Growing up in an area of France famous for its textile manufacturing, it was perhaps fate that Julien Payen found his way into the industry, albeit not in a typical fashion.
As a child in the Hauts-de-France region, he loved science and even dreamt of becoming an astronaut. And while his career path didn’t quite put him on a terrestrial trajectory, it certainly put him on a trajectory to change the world.
Early on in his career, Payen, who has a PhD in materials science, was already ahead of the curve.
He spent the first part of his career helping to design and manufacture face masks that would ultimately be used years later during the COVID-19 pandemic.
“I worked specifically on designing materials that would block viruses from entering the body,” Payen said. “It was a great time to be in this industry because there was a lot of work to be done.”
Textile sciences and healthcare intersect in various ways, including the development of advanced medical textiles for applications such as wound dressings, surgical implants, drug delivery systems, and, like the industry, Payen worked in, face masks.
As Payen’s work on masks wound down, a new opportunity presented itself: Two general physicians and a plastic surgeon who were trying to improve breast reconstruction surgeries approached Payen.
Together, they decided to start growing cells within textile material that could eventually be implanted into the breast. However, initial attempts failed every time. As it so often happens, inspiration struck in the unlikeliest of places. On the long return flight home from a conference in Austria, Payen’s mind kept returning to a presentation from the medical conference he’d just attended.
“An engineer at a German research institute could orient the growth of cells on a specific embroidery pattern” Payen recalled. “It reminded me of Calais lace, a type of lace that France is known for. And I thought: ‘What if we grow cells on this?’”
It was on that flight that he had the idea that he would kickstart Lattice Medical.
And it worked. From there, Lattice Medical was born.
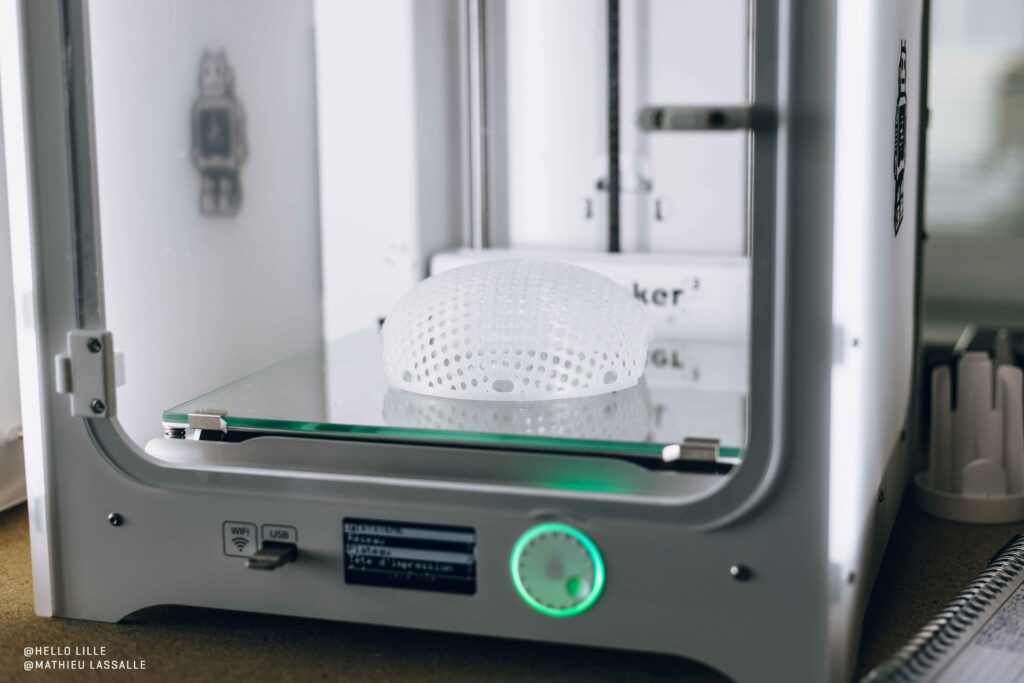
Revolutionizing breast reconstruction
Every 14 seconds, a woman somewhere in the world is diagnosed with breast cancer, totaling 2.3 million diagnoses a year worldwide.
Breast cancer accounts for 12.5% of all new annual cancer cases worldwide, making it the most common cancer in the world. But despite its unfortunate commonality amongst women, certain aspects of breast cancer care and treatment have not been updated to reflect advancements in modern medicine. Due to the limitations of technology and surgical techniques commonly used today, only 30% of women who have a mastectomy will benefit from breast reconstruction. Many women aren’t able to undergo reconstructions or choose not to, depending on a variety of factors from age to pre-existing medical conditions that might rule out their candidacy for the procedure.
Noting this discrepancy in treatment options, Payen and his team set out to improve the odds for patients. Their first order was to create the Mattisse, a 3D-printed, bio-resorbable chamber for natural and customized breast reconstruction. After the Mattisse is implanted with grafted tissue, the tissue begins to regrow around the chamber. Eventually, the chamber dissolves in the patient’s body, leaving them with a naturally reconstructed breast.
With the Mattisse, patients can receive less invasive treatment with a faster recovery time and the desired results.
“Unfortunately, I’ve had women in my life impacted by breast cancer,” Payen said. “I know how hard it can be to go through something like that, and I want to try to make it easier.”
