Sustainability and profitability have long been considered conflicting goals in packaging industry. This is because the pursuit of sustainability adds a layer of complexity to the challenges manufacturers already face daily on the shop floor.
However, in recent years, there has been a growing environmental movement supported by strict government measures and environmental, social and governance (ESG) initiatives. This has led to customers choosing brands that are committed to reducing their ecological footprint. Consumers and governments are increasingly pushing for reduced plastic usage, increased recyclability, biodegradability, and overall eco-friendly packaging options.
This shift in customer behavior and demand has affected the packaging industry significantly as they have long relied on plastic.
Packaging companies are now finding themselves at a crossroads. Already battling increasing costs from having to meet evolving customer demands for higher quality and more personalized products—are they able to add sustainability into the mix while remaining cost-efficient?
The answer is yes. Companies, such as Boticário Group have found that the right integrated manufacturing solutions can drive innovation, paving the way for future-ready operations.
Brazil’s Boticário Group leveraged modernization to become an industry leader
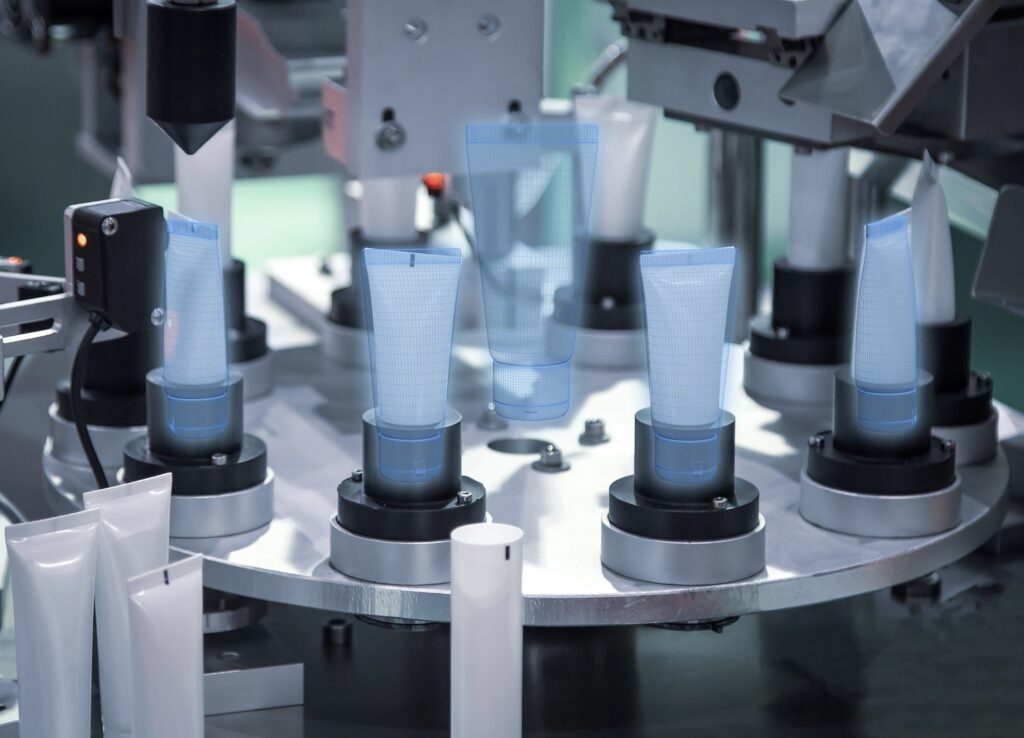
DELMIA in the Packaging Industry
Here are three main ways DELMIA enhances packaging companies’ capabilities to strike the right balance between profitability and sustainability—ensuring business continuity in an increasingly competitive and complex landscape.
- Increased Visibility: With DELMIA, businesses gain full visibility into everything that takes place on the shop floor. This allows them control over process indicators, enabling them to improve delivery, performance, quality, safety, productivity and cost-efficiency. Leveraging real-time visibility, companies can also make accurate demand forecasts as well as easily identify and mitigate potential bottlenecks. By aligning procurement with production, it facilitates just-in-time manufacturing—minimizing wastage.
- Automation: Automating menial manual work such as data capture and entry allows workers to focus on value-added work, which ups their productivity. Automation can also be extended to quality checks and assurances. This ensures products adhere to safety standards and minimizes the risk of product recalls and hefty fines. In addition, a well-connected shop floor translates into operators receiving real-time data. This is especially crucial in the event of a disruption as it enables them to make well-informed decisions quickly.
- 3D representation and simulation: The DELMIA Virtual Twin Experience (VTE) bridges the gap between product design and manufacturing by utilizing a virtual twin and simulation capabilities. A virtual twin is a digital replica of the product that is built and updated with real-world and real-time data. Optimization can be done virtually before manufacturing takes place in the real world. VTE can also run simulations to test how the virtual product withstands stresses as well as identify any potential issues. These capabilities increase the chances of manufacturers achieving first-time-right quality, which accelerates time-to-market. This is an especially critical factor for packaging companies as they experiment with various materials for sustainable packaging. VTE allows them to construct, interact with and evaluate models of different materials to determine the best option before costs are incurred for a physical prototype.
Real-life case study: Boticário Group
Brazil’s Boticário Group, one of the 15 largest and seventh most sustainable beauty companies in the world lacked visibility into their shop floor. They were unable to track their Overall Equipment Effectiveness (OEE) and capacity.
This meant they were unable to:
- Identify losses and measure progress
- Predict bottlenecks in supply chain and production
- Increase productivity of equipment to minimize wastage
- Optimize time management to receive new product volumes
After implementing DELMIA, Boticário was able to ensure efficient use of materials right from the design stage. With real-time end-to-end visibility of all processes and operations, they were also able to respond quickly to disruptions and ensure flawless manufacturing execution, minimizing wastage.
In addition, they could predict and minimize disruptions such as bottlenecks from filling machines as well as schedule preventive maintenance for equipment across operations.
Lastly, with automation and the merging and simplifying of several activities into a single system, operators were able to ramp up their skills quickly, improving knowledge retention across the organization.
To learn how transforming your shop floor with DELMIA can help you unlock innovation and operational excellence to meet modern day demands, download our eBook “Drive Sustainability and Profitability in Packaging by Transforming Manufacturing Operations” now.
Watch how 3DLean can help you become more sustainable: