Welcome to the second podcast in this series focused on business challenges facing today’s Energy & Materials (E&M) industry.
The E&M industry faces many challenges today. From environmental concerns and increasing public scrutiny drive rising interest in alternative solutions that disrupt traditional business models. Complexity may arise from aging infrastructure and new, technically demanding assets. E&M organizations must diversify into new ventures, increase pace of innovation, improve organizational and infrastructure efficiencies and increase responsiveness by aligning product supply with changing priorities and demands of customers and society.
In this podcast, Senior Technical Director for Dassault Systèmes’ SIMULIA brand, Dale Berry discusses with Howie Markson how the role of simulation can reduce risks such as costs, safety and operation and improve the design and operation phases of capital projects.
Simulation is the ability to predict realistic behavior of how a plant or a system operates fully in the computer… You build a prototype, you go into a test lab and conduct a series of tests and you learn something about the behavior of that system. Simulation lets you do that fully in a computational environment. — Dale Berry
Sit back and enjoy the podcast with Dale Berry and Howie Markson
Digitally Transforming Capital Projects
Simulation Driven Plant Design And Operations
Be sure to listen into the other podcasts in this series and to learn more, please visit: https://ifwe.3ds.com/energy-materials
Subscribe and listen to the podcast series on the following channels:
Podcast Transcript
and with me is my colleague Dale Berry, senior technical director for Dassault Systèmes’ SIMULIA brand. Dale has over 30 years’ experience with simulation in the application of simulation to solve industry challenges. Welcome Dale.
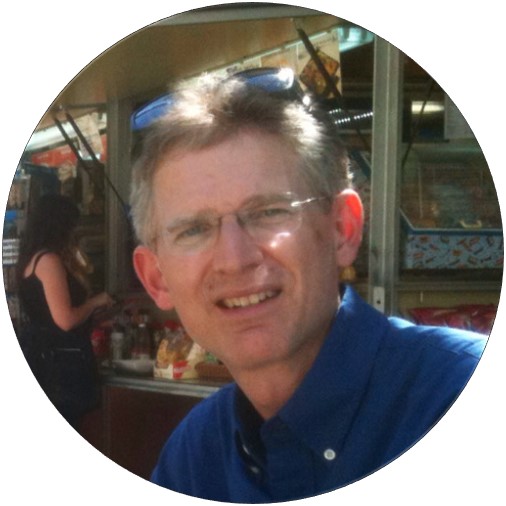
Dale: Hi, Howie. Thanks for having me.
Howie: All right, let’s get started. Dale, can you define what is simulation and how does simulation apply in the EPU industry?
Dale: Sure, and that’s a great first question, Howie. Simulation is the ability to predict realistic behavior of how a plant or a system operates fully in the computer. So I think your audience is very familiar with the benefits of testing. You build a prototype, you go into a test lab and conduct a series of tests and you learn something about the behavior of that system. Simulation lets you do that fully in a computational environment. It’s based on software that contains physics and response, stress, thermal, heat, loads. So really what you have with simulation is the ability 24/7 without an expensive test lab to build an operational behavioral model of your system, whether it’s a part or even a full plant and learn how it’s going to behave under various scenarios. I think a lot of organizations in the energy process and utilities industry already have a lot of activity going on in the simulation area, and it’s growing. Today, simulation is being used at the plant level and many of our customers are employing it, especially for things that cannot be otherwise tested. This is especially where the benefit of simulation and learning and knowledge that you get out of simulation can be valuable in this industry.
Howie: Okay, so you’re saying, so more people are using simulation sounds like it’s a good way to maybe reduce different kinds of risks. Maybe cost, safety. What are the main benefits of using simulation?
Dale: Right, so you hit on the key ones there that are owner operators and others in the industry are particularly interested in safety, reliability, uptime, quality. And simulation has immediate bearing on all of those topics. You know, for example, it’s hard or really impossible to test some of these complicated systems at the fringes of their operating environment, you know, during overload scenarios or accidents. And so simulation gives you the ability to go in and understand how your system is going to behave, not just when it’s operating normally, but when it’s operating off nominal, so to speak. The other thing that is important is from a reliability perspective, it’s important for these complicated and expensive plants to be up, operating as much as possible. And so simulation is very important then is used heavily to try to help keep the plants going, try to help understand when accidents might occur, you know, little things that occur in the course of ordinary business. And so those topics are really the economic drivers compared with the expense of testing. Simulation is a much more viable and less expensive alternative.
