This is Part 3 of our 12-part blog series, series based on the LNS Research eBook, “Forging the Digital Twin in Discrete Manufacturing: A Vision for Unity In the Virtual and Real Worlds“.
Previously in Part 2 we explored the today’s possibilities being driven by digital twin technology. Now let’s look at who is using Digital Twins and across which industries, as polled by LNS Research.
Who’s Using Digital Twin
LNS pre-screened all potential respondents and weeded out many hundreds that do not have a digital twin initiative, or do not operate in an industry congruent with the focus of LNS’s work. Of those with no digital twin initiative or plans, we did ask one key question, “Why not?”
The results are reminiscent of IIoT awareness three to four years ago; almost half didn’t know what a digital twin is. As the Digital Twin gains traction and importance, awareness will grow. For today, the software vendor and market research communities have a substantial education task in front of them.
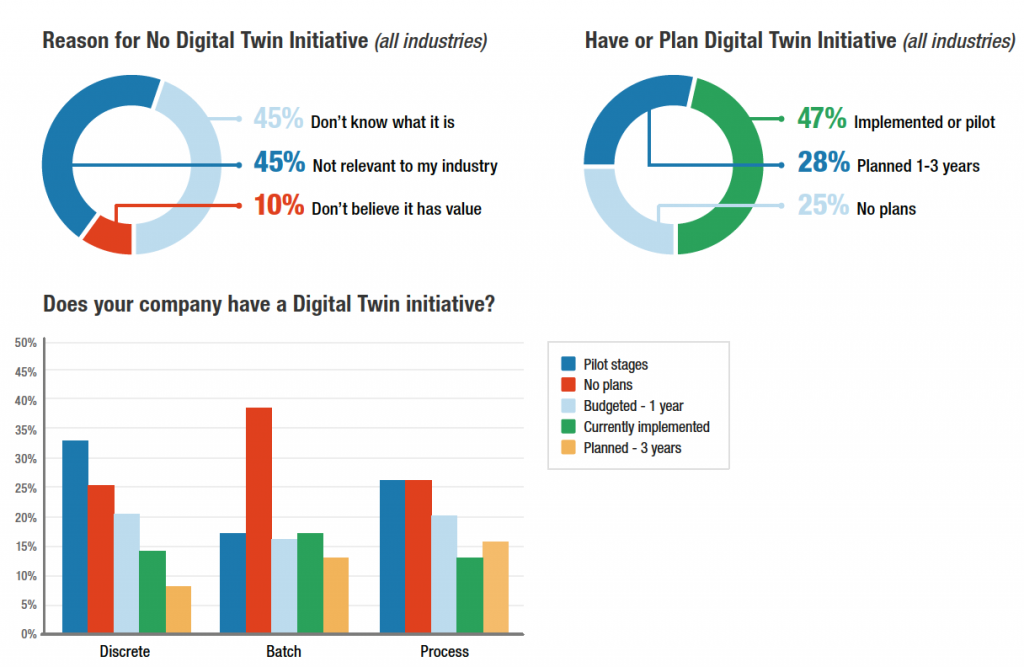
The appetite for the Digital Twin varies by industry segment, and there is a correlation with use of product lifecycle management (PLM) and the IIoT. As we expected, companies that use PLM and the IIoT show considerably more enthusiasm for digital twin technologies. Overall about 40% of companies either have digital twin technology or are in pilot stages, but when we look at just companies that actively use PLM or IIoT platforms, that number rises to an impressive 60%. However, things aren’t as rosy as the numbers suggest:
- Among discrete manufacturers, one-third have no plans or plan to wait up to three years.
- While respondent’s mean number of production sites is about 25, with very few exceptions, companies have deployed or piloted digital twin technology in only one or two sites.
- Where implemented, only a median of ten people actually use the Digital Twin software.
- Only 23% of companies have more than $1 million in the budget for the Digital Twin initiative.
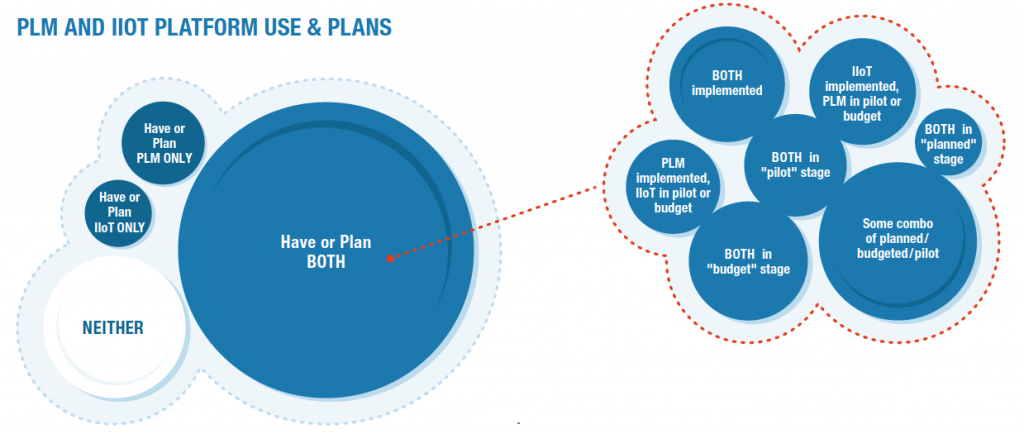
EXALEAD Commentary:
Before emerging IoT technologies, the digital twin concept was limited to the manufacturing process industry, focusing mainly on equipment monitoring.
The recent need for digital twins sprung from organizational changes that have happened in the industry. Business Matter Experts are no longer available in each and every production plant. Mobility and remote connectivity have made it possible for people to work remotely from the field. Being able to navigate virtually in an accurate (and up-to-date) 3D representation from any remote location while accessing field Information became a necessity.
During the last two decades companies were focusing on the deployment of ERP and supply chain. Now that every company has the visibility on their back-office and are able to promise, they need to secure their ability to deliver. Thanks to the digital twin, companies can reconcile field information with their supply chain.
The digital twin is also becoming a collaboration space between the end user and supplier. By providing access to the virtual products, the customer’s voice is counted and can influence the design. The demand for customization will increase, leading to production orders of one, which requires high flexibility.
The key to this transformation is to first break down the data silos between IT (Information Technology) and OT (Operational Technology): supply chain management system (SCM), enterprise resource planning (ERP), various manufacturing operations management systems (MOM), Enterprise Asset Management systems (EAM) and customer relationship management systems (CRM).
If today these different systems are interoperating to manage the overall production process, it remains very difficult to reconcile quality issues or events that happened at any stage of the process with the quality of the final product.
EXALEAD on the 3DEXPERIENCE platform is leveraging the content of multiple IT and OT sources by aggregating, contextualizing data and revealing information in the context of the digital twin. Acting as an abstraction layer between the Users and the different information systems, EXALEAD is providing a unified and single access to the information.
This need for customization and quick-to-market delivery not only leads to happier, more satisfied customers but also reduces risk and increases profitability for manufacturers by enabling them to nimbly innovate at the speed of market demand.
By aggregating and analyzing IT and OT data together in the context of the digital twin, the manufacturer can engage close-quality feedback loops to improve continuously its operations and respond more agilely to customer needs.
In the next blog installment, we will explore future growth expectations for the use of digital twins in manufacturing.
Part 1: What is a 3DEXPERIENCE Twin?
Part 2: Digital Twins and Manufacturing: Today’s Possibilities
Part 3: Who is Using Digital Twin Technology?
Part 4: Growth Expectations for Digital Twins in Manufacturing
Part 5: Digital Twin Use Cases in Manufacturing
Part 6: Exploring Digital Twin Opportunities in Manufacturing
Part 7: Simulating Product Use with Digital Twins in Manufacturing
Part 8: Simulating the Manufacturing Process with Digital Twins
Part 9: Software in Digital Twin
Part 10: Real Data Versus Virtual Data
Part 11: Digital Twin: Pragmatic Considerations
Part 12: Recommendations for Getting Started with Digital Twin
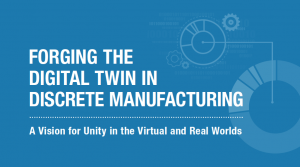
Read our White Paper on Forging the Digital Twin in Discrete Manufacturing
Join our User Communities to stay on top of the latest industry news, ask questions and collaborate with peers:
- EXALEAD Sourcing & Standardization Intelligence User Community
- 3DEXPERIENCE Marketplace | PartSupply User Community
- NETVIBES Public Community
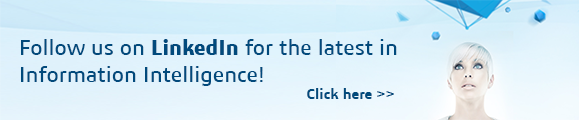
Learn more about EXALEAD on the 3DEXPERIENCE platform.