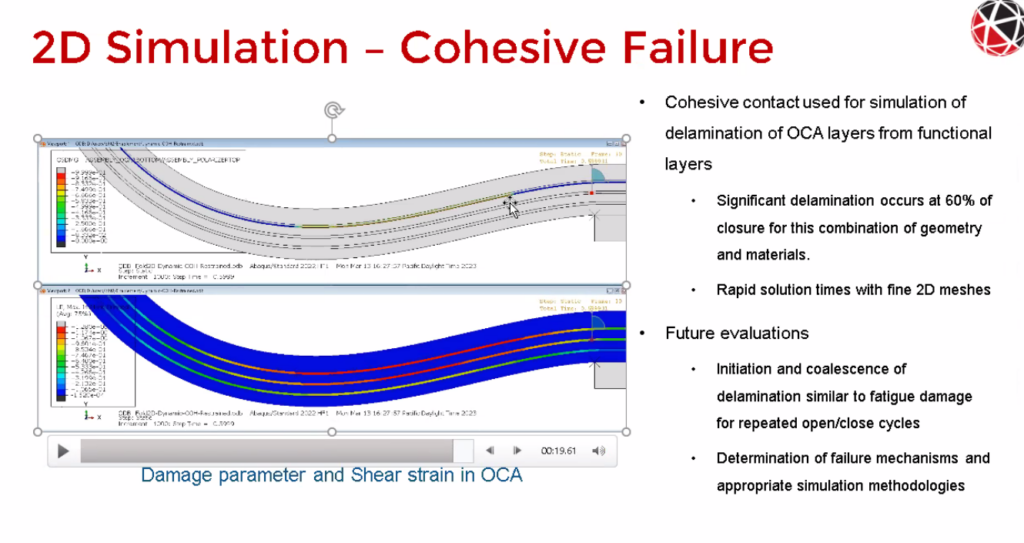
Design of Experiments
Designers can mitigate these potential types of failure using simulation to evaluate each situation. Using multiple design variants, designers can change the thickness of individual layers and the layer stack-up, and explore various materials for each layers. Parameter studies and design of experiments (DoE) can be used to explore the design space while staying within the constraints of the industrial design. DoE is a simulation technology that allows designers to use statistical analysis to achieve an optimal design.
Device Virtual Twin
Hardware prototypes for devices are typically very expensive, particularly in areas around innovation where many iterations might be expected. Creating a device virtual twin, is essential so that as many of those iterations as possible can be done in software, at much lower cost and quickly. The virtual twin of the smartphone uses either the full 3D model or a 2D representation of the screen component and then runs a detailed simulation of the folding and unfolding processes. Fully parametric CAD can enable a full range of design variants to achieve the optimal outcome using DoE. It is a very powerful methodology to use when running both full-scale system simulations and detailed component simulations. Once the designer is happy with the design of the individual flexible screen, they can go back and re-use the component for use in a large-scale smartphone model.
Dwell Time Effects
An important consideration with foldable screens is the assessment of the time dependent material properties of the OCAs, causing dwell time effects. This is when the phone is left in a certain position for an extended period of time.
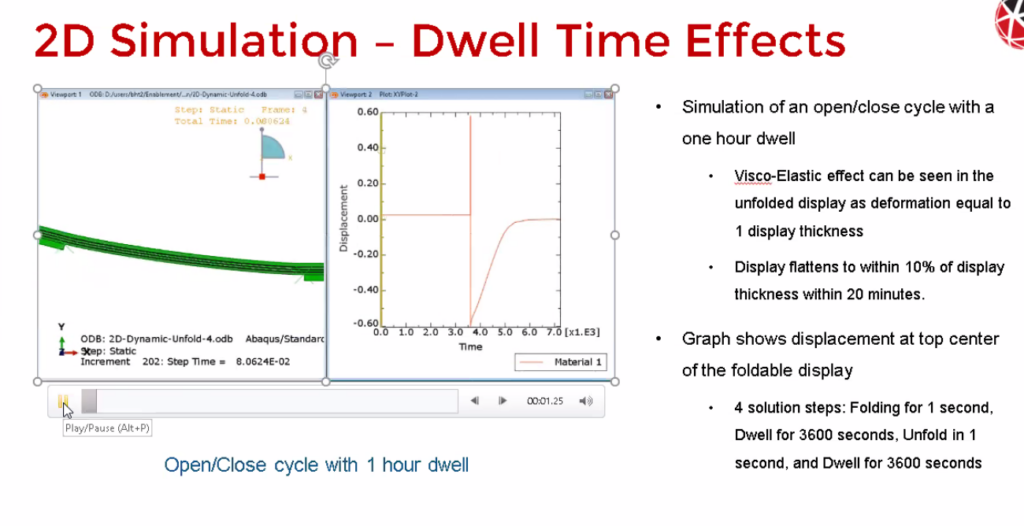
OCAs have two different types of unique material properties that must be considered. The first are hyper-elastic materials, characteristic of incompressible materials, such as rubbers. These need to be modeled to take account of large strains that the OCAs experience during a full bend. The second is viscoelastic materials. Here the materials deform not truly, linear elastically, but in a viscous manner when the screen is folded. This property is exhibited when a smartphone screen stays closed overnight and does not return to its full flatness immediately upon opening. A dip or a trough in the fold of the screen is created that flattens over time. In simulations the time range was found to be anywhere from 20 min to over an hour and is highly dependent on the type of viscoelastic material used.
