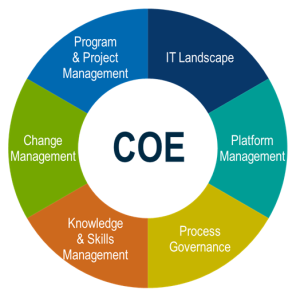
In my work with global manufacturing companies, I am increasingly hearing people talk about implementing a Center of Excellence or COE. There are several reasons for implementing a COE, such as to assure process consistency across locations, better address regulatory requirements or to streamline continuous improvement initiatives. The customers I speak with ask similar questions: What people should be involved? How should they operate?
What is COE?
At DELMIA Apriso, we define a COE as a formal, centralized process and organization for managing, developing and deploying continuous improvement to manufacturing processes. These manufacturing processes are part of a single, unified solution used in all the plants.
Typically, a COE consists of a multidisciplinary team of experts. The first part of this group is a governance team, consisting of the process owners. They decide what process changes are needed and should be applied. This group frequently travels to the plants while also being aware of the various business needs and constraints. They may or may not be the budget owners. The second group is the IT specialist’s team that – based on the scoping decisions done by the process owners – actually makes the changes, tests them and then distributes to the plants.
Just as software companies write new code in cycles, a COE is built in the same way. A cycle consisting of scoping-decision-design-development-testing-deployment may be as short as 4 weeks or as long as 3-4 months.
Purpose of Center of Excellence
A common misconception is that a COE is a top-down, cookie-cutter approach to manufacturing, where standard processes are forced onto local plants. While process standardization is essential, COE owners in some of the most successful implementations I have seen view their COE as a clearinghouse of ideas, or a hub where information flows in from plants all over the world. This way process improvement, regardless the point of origination, is discovered and leveraged in a systematic way.
To make this work, a Center of Excellence should involve plant-level representation, ideally from multiple regions, for an accurate evaluation of your firm’s overall manufacturing practices. There needs to be a regular process for submitting and reviewing suggested improvements. Some manufacturers hold regular meetings where ideas are presented and vetted. Others use an email “suggestion box” that goes straight to the COE committee. Others are now starting to use social-media-like systems to enable on-line collaboration between plants’ representatives and process owners.
The method doesn’t matter. What’s important is that ideas for process improvement flow up to the COE, not just down from the COE. When used this way, a Center of Excellence is more than a method of enforcing best practices. It becomes a means of leveraging the experience and skills of every manufacturing employee in the enterprise, ensuring that improvements, no matter where they come from, are discovered, evaluated and deployed everywhere – to the benefit of the entire enterprise.