Simulations for the assessment of HVAC noise play a key role in the HVAC development process. As opposed to tests which only tell how loud an HVAC is, simulation also helps to identify potential noise sources, provide visualization of these noise sources and even generate audio signals at passenger ears. Currently, our market leading best practices for setting up an HVAC simulation require expert knowledge and time. In addition, the whole HVAC unit needs to be simulated even if design changes are made far downstream. Our new release of best practices and simulation processes addresses these issues by adding advanced capabilities which reduce engineering time and simulation cost. This article presents an overview of these new methodologies.
Simplification of Geometry Preparation
Preparing a HVAC geometry is a time consuming process since the geometry is complex, determining the fluid volume is non-trivial and is prepared entirely manually by experts given the complexity involved in connecting parts.
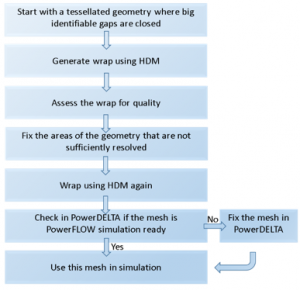
Acoustic simulations require the precise details of the geometry to be captured since a slight anomaly in the surface can generate unrealistic noise sources and levels. A semi-automated method has been developed that allows for the precise manual intervention but at the same time automates the non-trivial and time consuming parts of the process. Only certain targeted regions need to be corrected manually instead of the whole geometry. One can choose to work upon only flow critical parts. In a complicated geometry, it is difficult to determine the connections between parts. The method helps find out where the connections need to be made.
This method involves the use of Hex-Dominant Mesh (HDM) surface wrap which is used to generate wrap that creates a surface mesh. HDM is generates surface wrap with a single command. A generalized overview of the mesh generation process is shown in Figure 2.
This mesh generation methodology will enable a non-expert to generate a simulation ready mesh with ease without undergoing the hassle of preparing the entire geometry manually. Also, there are sometimes changes in the geometry from the client’s end or from the internal design team. That means if the geometry has already been worked upon, then the person has to start over again. This methodology allows for such changes, still reducing geometry preparation time and also finishing the sometimes repetitive, mundane process with ease.
This method is in the evaluation phase. Initial tests are completed and methodology is currently under test on realistic customer cases. This approach makes the process streamlined, less prone to human errors and also helps reduce the simulation set up time.
Simplification of Simulation Process
Once the geometry is ready to be simulated, the next step is to prepare the simulation. The simulation process involves setting up the case, submitting of jobs on queuing systems and post-processing the results.
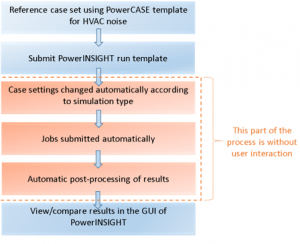
The set up for acoustic simulations is complex and time consuming, and thus prone to engineering errors. Improvements to the case template were implemented to minimize engineering effort during the preparation of the reference case. A full case can be ready within a quarter of an hour from prepared geometry, with all simulation specific settings fully automated. A process template is generated in the automation tool PowerINSIGHT for these simulations, where no user interaction is required beyond the template submission through a graphical user interface (GUI). With the use of this template, the saving in overall turnaround time, including engineering and computation time, is approximately 60 hours. A generalized overview of the process using the PowerINSIGHT template is shown in Figure 3.
Post processing is performed automatically and results are generated as PowerINSIGHT contents. The results can be conveniently browsed in PowerINSIGHT for each simulation and a comparison of results from different simulations can be performed with ease as shown in Figure 4. This also allows for the simulations to be submitted overnight and during weekends automatically, which eliminates the time spent in waiting for the next simulation to be submitted manually.