Howie: So it sounds like simulation in many ways is like predictive. You mentioned that, maybe to avoid some kind of accident in the future. Is it indeed used that way?
Dale: That’s right. You know, the history of the simulation industry was used for forensics and, you know, to determine why accidents occurred and what happened when they occurred. That’s the beginning of the simulation industry several decades ago. Since then computers and software become a lot more powerful and now these same methods that were used in an after effect way are being used during design being used during operation being used in advance to not only predict what may have happened, but to avoid those incidents in the first place.
Howie: So where is simulation typically used by owner operators?
Dale: Simulation can really be used throughout the entire plant life-cycle, from design all the way through the life cycle of a plant to decommissioning. I think a main application and benefits is in the design and operation stage. So, for example, simulation can be used to design a part of the entire system or a subsystem. For example, a containment structure, a turbine, a piping system, valves, and other important components in a complete plant. But it can also be used to study the processes that occur when those systems are in operation, both during normal operation, what’s the expected lifespan of the equipment during normal operation? It can also help to understand what happens when accidents occur. These plants are complicated and difficult plants to run and little accidents happen all the time. For example, a forklift may back into a column or back into a pipeline and dent it. So the question is, what does that mean? Do I have to shut down the plant completely and replace that piece of the dented pipeline, or can I go to the next maintenance cycle? Simulation is really very important in the fitness for service topic, where during operation it can help the operator understand what’s really happening in his plant as it’s operating.
Howie: Dale, we hear about Digital Twin in the manufacturing world. Does it apply in the Energy, Process and Utilities industry, and if so, can you explain what Digital Twin means in the context of simulation?
Dale: Sure. So the Digital Twin or, or really what you might call the Virtual Plant, is a replica of virtual replica, of all the physical assets as well as their processes. So what that means is we build a system model of the entire plant on the computer and we use that model to understand, to monitor, to help make decisions on the spot of how to operate the plant more effectively, how to make changes, how to go from one state to another. The concept of digital twin includes both the predictive capability of the simulation, but it also includes the idea of using real time data coming from the plant itself as input to the virtual model so that the operator can really see exactly what’s going on. When you have a computer model and you have the ability to understand a lot more of the data, a lot more of the process than you do just just from the physical measurements. So we have a new partnership with OSI soft, which is a leader in that part of the industry where data from their software will be able to be brought into the simulation model and we’ll close the distance between the virtual world and the real plant.
Howie: In one of your earlier answers, you talked about fitness for service and my understanding is there’s a standard API 579-1 everybody is required to comply with. How does simulation help with that compliance?
Dale: The term fitness for service really refers to an engineering evaluation and operational evaluation that has to occur when an incident in the plant occurs. As I mentioned, if a forklift backs into a pipeline and dents a pipeline, you have to decide what does that mean, how dangerous is it and what do I need to do about it? So there is a set of industry standards in the US, it’s API 579-1, and there are other standards worldwide. In Britain it’s BS 7910. So these standards describe the protocol and the approach that an owner operator has to take when an incident like that occurs. And simulation is really important here because it can help provide insight into what really the state of the plant is. So for example, you can build a simulation model of a dented pipe, put it through its paces, put its operating pressure and temperature on it, and then you can put an over pressure on it and see what that dent really means. Is it capable of handling the pressure? Is it more likely to fail or leak? And so the fitness for service topic is an important one for plants in many industries, especially in energy process and utilities because, you know, nobody wants to shut your plant down if you don’t have to. It’s just too expensive to do that. And so simulation can really provide the type of insight that is needed to help make the right decision at the time.
Howie: That makes a lot of sense. Thank you. Dale. The listeners and I now have a much better understanding the role stimulation can play in plant design and operations. Thanks everybody for listening to our podcast on simulation-driven plant design and operations. Remember, with simulation, you can reduce complexity and risk in your capital projects. To find out more how Dassault Systèmes is helping energy process and utilities companies digitally transform, go to https://www.3ds.com/industries/infrastructure-energy-materials. Please enjoy listening to the other podcasts in our series on Digitally Transforming Capital Projects in the Energy, Process and Utilities Industries.