Addressing transformation and sustainability initiatives
Globally, manufacturers are experiencing growing pressure to reduce carbon emissions in their production processes. The metals manufacturing industry is characterized by disruptions and volatility, making it paramount that manufacturers find innovative solutions to face the challenges ahead. These challenges–wrought by the global shift towards decarbonization and the adoption of circular economies–generate a need for transformation and sustainability initiatives.
Steel production stands out as a prominent contributor to global industrial emissions. According to the World Steel Association, a staggering 1,860 million tons of steel were manufactured in 2020, constituting 7% to 9% of global CO2 emissions. Clearly, metals manufacturers face a tremendous challenge in transitioning away from traditional production methods to green hydrogen, green steel, and eco-friendly technologies.
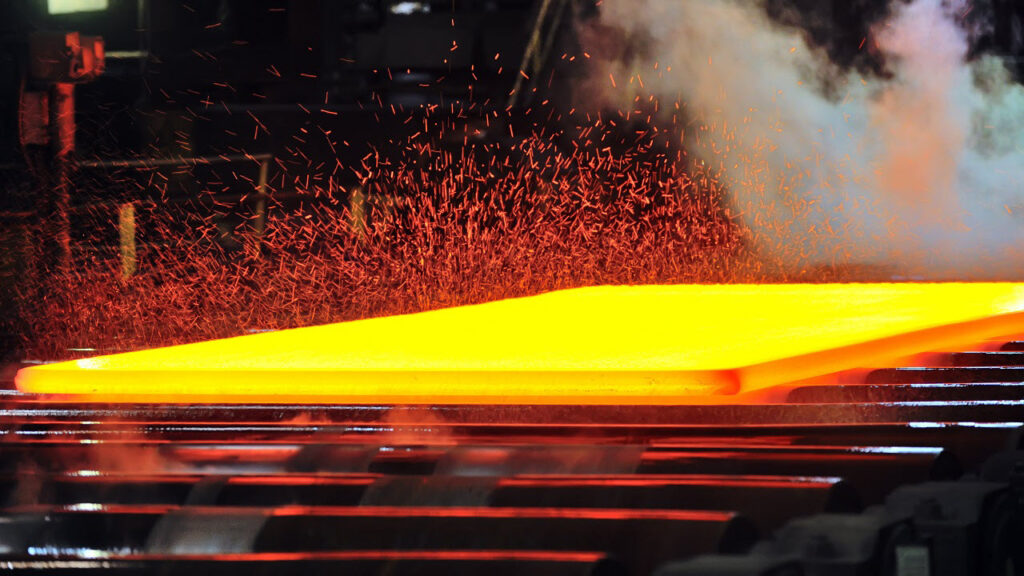
The path forward is clear: metals manufacturers must engender greater resilience and future readiness by optimizing resource usage, minimizing waste, and embracing renewable energy sources. However, the difficulty lies in simultaneously ensuring profitable operations.
Obstacles to supply chain optimization in metals industry
Volatility remains a constant thorn in the side of metals manufacturers. For example, ongoing conflicts caused price spikes in 2022, with the trend of unprecedented volatility throughout the value chain expected to continue across 2023.
Aside from challenges that arise externally, metals manufacturers also encounter internal obstacles that hinder their supply chains from achieving end-to-end excellence.
Here are three significant internal challenges faced by metals manufacturers:
Lack of Integration: Siloed planning is still commonplace throughout the metals manufacturing industry. Different departments often operate independently, making it challenging to synchronize operations and optimize the supply chain. Each unit can only make plans based on its own set of data and goals, leading to fragmented operations, sub-optimal resource allocation, and poorer performance.
Resource Planning on Outdated Platforms: Many metals manufacturers still rely on spreadsheets and legacy tools for resource planning, which hinders data accuracy and integrity. At the same time, manually updating these systems can often lead to additional errors and discrepancies. Furthermore, these tools often lack the capability to provide real-time visibility into resource availability and demand, making it difficult to make agile decisions in rapidly changing environments.
Local Decision-Making: Decisions about inventory management, machine usage, and workforce allocation are often made at the local level. This decentralized approach results in sub-optimal choices that often fail to align with broader supply chain planning and optimization goals. Additionally, without a holistic view of the entire supply chain, local decision-makers are unable to allocate resources appropriately, potentially leading to wasted materials, increased energy consumption, and higher operating costs.
With these problems in mind, metals manufacturers can clearly see the need for integrated, data-driven, and collaborative supply chain and operations management. What does a resilient, more technologically advanced future of metals manufacturing and production look like?