Inspired by the past
With clinical trials underway for the Mattisse involving 50 patients, Payen and the Lattice Medical team have already started on their next project: the Rodin, a new way to reconstruct the skin’s deep layer of soft tissue, also known as the hypodermis, after injury.
Like the Mattisse, the Rodin is also 3D-printed and absorbable by the body. But this time, the application is designed to help with skin and fat grafting.
“Henri Matisse, the painter, was born in the same region of France we are working out of, and he admired Auguste Rodin, the sculptor,” Payen said. “We’ve named these implants after the artists to continue that connection and honor their legacy.”
Payen, whose love of his work and company motivates him to continue with these projects, hopes they will also have a lasting legacy, just like the artists they’re named after.
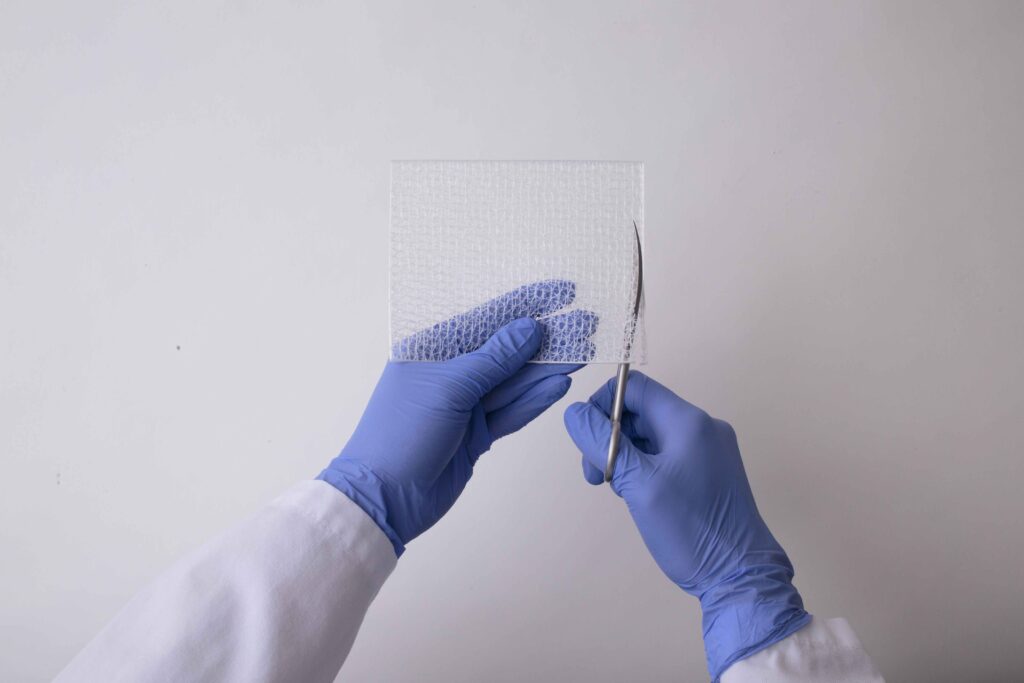
Rethinking the future
In 2023, Lattice Medical was accepted into the 3DEXPERIENCE Lab, Dassault Systèmes’ accelerator program that supports startups whose visions for changing the world align with the UN’s Sustainable Development Goals.
Leveraging a suite of software tools on the 3DEXPERIENCE platform, Lattice Medical can design and print the proper implant, getting each patient’s exact size and dimension specifications to reduce wasted materials. The company uses CATIA and SOLIDWORKS for its 3D modeling work, then transfers those findings to SIMULIA, where their engineers conduct biomechanical simulation tests. To make their efforts scalable, they use DELMIA to ensure their production capabilities and capacities, thereby using a variety of technologies to make products that are not just life-changing, but accessible, too.
“We built our own factory to do everything in a controlled environment. This lets us improve quality, manage costs and reduce waste,” Payen said. “We have a large responsibility, not only with our patients but the planet too. We must do our best to ensure that responsibility drives us further.”
In 2022, to advance this objective, Payen and his team at Lattice Medical established Lattice Services. An offshoot of the parent company, Lattice Services is democratizing access to its products by selling medical-grade filaments and surgical guides to medical facilities and laboratories around the globe. In doing so, they aim to make their innovative approach to medicine accessible and approachable. Through this initiative, they strive to democratize access to these materials, empowering the next generation of medical professionals and engineers with the necessary tools for innovative healthcare solutions.
“These filaments are very expensive and can be hard to access, but how are we supposed to help others learn with them if they can’t use them?” Payen said. “Lattice Services helps make this possible.”
Eventually, Payen is hopeful that hospitals will be able to 3D print organs for transplants and further reconstructive needs.
“Right now, the technology isn’t there,” Payen said. “But maybe a student who can experiment with the materials now will be able to create the next generation of medical filaments for this.”
In the meantime, though, Payen will continue to focus on Mattisse and Rodin, making these technologies accessible to the patients who need them.
“Science is still driving the world now, and we will find new solutions to help the people we care about,” Payen said. “That’s what inspired me, and if others have the same mindset, I think humanity will be in a good position in the future.”
Julien Payen isn’t the only one impacting the future of technology in the medical field. Check out some of the other Humans Driving Progress.