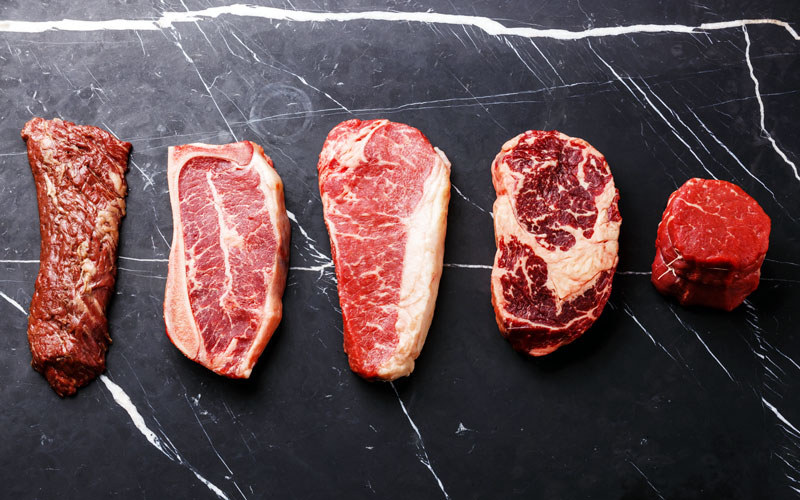
Worldwide meat production has doubled over the last three decades and increased 20% in just the last 10 years. As meat consumption rises, the pressure is on meat producers to fulfill demand. To accomplish that, they need to be efficient at every step of their supply chain. The meat supply chain is long and complex. It starts from farm, slaughterhouse, processing, packaging and logistics, right up to retail and catering.
Meat disassembly is a key part of the operations, and it’s where opportunities for profit can be found. But amidst the many challenges and constraints, maximizing the potential at the disassembly line becomes difficult.
Supply uncertainty
Meat disassembly is complicated because, among other reasons, no two animals are alike. Each differs in size, weight and quality. In essence, you can’t tell for sure what you’re going to get. What’s certain is that there will be inconsistencies and deviations from your predicted volumes.
Optimizing the use of products to match demand in the meat sector is highly complex. Your planners must be able to identify and address the gap between forecasted and actual volumes. Given the capacity constraints of individual plants, they have to match the demand for individual cuts with supply.
Decisions, decisions
Adding to this is the inherent complexity of the raw material. A carcass is a composition of several cuts, each with its own demand curve and a set number of disassembly options. The challenge lies in determining what to make from the fixed and mixed supply, in a way that can have the highest valorization and meet the demand for all individual cuts. This, however, results in a large surplus of less popular cuts. The only way to reduce wastage is to have both end-to-end visibility and a consistent planning approach.
As the exact specification of the animal can only be determined after the slaughtering, planners need to be flexible once reality kicks in. With the right planning tool in place, the optimal valorization can be recalculated and a new plan created just in time based on the most up-to-date information.
One of DELMIA Quintiq’s customers that understand this very well is JBS USA. The company relied on DELMIA Quintiq to improve its disassembly process. As a result, the company was able to maximize the value of dozens of individual products for different customers. Read the JBS USA story here.
The need for efficient disassembly plans
In order to boost performance and stay ahead of the competition, meat producers must place a stronger emphasis on better planning of operations, and this includes their disassembly process. But first, the obstacles need to be overcome.
Supply uncertainty and numerous cutting options are just two of the major disassembly challenges plaguing meat producers. There are more, including volatile demand and meat freshness. How can all of these challenges be overcome effectively? We at DELMIA Quintiq say that it’s about managing the complexities of large-volume operations, achieving sufficient visibility, having decision support and relying on optimization technology. We share the full details here.