In the quest to design more efficient and sustainable aircraft, the turbofan engine provides an elegant solution. Using a fan to draw in extra air, which helps propel the aircraft, these engines provide thrust and boost fuel efficiency. While turbofan are generally quieter than turbojets, the engine is still a main contributor to community noise at takeoff and on landing.
“Noise matters because of its community impact,” said Sheryl Grace, associate professor of mechanical engineering at Boston University. “If you are going to take off or land at an airport, fuel consumption is a secondary concern for the people living nearby. What they care about is the noise that wakes them up at night and stops them from being able to talk outside for a given time. In addition, the internal noise created by turbofan engines impacts the experience of passengers and crew onboard.”
Turbofan noise is a complex challenge for aircraft developers and they are looking for the simulation tools they need to isolate and mitigate specific sources early in the design phase. Grace is working with Dassault Systèmes to create those tools with the help of SIMULIA PowerFLOW.
Turbofan Noise: A Multiphysics Challenge
Turbofans come in various styles, each bringing its own noise mitigation challenges. For instance, the low-bypass turbofans used in military jets pass most of the air through the core of the engine, so the primary noise source is from the flow out the jet nozzle. For high-bypass turbofans used by commercial airlines the situation is different.
“Turbofan engines advance the turbojet by enabling a lot of air to flow around the core, so the propulsion comes from the fan portion at the front of the engine,” Grace said. “The higher the bypass, the more the propulsion is coming from the fan. That means more of the noise is coming from the fan too.”
The noise is generated when the wake from the engine’s fan blades interacts with downstream stator vanes, redirecting airflow. This is known as “interaction noise” and it is the dominant noise source in commercial aircraft engines, especially during approach and landing. Its components include a tonal noise created by the mean flow difference in the wake behind each fan blade and broadband noise produced by turbulence in the wake. So far, this broadband noise has proven especially difficult to address. Solutions like resonators and duct shapes can be used to absorb specific tones, but they only work for narrow frequency bands (tonal noise). It’s much more difficult to absorb the large spectrum of sound that makes up broadband noise.
To model the fan noise problem, “you have to understand the fan wake, its interaction with and the shape of the vanes, how many vanes, how many rotors, how fast the fan is spinning,” Grace said. “There are many adjustments in these properties and in the duct that can be made to kill tones from the engine, but you can’t eliminate the turbulence in the fan wake and you cannot kill all of the noise it produces so there will always be broadband noise.”
Simulation Versus Physical Testing
Designers trying to mitigate broadband noise often rely on data from physical experiments to validate their predictions. This data typically includes flow measurements from at least two locations in the fan wake and then microphone measurements at specific locations in the field around the engine. It’s good data, but it’s limited.
Simulation can provide much more detailed insights into engine noise. SIMULIA PowerFLOW has emerged as an excellent tool for modeling the full fan stage using very large eddy simulations – a mathematical model for turbulence used in computational fluid dynamics. But while these simulations effectively capture turbulence and predict noise, they can be challenging to apply during the early design phase.
“PowerFLOW turbofan simulations have been used to explore various design questions, but they tend to be too intensive to use when assessing initial design,” Grace said. “Also, we’re dealing with different types of noise that are generated in various ways and if you’re modeling them with simulation software, you can get them all at once. But if you’re trying to just pull a little piece off and do a quick calculation, then you really have to drill down and ask, what exactly is causing that noise? And what could I pull out and model?”
Collaborating to Create Noise Simulation Design Tools
Grace wanted to see how PowerFLOW could be used to help create the tools turbofan designers need to minimize fan broadband interaction noise. Collaborating with Dassault Systèmes SIMULIA was a natural next step.
“Our collaboration happened organically,” Grace said. “Several years ago, at the Aeroacoustics conference, PowerFLOW started to come up in presentations on the airframe noise side. People were looking at how they could use simulation to predict airframe acoustics and PowerFLOW was gaining traction. Fast-forward a couple of years and suddenly, PowerFLOW had much higher Mach number capability. There was a benchmark challenge in the fan world and Damiano Casalino, [SIMULIA R&D, Fluids Science & Technology application manager at Dassault Systèmes] showed his results from a full, direct numerical simulation that he said took only about a week.”
Impressed by what she had seen, Grace was keen to get involved.
“I asked Damiano if I could analyze his computational data and see if the wakes were well modeled. Then we showed up at another meeting together and he told me NASA was going to let him run his simulation on a couple more fan cases that I had looked at previously. He agreed to send me the volume data and we worked together to complete the assessments.”