Screen Hinge
In addition to adhesives, the shape of the foldable screen hinge must be considered. The initial designs for many foldable screens were standard U shapes with parallel screens. This created a single curvature, which is used in testing to obtain material properties. The basic curve means stress predictions are straightforward. The problem with the U shape is that it creates a significant gap between the screens, which is undesirable in a modern device where space is at a premium and device thickness and bulk is an important deciding factor for consumers.
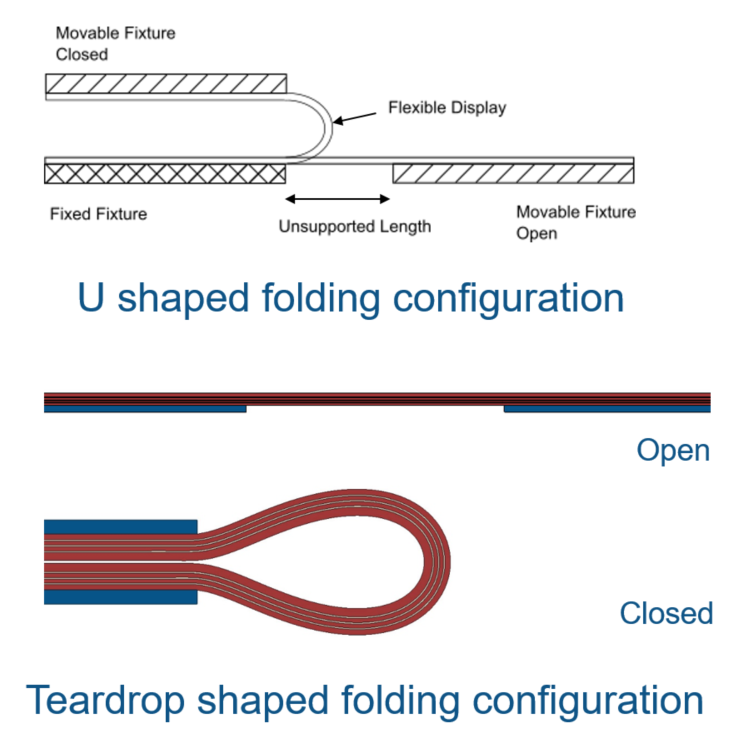
A solution is to use a more complex double curvature such as a teardrop shape, so that when folded, the two screens are effectively touching, with only a small gap between them. In this scenario, the overall device is much thinner with the only wasted space being inside the teardrop itself. This type of structure has a much more complex closing mechanism with potentially high shear stresses between layers that can cause delamination. Simulation in both 2D and 3D helps to create the optimal combination of shape, structure and materials to ensure that the screen can withstand thousands of operating cycles.
Learn more about structural performance validation.
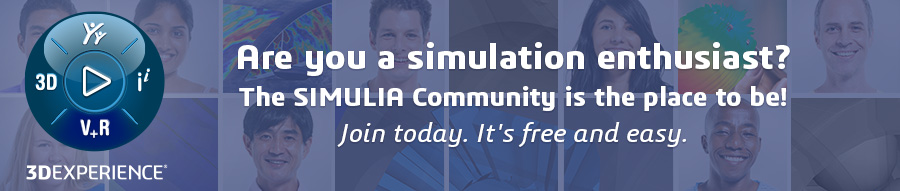
Interested in the latest in simulation? Looking for advice and best practices? Want to discuss simulation with fellow users and Dassault Systèmes experts? The SIMULIA Community is the place to find the latest resources for SIMULIA software and to collaborate with other users. The key that unlocks the door of innovative thinking and knowledge building, the SIMULIA Community provides you with the tools you need to expand your knowledge, whenever and wherever.