Introduction
The strength and integrity of a propeller is mission-critical for any marine application. Damage to the propeller can significantly impact the speed and maneuverability of a ship. Additive manufacturing, particularly the wire-arc additive manufacturing (WAAM) technique, has emerged as a way to not only construct propellers but also to repair them efficiently and cost-effectively.
Before additive manufacturing can be implemented in an industrial workflow, engineers must have confidence that the manufactured part will meet the requirements and specifications. Simulation can calculate and analyze the performance of the part in real-world conditions, but to take advantage of this, engineers must be sure that the simulated model matches the final part. Traceability with the digital thread provides a connection between the simulation model and the manufacturing data.
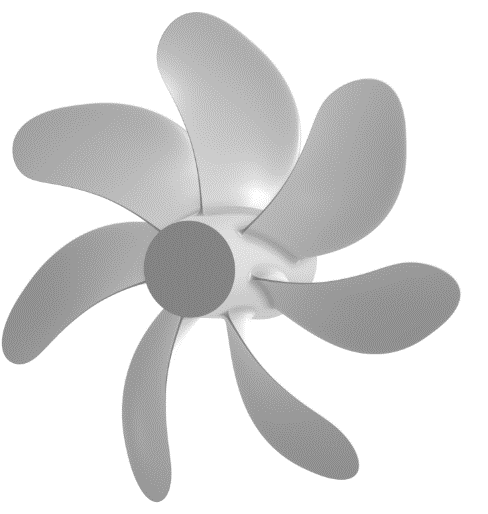
In this blog post, we will present an additive manufacturing workflow on the Dassault Systèmes 3DEXPERIENCE platform. This workflow uses simulation to optimize parameters and calculate temperatures and stresses inside the propeller, to reduce the risk of failure and expedite the testing process. This simulation is part of a digital thread, allowing traceability.
How is additive manufacturing used in the marine & offshore industry?
The American Society for Testing and Materials (ASTM) defines seven categories of additive manufacturing (AM). Two that are particularly widely used in marine & offshore (M&O) are powder bed fusion (PBF) and directed energy deposition (DED). In PBF, the part is built layer by layer from particles of metal powder, melted by a laser. In DED meanwhile, a direct energy source melts material layer by layer. The print head is fed with powder or metal wire, and can be rotated to any angle. The makes DED well suited to repairing damaged parts.
DED, and the wire arc additive manufacturing (WAAM) method especially, have demonstrated promising results for propellers in several projects. Maintenance is a particular advantage of AM – if damage occurs to a propeller in use, the damaged part can be ground away and re-printed. AM can also reduce weight by allowing strong hollow structures. This helps to reduce fuel consumption and therefore cut operating costs and increase sustainability.
How does simulation help the additive manufacturing process?
Additive manufacturing is a dynamic process, meaning the quality of the build depends not only on the structure as a whole but also the interaction of each layer of material with the one below and above at different stages of cooling. As the part cools, thermal expansion causes it to contract. This leads to a complex residual stress within the part.
Simulation can be used to model the AM process over time. This reveals the residual stress and helps engineers to identify potential failure points. Different AM processes can be compared – for example, different tool paths or speeds –to find the optimal parameters and to find trade-offs between, for example, strength and manufacturing time.
Real-time monitoring of metallurgical changes within the part can also help guide quality assurance. Understanding stresses within the part helps to target testing, and also gives engineers more confidence that the part will pass testing. This accelerates the prototyping phase and shortens the development cycle, saving time and money.
A digital thread solution for AM simulation
There are several distinct tasks in an AM propeller design cycle. These include 3D CAD design of the part itself, definition of the AM process, and simulation and analysis. These can all be linked together with a “digital thread” – an integrated workflow where data is shared between tasks and all stakeholders are working on a common digital model on a single source of truth.
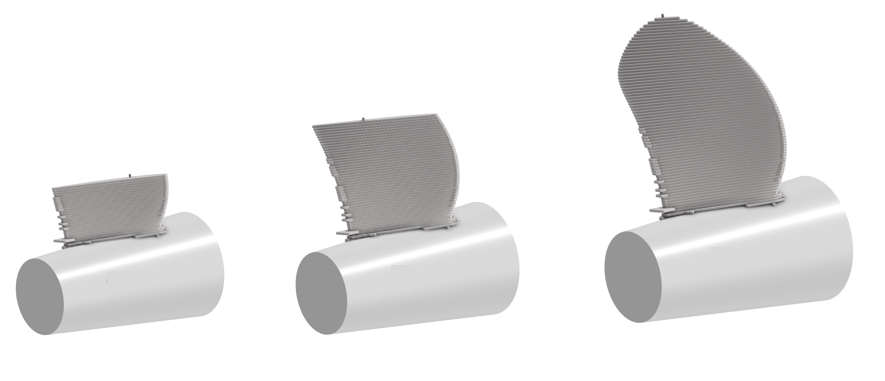
Dassault Systèmes offers a digital thread for additive manufacturing on the 3DEXPERIENCE platform. A propeller or other part is initially created in a CAD tool. This can be done directly in the design software on the 3DEXPERIENCE platform, or by importing a design in a format like STL, commonly used for AM. This is prepared for simulation with the CATIA Digitized Shape Preparation app.
The AM process is then defined using the DELMIA Material Deposition Fabrication app. This slices the geometry into layers and sets up the path for the laser. The SIMULIA Additive Manufacturing Scenario app then uses this to model the AM process. Transient heat transfer analysis calculates heat inside the part as the laser beam moves. This is then coupled to a mechanical simulation and drives the calculation of the static residual stress within the part.
Throughout this process, there is a direct, traceable connection between each step. The input for each stage is the output of the previous stage, and important context is preserved. Users can be confident that the final result reflects the original process, and if quality issues are identified, the problems can be traced back up the digital thread to their original source.
We presented a realistic, worked example of the digital thread for the simulation of marine propeller AM at UDT 2024. -See the conference paper for more details.
Conclusion
Additive manufacturing software has great potential in the marine and offshore industry, helping naval engineers to build propellers that are lightweight and easy to repair. Simulation helps designers and AM process engineers to analyze residual stress in an AM component during the design phase and to optimize the printing process to improve strength.
The Dassault Systèmes additive manufacturing apps on the 3DEXPERIENCE platform offer an end-to-end solution for AM process optimization. Design, process definition and simulation are linked in a digital thread, allowing traceability from the initial design files to the final product. With simulation, engineers can be confident that the design meets requirements, allowing accelerated testing to cut development time and costs and reduce the risk of test failure.
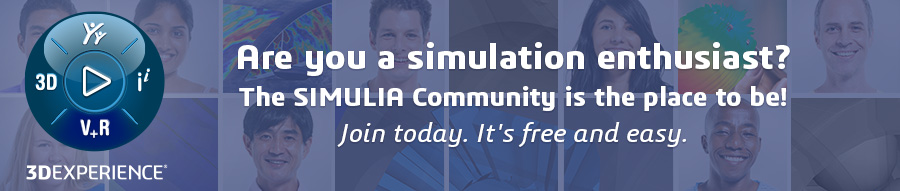
Interested in the latest in simulation? Looking for advice and best practices? Want to discuss simulation with fellow users and Dassault Systèmes experts? The SIMULIA Community is the place to find the latest resources for SIMULIA software and to collaborate with other users. The key that unlocks the door of innovative thinking and knowledge building, the SIMULIA Community provides you with the tools you need to expand your knowledge, whenever and wherever.