Eventually, that led to Grace’s collaboration in a SIMULIA Outcome-Based Engagement (OBE) – a software-as-a-service model in which the company that creates the software takes responsibility for its implementation and use. As well as cutting the time required to achieve a return on investment, Grace’s OBE with SIMULIA has provided a way to extend and enhance the data available from experiments to support design tool development.
Using Simulation to Grow Understanding
Collaborating with Dassault Systèmes meant that Grace could embark on a journey to develop the turbofan broadband noise prediction tools that engine designers need.
“What I really wanted was to see that the turbulence parameters out of PowerFLOW were going to be more understandable to me than when you just try to grab values from a turbulence model or play with a single-probe type of measurement from an experiment,” Grace said. “I wanted to get a better read on the length scale from the turbulence – which should be available from a full, large-eddy simulation. And I wanted that information everywhere – especially in the gap between the rotor and the stator vane. The other thing I wanted was to use all of the data in order to determine if the old empirical methods for how the wake should evolve still apply.”
Grace and her collaborators have made great strides in looking at wake evolution. And while the team continues to work through all of their questions around the turbulence length scale from the PowerFLOW data, Grace believes they are heading in the right direction.
Another of Grace’s goals for the collaboration was simply to figure out if she was missing anything in the low-order model, for example, regarding how the vane responds to pressure.
“We wanted to look at the vane response because the low order model is all about having something come in and hit this vane,” Grace said. “We model the vane with all our assumptions about how it responds to disturbances and I wanted to know whether that was close to the real answer. I wanted to see what the full vane response looked like.”
This turned out to be a more difficult challenge than anticipated – but PowerFLOW has enabled Grace to understand why that is.
“I tried to separate the acoustic response into the acoustic and hydrodynamic parts and it turns out that is just really hard to do,” Grace said. “You always have a boundary layer, you always have hydrodynamics, and pulling out that part, which is large, to get to the acoustic piece is really tough. But having the full vane data helped me to settle in my soul that this is just a tough problem. The reason I hadn’t been able to do it before was not because we only had experimental data at a few points. I now appreciate how difficult that whole separation process is and that’s a good outcome. I learned from it.”
Powering Ahead
Ultimately, the project has created a collaborative relationship that will continue to yield results.
“This project got me working with people at Dassault Systèmes and we continue to work together,” Grace said. “For instance, the next question is about boundary layer ingestion type engines. We continue to have conversations about whether there is something else we can work on together to improve the low-order modeling. Our work has given me an understanding of how to interact with the PowerFLOW output and what kind of information I can pull from a simulation and it’s connected me to the people who know how to run the simulations.”
New directions have also emerged for Grace’s work at Boston University.
“Collaborating with Dassault Systèmes has helped me to push my work in a few new directions and try to resolve unanswered questions,” Grace said. “It’s also brought more attention to my work, which has led to a grant from the Federal Aviation Administration that includes a new collaboration with Raytheon Technologies Research Center.”
Grace describes the effect as “like little stepping-stones.” As the project has opened more research and funding for her, that also means more funding for the graduate students who gain hands-on experience working with her.
“For me, this experience has been 100% positive,” Grace said. “I have found Dassault Systèmes to be extremely generous with their datasets. They are truly interested in understanding if there are ways to improve the PowerFLOW tool and how it can be used to help us in the acoustics field. They also like the research side from a fluid mechanics point of view and they often ask us to check something out. It’s very symbiotic and a collaboration I see continuing.”
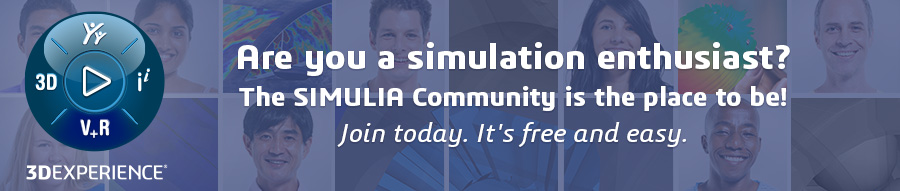
Interested in the latest in simulation? Looking for advice and best practices? Want to discuss simulation with fellow users and Dassault Systèmes experts? The SIMULIA Community is the place to find the latest resources for SIMULIA software and to collaborate with other users. The key that unlocks the door of innovative thinking and knowledge building, the SIMULIA Community provides you with the tools you need to expand your knowledge, whenever and wherever.