Solutions to optimize operations in your metals plant
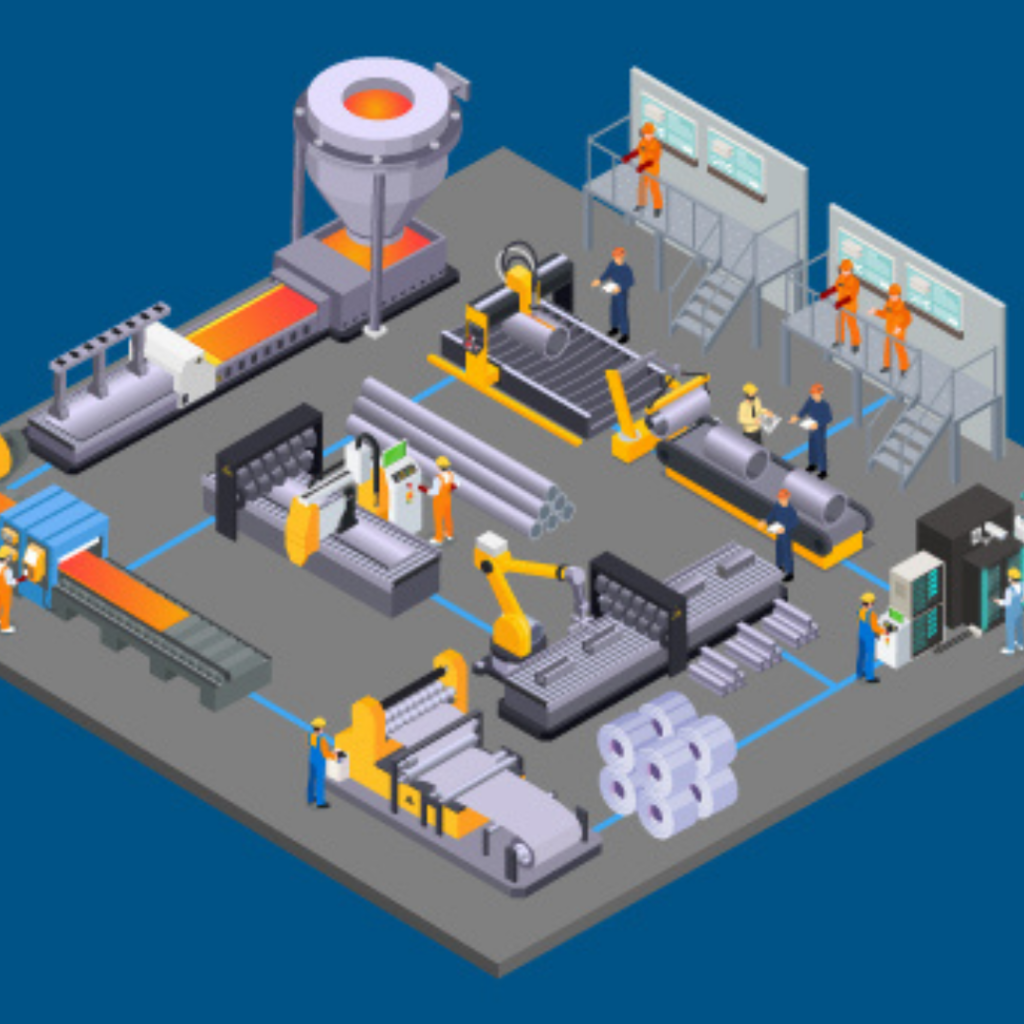
The metals factory of the future should incorporate innovative solutions in the pursuit of sustainability and profitability, without compromising on either. These solutions should also minimize the impact of volatility and disruptions on operations, allowing the manufacturing process to proceed smoothly regardless of internal and external challenges.
Sales and Operations Planning software: A good S&OP solution bridges the gap between strategy and execution through improved collaboration, real-time insights, and seamless decision-making. Besides aligning plans with market demand and strategic objectives, S&OP can also enable global supply chain visibility, automated data collection, improved forecast accuracy, and tracking of CO2 emissions for sustainability.
With mature S&OP capabilities, metals companies can also integrate financial planning with operational planning. This allows them to link high-level strategic plans to day-to-day operations to meet targets, as well as maximize operational efficiency. Furthermore, companies can gather financial inputs on current plans and manage multiple currencies, easily switch between currencies, simulate rate changes over time, and analyze financial impact.
