Automated Guided Vehicles (AGVs) have been around in factories as early as the 1950s, where a “driverless vehicle” manufactured by Barrett Electronics, in Illinois, could follow the electromagnetic field of a wire located in the factory ceiling or, later on, embedded in the floor[1].
However, since the acquisition of AGV manufacturer Kiva Systems by Amazon in 2012 and Amazon’s decision to stop sales and use Kiva robots exclusively to improve their logistics, there has been a surge of interest for industrial Automated Guided Vehicles. According to a 2017 article from a Loup Ventures analyst, the AGV market could be by 2025 “one of the fastest growing sub-markets within the entire robotics space”, with a Compound Annual Growth Rate of 35% for the 2015-2025 decade.
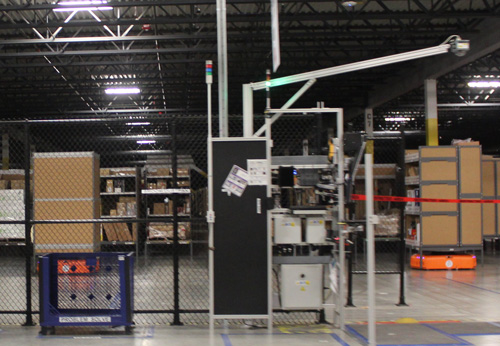
In this article, we will see what drives companies to use AGVs in their facilities, what needs to be considered when choosing an AGV System (involving a fleet of Automated Guided Vehicles) and finally what are the impacts in terms of IT systems.
Why Use AGVs?
Today, industrial AGVs are mainly used for material handling within a warehouse or factory or sometimes outdoors. Some typical usages include:
- Transporting received materials to storage areas
- Supporting kitting operations and just-in-time deliveries
- Delivering work-in-progress parts to manufacturing production and management software lines
- Transporting finished goods to shipping areas
So transportation is the key function. In spite of recent advances in computer vision, object recognition and robot grasping techniques, humans are still usually needed to pick and place individual parts, while pallets are typically transported by AGVs.
An AGV System may bring different benefits listed below.
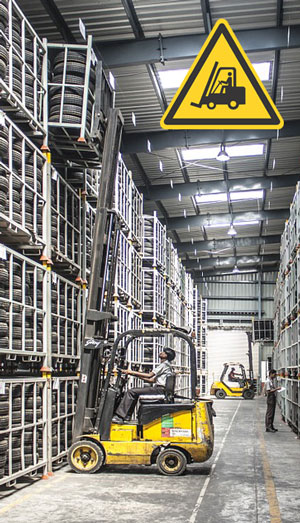
Safety
According to a 2016 from the Occupational Health and Safety Administration (OSHA), forklift accidents result in roughly 85 fatalities and 34,900 serious injuries every year in the United States. When truck manufacturer Scania considered using AGVs for material handling in their production areas, a key objective was to help achieve a forklift-free production, since forklifts were regarded as “one of the most dangerous work equipment at Scania”[2].
Forklift AGVs are the most common type of AGVs and look pretty much like regular forklifts. Some models also have space for humans, allowing to steer the AGV manually when needed. Like all AGVs, they include sensors that ensure that the vehicle slows down or stops when encountering a human or an obstacle. They operate at a controlled, limited speed, accelerate smoothly and have a predictable behavior, thereby limiting accidents[3].
Damage Reduction
Forklift drivers may be distracted, tired or simply have a bad day. As a result, they may damage products or hit equipment and structures. AGVs of course are more reliable and can work 24 hours a day. Following the introduction of AGVs, Valio, a Finnish producer of dairy products, has managed to reduce damage to vehicles, stock and site by 90% in one of its cheese factories.
Cost Reduction and Better Operations
In a Lean Manufacturing software perspective, AGVs reduce transportation time, which is non-value added time in manufacturing operations.
If AGVs replace fixed automation systems such as conveyors, they can reduce costs thanks to quicker implementation, staged investment and additional flexibility.
If Automated Guided Vehicles replace or relocate employees, they can allow to reduce labor costs and increase productivity. After automating transport routes using a mix of conveyors and AGVs, AMAG Automobil, a car importer and dealer, has optimized its production throughput time by 20 to 30%.
An AGV System also leads to a more regular flow of material, with clean shop floors making room for Automated Guided Vehicle navigation paths. It can also bring improved inventory accuracy if properly connected to a Warehouse Management System Software.
Things to Consider When Planning the Introduction of an AGV System
Here are a few things you need to keep in mind:
What to automate?
First, companies need to identify a candidate process to automate, the material flow paths within the process and the load to be transported automatically. A first estimation of employee relocation impacts, rationalization gains, quality improvements and improved work conditions can help decide which processes to target at this point.
What kind of Automated Guided Vehicle?
The choice of the process and of the transported load will largely define the kind of AGV to select. There is no standard nomenclature for AGV types, but the most commonly cited ones are the following:
- Forklift AGVs, to move and lift pallets both at floor level and on stands
- Unit load AGVs, to retrieve and delivery pallets, boxes or containers, equipped with decks for load transportation and load transfer
- Towing AGVs, to move trailers or trains of trailers within the factory
- Assembly AGVs, to move work-in-progress parts to the assembly line, usually at a slow pace
- Light load AGVs, to transport small parts or baskets, for example in hospitals
- Towing AGVs, to move trailers or trains of trailers within the factory
Which Navigation Technology?