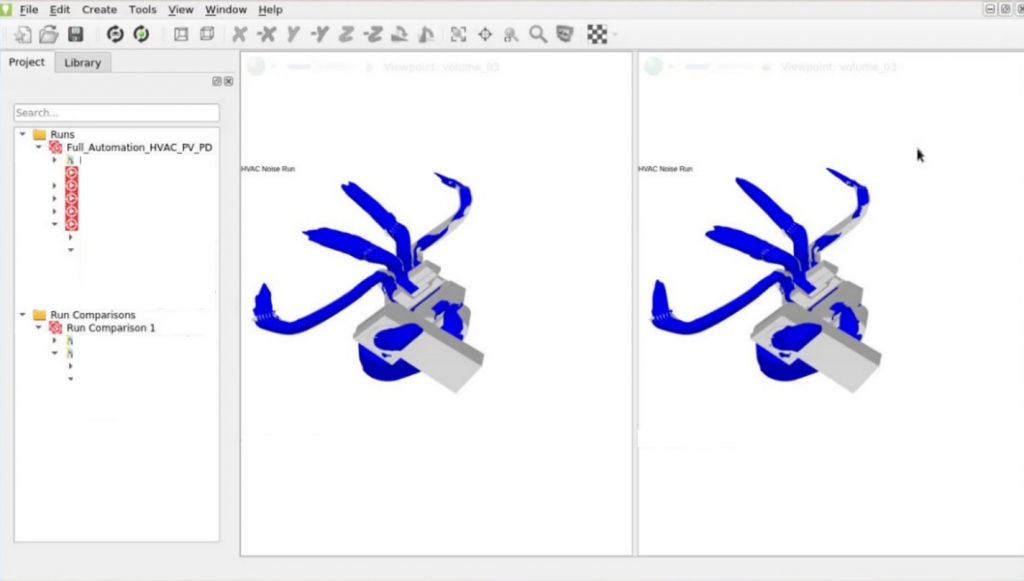
The template is currently being deployed by customers on their High Performance Clusters for testing in their HVAC industrial development process.
Transient Boundary Seeding
Transient Boundary Seeding (TBS) is currently being used for external aerodynamics and acoustics to bring down simulation cost on complex geometries. For example, in the case of HVAC, instead of simulating entire fluid volume that has the ducts, registers, mixing unit and blower, only part of the fluid volume that has for instance only one duct and register is simulated. By saving specific data upstream at a defined surface in a previous run, we can cut down on the simulation cost for variant runs. Because now, we are reducing the size of the simulation volume of fluids.
In a similar way, this methodology is used on internal flow. Especially for HVAC simulations, this can lead to dramatically decreased turnaround costs compared to a full system. The immediate advantage versus imposing mass flow on the boundary is the inclusion of turbulent fluctuations and pressure boundary conditions. Thus, noise generated upstream is seeded into the run, bringing noise levels closer to what we would expect from a standard setup. This can lead to a difference of up to 20dB measurable at the microphone locations for an HVAC system in a test setup. TBS also provides a cheaper way to include the noise contribution of an upstream blower which would otherwise needed to be resolved. In extreme cases, this can reduce simulation costs up to a factor of 10.
Depending on the needs of the customer, several setups from singular register simulation to setups where all registers/ducts are considered are possible.
The acoustic field of the simulation outside of the ducts is well comparable, as are probes close to the respective outlets. Keep in mind, that in order to capture the full spectrum on a far field probe or at a typical driver ear position on a car HVAC system, all relevant outlets and thus ducts need to have a seeding input and need to be simulated. An example of comparison of acoustic dB maps between whole and truncated unit is shown in Figure 5.
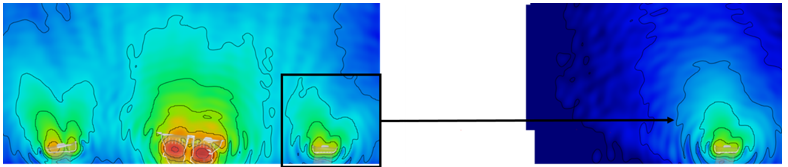
Comparing the noise levels inside the ducts to study resonant behavior gets a little bit more challenging as a slight absorption needs to be applied to the walls inside of the system to dampen acoustic waves reflected at the seeding boundary. This aspect is currently evaluated and will be added to the Best Practices document.
With these advanced methodologies, both experts and non-experts can perform simulations with ease, reduce manual time spent on setting up the simulation and spend time on design and analysis for their products.
Want to connect with other HVAC experts and access HVAC resources? Visit the HVAC overview page in our SIMULIA Community to start exploring.
SIMULIA offers an advanced simulation product portfolio, including Abaqus, Isight, fe-safe, Tosca, Simpoe-Mold, SIMPACK, CST Studio Suite, XFlow, PowerFLOW and more. The SIMULIA Community is the place to find the latest resources for SIMULIA software and to collaborate with other users. The key that unlocks the door of innovative thinking and knowledge building, the SIMULIA Community provides you with the tools you need to expand your knowledge, whenever and wherever.