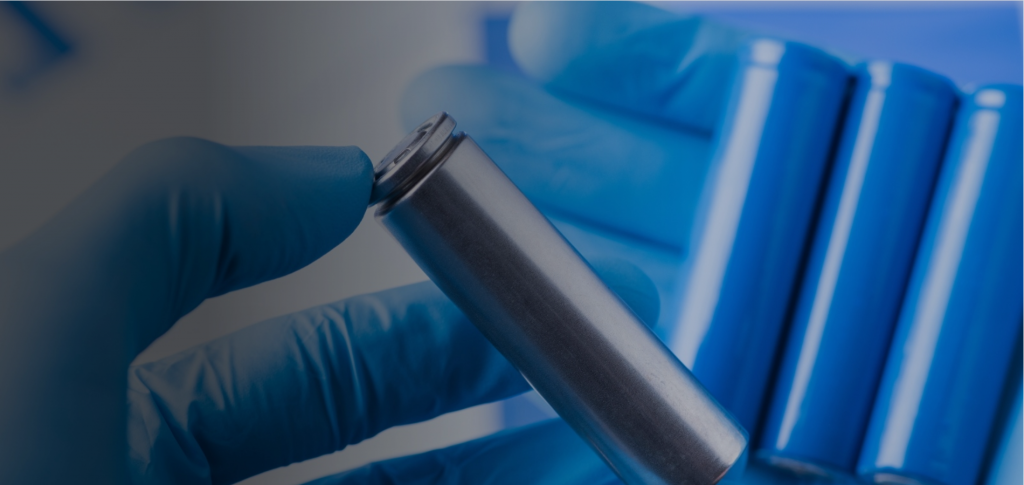
One of the most intriguing high tech industry segments today is battery cell technology. It is an amazing mix of rapidly evolving supply chains, constrained resources, product innovation and global and startup companies competing for market-share.
Battery Cell Manufacturing In a Nutshell
Battery cell manufacturing refers to the process of producing individual battery cells. A battery cell is a self-contained electrochemical device that can store and provide electrical energy through chemical reactions. These cells are then assembled into battery packs to meet the specific power and energy requirements for various applications, such as electric vehicles, consumer electronics, and renewable energy storage.
The battery cell manufacturing process typically involves several key steps:
- Materials Preparation:
- Raw materials such as metals (like lithium, cobalt, nickel), electrolytes, and separator materials are sourced and prepared for use in the manufacturing process.
- Electrode Production:
- Electrodes are the positive and negative terminals of the battery cell. They are typically made by coating a thin layer of active material (such as lithium cobalt oxide for the positive electrode and graphite for the negative electrode) onto metal foils.
- Separator Coating:
- A separator material is coated or impregnated with electrolyte to create a barrier between the positive and negative electrodes. The separator prevents a short circuit while allowing the flow of ions between the electrodes.
- Cell Assembly:
- The positive and negative electrodes, along with the separator, are assembled into a cell. This assembly is often referred to as the “jellyroll” structure, where the components are tightly wound or folded to maximize energy density.
- Electrolyte Filling:
- The cell is filled with electrolyte, a conductive solution that facilitates the movement of ions between the electrodes during the charging and discharging cycles.
- Sealing:
- The filled cell is sealed to prevent leakage and to maintain a controlled environment within the cell.
- Formation:
- The newly assembled cells undergo a formation process where they are charged and discharged several times to stabilize their performance and capacity.
- Testing and Quality Control:
- Each cell undergoes rigorous testing to ensure it meets specified performance and safety standards. This includes checks for capacity, voltage, and other critical parameters.
- Packing:
- After passing manufacturing quality control software, the cells are grouped together and packaged into battery packs. These packs can vary in size and configuration depending on the intended application.
Advancements in battery cell manufacturing technologies are crucial for improving the performance, energy density, and cost-effectiveness of batteries, which, in turn, contributes to the development and adoption of electric vehicles, renewable energy storage solutions, and portable electronic devices.
It is also a classic example of the connection between different industries (such as automotive) where strategies range from collaboration to acquisition as OEMs attempt to plan their own roadmap to capture consumer demand and meet regulatory requirements.
Taken all together, this perfect storm of events is having a dramatic impact on manufacturers as they juggle the challenges of ramping up large scale production while coping with ever changing technology and creating sustainable operations. Given the complexity, manufacturing systems of the past do not provide an effective means to support the production requirements demanded. In fact, what is required is elements of capability from both the real and digital world through digital twin solutions.
Digitizing Battery Cell Production
Virtual twin experience capabilities have been used extensively in many industries as it provides the unique ability to simulate all aspects of manufacturing. From plant and line layout to process and manufacturing engineering, manufacturers can mitigate the risk of real world consequences by experimenting with digital models of products, processes and resources. It also incorporates a closed loop process that connects internal silos of design, engineering and production while collecting data from the real world to drive continuous improvement.
Without technology such as the digital twin, battery cell manufacturing can be a challenging proposition for both startups and seasoned organizations. Achieving operational excellence can provide significant benefits through:
- Reduced costs from more efficient operations
- Reducing time to market by eliminating internal silos
- Continuous improvement through analysis and 3D visualization
It is clear that there is no definitive playbook for this new and rapidly involving industry, but there are plenty of questions. We hope to have a valuable discussion around some of these questions and provide some answers that you can take away and start to apply to your own journey. Whether you are directly involved in battery cell manufacturing or representing an OEM integrating batteries into your own product, we are sure you will benefit from taking part.