AGVs need to continuously assess their position, which can be done in different ways. The choice of navigation technology not only depends on what AGV suppliers may propose, but also on the environment in which the AGVs will operate, and on the desired flexibility for changing AGV paths.
The laser guidance navigation technology is one of the most popular navigation methods today. A rotating laser on top of the AGV emits a beam that is reflected by marks positioned on walls. The exact vehicle position is computed through triangulation. This technology is flexible and highly accurate but is sensitive to dirt and sunlight.
Other technologies include:
- Wire guidance: a current-carrying wire generates a magnetic field (low cost, reliable and robust, but not flexible and sensitive to metal in the ground)
- Magnetic tape or grid guidance: a magnetic tape or magnetic spots are placed on the floor (low cost, flexible, but sensitive to dirt, sunlight, damages, and metal on the floor)
- Optical guidance: a painted or taped line on the floor guides the AGV (low cost, flexible, but sensitive to dirt, sunlight and damage to the line)
- Natural navigation: using a registered map of the facility and a camera or laser, the AGV identifies elements in the facility, such as pillars or walls, and computes its position according to them (highly flexible, does not require a specific infrastructure, but preferably used only in simple and constant environments, sensitive to sunlight)
- GPS navigation: satellites are used to determine the position of the AGV (adapted to the outdoor environment, but low precision and cannot be used inside)
Which Charging Strategy?
AGVs operate on batteries and there are different options to manage charging:
- Battery swap. When the battery level falls beneath a certain point, the AGV is redirected to a station where the battery is replaced by a fully charged one. The swap can be done manually or automatically. The advantage of a battery swap is that it limits the unavailability of the AGV to a minimum. The disadvantage is that extra batteries must be purchased and stored.
- Automatic charging. When the battery level falls beneath a certain point, the AGV is redirected to a charging station. During charging time, the AGV is not available, which means that more AGVs are needed, for example, the battery can last during all day shifts and be charged at night.
- Opportunity charging. The AGV is redirected to a charging station when an opportunity arises. This is a solution to consider if AGVs are stopped and idle several times a day.
IT Impacts
Unless AGVs simply move back and forth across predefined and independent paths, there is a need for a central management of the fleet of AGVs. All AGV vendors propose an AGV Control System, which is proprietary software allowing to:
- Program vehicle routes, using a map of the facilities and of possible paths previously entered in the system
- Fulfill transportation orders, by selecting an available AGV and ordering it to go from point A to point B using a given path
- Monitor vehicle statuses and locations
- Interact with other systems, such as manufacturing ERP software or Manufacturing Operations Management (MOM) software Systems
Having a well-working AGV Control System also means addressing the IT challenges of a reliable wireless network and integrating with IT and OT Systems. Simulating the AGV fleet before its commissioning can also bring a lot of benefits.
Wireless LAN
Individual AGVs need to maintain constant communication with the AGV Control System through a wireless network, either to receive orders or send back field data.
The deployment of the wireless solution needs, therefore, to be carefully planned and tested. For instance, if antenna fields do not have sufficient overlap, this can result in the AGVs sometimes losing contact. The industrial environment may also cause interferences or other issues. For example, industrial metal surfaces such as those used in racks can cause a reflection of radio waves, preventing a well-functioning connection.
Integration with Other Systems
In order to fully automate transportation operations, the AGV System needs to communicate with other Systems, such as the ERP and MOM systems.
Transport orders need to be created and scheduled according to demand and capacity. The Warehouse Management System then needs to check the availability of the storage bins, communicate the location of the palette or goods to be transported and update the inventory after the transportation has been done. Integration with other components of the MOM system (Production, Quality) can allow a full traceability of the materials from receipt to final delivery.
AGV Fleet Simulation
Finally, a program that can simulate the operations of a future AGV fleet can prove useful to:
- Verify that the AGV fleet has been properly sized,
- Assess the efficiency of the routing and of the battery charging strategies,
- Experiment “what if“ scenarios with unexpected events, such as a human crossing the path of an AGV or several AGVs being down
Conclusion
Cheaper and more accurate sensors, better vision recognition, quicker-charging batteries, intelligent collaboration within an AGV fleet… AGVs will benefit from all these advances in the future, making their usage even more compelling and their deployment easier. In the meantime, and as we have seen, companies need to evaluate the business case for AGVs, select an AGV type that can support all the required loads, make sure the environment is suitable for the AGV navigation system, implement a reliable WLAN infrastructure for AGVs and properly integrate other systems, such as MOM software, with the AGV Control System.
Continue the conversation by joining our DELMIA Communities on 3DSwYm. Membership is free.
[1] The No-Hands train, a 1958 implementation of Barrett Electronics’ invention in a refinery [2] A State of the Art Map of the AGVS Technology and a Guideline for How and Where to Use It, thesis from Lund University Faculty of Engineering for Scania, 2017 [3] As of August 13, 2018, a Google search of “accident report detail” along with the terms “AGV” or “automated guided vehicle”, and restricted to the OSHA Web site, provided two OSHA fatality reports, dating back from 1997 and 2008. By contrast, a similar search with the term “forklift” resulted in 493 OSHA fatality reports.