Master Production Scheduling software: An MPS solution coordinates the production cycle to balance goals, cut costs, and boost customer satisfaction. By developing optimal production plans, this solution seamlessly integrates sales, production, procurement, and transportation, allowing for reduced inventory and heightened efficiency. Gain visibility across the supply chain—from upstream melt-cast work orders to downstream finishing line work orders as well as material flow synchronization—with integrated short-term production planning software and a single source of truth that connects sales, production, procurement, and transportation through supply chain planning and optimization software.
Detailed Scheduling: DELMIA provides an advanced system that optimizes programs and sequences while considering the unique rules and constraints of each business. This enables better planning of material flow, order combination, and batch creation, resulting in improved delivery performance and resource utilization.
– Material flow: DELMIA can model the flow of operations from steelmaking to hot or cold rolling and finishing, simultaneously taking into account different lead and processing times as well as setup times between operations.
– Rolling programs: DELMIA increases resource utilization by defining programs and scheduling operation groups on resources where operations are processed individually, as well as being able to re-sequence entire groups of operations at once.
– Sequencing: The solution improves utilization, minimizes production costs, and reduces quality issues by sequencing tasks and establishing feasible schedules.
– Optimization: DELMIA automates the creation and optimization of heat sequences in furnaces and melt-cast shop processes with world-class KPI-based optimization.
– Sustainability: The solution improves efficiency while also promoting sustainability, reducing energy consumption, and minimizing waste and scrap production. This brings you one step closer to the creation of the metals factory of the future.
– Decision support: DELMIA offers a configurable user interface that allows for easy manual changes and propagates those changes throughout the entire production routing. Real-time key performance indicators (KPIs) and “what-if” scenario creation and comparison further enhance decision-making capabilities.
Manufacturing Operations Management: DELMIA Manufacturing Operations Management (MOM) software provides a unified platform that seamlessly integrates production, quality, logistics, maintenance, and other business operations.
– Production: Lean Six Sigma practices are enforced for error minimization and delay reduction, enhancing production quality and output.
– Quality Control: A traceable manufacturing quality control software is featured in DELMIA MOM, ensuring value chain visibility and compliance. Certifications and document generation, configurable analyses, and real-time process control checks are facilitated.
– Maintenance: Integration of maintenance schedules with production is made possible by DELMIA MOM, creating a seamless workflow.
– Warehouse & Logistics: The solution allows for inventory and logistics management, OTIF delivery improvement, cost reductions, and detailed inventory movement tracking in real-time. It also supports the transition to pull-based or hybrid production models.
– Traceability and Genealogy: Complete genealogy, traceability, and sampling for products and processes are provided, aiding in defect identification and standards compliance.
– Labor: Compliance with labor regulations is ensured, while workers are matched with suitable jobs. Meanwhile, DELMIA MOM enables complex configurations of pay, work, and union rules, as well as providing performance insights through Key Performance Indicators (KPIs).
Virtual Modeling: The Virtual Twin Experience lets manufacturers visualize and optimize new products, facilities, and production processes. This executable virtual representation of the supply chain enables organizations to design, plan, and optimize virtually before implementing it in the real world, leading to waste reduction and increased efficiency. In effect, in helps you visualize and model your own metals factory of the future.
Powered by the 3DEXPERIENCE platform, a virtual twin of the manufacturing and supply chain allows manufacturers to capture all complexities within the metals production network. Besides creating realistic, feasible plans, this also provides opportunities to improve processes for better service and an improved delivery experience, alongside driving sustainable manufacturing operations.
– Facility planning: The tool optimizes physical space and assembly lines by validating workstation and tool usage, minimizing risks to health, personal safety, and environmental performance. Collaboration and sharing of 3D layouts with suppliers and partners in the value chain also prevent costly layout redesigns.
– Recipe lifecycle management: This will enable metal manufacturers to manage the deployment, adoption and execution of production recipes in process manufacturing. It allows storing the recipes and enables recipe modification for manufacturing processes.
– 360 Degree Manufacturing Control Tower software: Provides the ability to take decisions and monitor the metal manufacturing operations through contextualizing data from Information Technology (IT) and Operations Technology (OT) sources. It enables shop floor production supervisors and managers to gain visibility and helps in anticipating disruptions through real-time data in a live dashboard.
Taking the next step towards the metals factory of the future
As the sustainability imperative becomes crucial, metals producers need to embrace new technologies and adapt to rapidly-evolving global marketplace demands. However, integration of these new technologies should include more than just production processes. It should encompass suppliers and customers to streamline all aspects of the value chain and operations.
Learn more in our comprehensive virtual tour of the Metals Factory of the Future.