The digital transformation era has completely changed the manufacturing landscape. Manufacturers today are expected to deliver a wide variety of products at an escalating pace without the price hike.
To meet these modern day demands, most have leveraged robots to drive up efficiencies and productivity while remaining efficient. While the capabilities and benefits of robots are undeniable, they are often implemented and operated in silo. This results in manufacturers being unable to maximize the full potential of their robotic solutions.
Why are robots not enough as a standalone robotics solution?
Having robots operate on their own results in a disconnect across manufacturing processes, teams, trading partners and IT systems. Consequently, there is a lack of internal collaboration especially between product design and production, which negatively affects lead times and product quality. Then there is a matter of time sinks and high costs that stem from the time, expertise and specialized software and hardware needed to program robots and set up robotic production lines. Not to mention, each time changes have to be implemented to reflect changes in customer demands, robots have to be taken offline to be reprogrammed—halting production lines. Adding to this is the complexity of manual robot programming. It is error-prone and validation is often done on the shop floor. This can quickly devolve into a trial-and-error session, leading to collisions and damage on the shop floor.
Lastly, due to the specialized nature of robotic systems, it can be difficult to democratize knowledge and expertise—affecting standardization across production lines.
All these challenges translate to longer lead times, increased costs and compromised efficiency—ultimately, hurting the bottom line. That’s why forward-thinking manufacturers are now turning to a robotic virtual twin to elevate their solutions.
What is a robotic virtual twin?
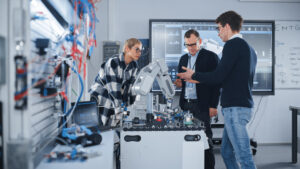
It is a virtual representation of a physical robot and its environment that provides manufacturers with:
- A flexible and agile system that responds immediately to changes in product design, materials and production methods
- A shared platform that drives collaboration across the value chain
- A user-friendly interface that simplifies programming and reduces the need for specialized software and hardware
- Real-time data and insights into the performance of robotic systems
- A streamlined process for installing and maintaining robotic systems
- A centralized repository for data and information about robotic systems
This enables digital continuity across product engineering, process engineering software, robotics and virtual commissioning.
How does DELMIA Robotics solution help manufacturers build competitive advantage?
DELMIA Robotics software, which operates on Dassault Systèmes’ 3DEXPERIENCE platform is a manufacturer agnostic solution that can work with a wide range of robotic systems. It also has a huge robot library with all major robot vendors and is updated with new robots in the market regularly.
With DELMIA Robotics, manufacturers will gain unprecedented levels of interconnectivity and flexibility to cater and adapt to changes. This is because any changes made to the product design are automatically reflected in the robot trajectories. It also supports a very extensive list of processes from material handling to point-to-point to fabrication and more.
In addition with the 3DEXPERIENCE platform, stakeholders can now easily exchange data and collaborate. For example, non-experts, such as managers and sales personnel can review work cells through a web-client without a robotics license.
This capability in turn facilitates knowledge sharing of all processes and robot models across different sites. With the benefits of embedded robotics expertise in the platform, it is possible to develop a worldwide center of excellence and define best practices. It makes it easier to manage complex processes and parameters, configuration and automation.
Looking toward the future of robotics software
Manufacturers must understand that as the world continues evolving, so must their solutions. It is no longer enough to merely incorporate robots in their production process without a way to unlock digital continuity throughout their value chain. With DELMIA Robotics, efficiency, cost-effectiveness, productivity, agility, flexibility and future-ready operations are well within grasp.
Discover the real-life value of leveraging DELMIA Robotics to unlock manufacturing excellence by downloading our eBook on Enabling Digital Continuity with the Robotic Virtual Twin now.
Listen to DELMIA’s Global Operations on the Go podcast on robotics.