It may be that there’s no “I” in team, but inventory is certainly a major factor in Sales and Operations Planning (S&OP) software. So why isn’t it called SOIP or Sales Operations and Inventory Planning? Truth be told, it actually is called Sales, Operations and Inventory Planning in some parts of the world, notably in parts of Europe. In the U.S. and other regions, S&OP is the term normally used to describe the business planning process that creates a supply plan to match demand, and in truth generates what is essentially an inventory plan. Let’s explore that idea a bit.
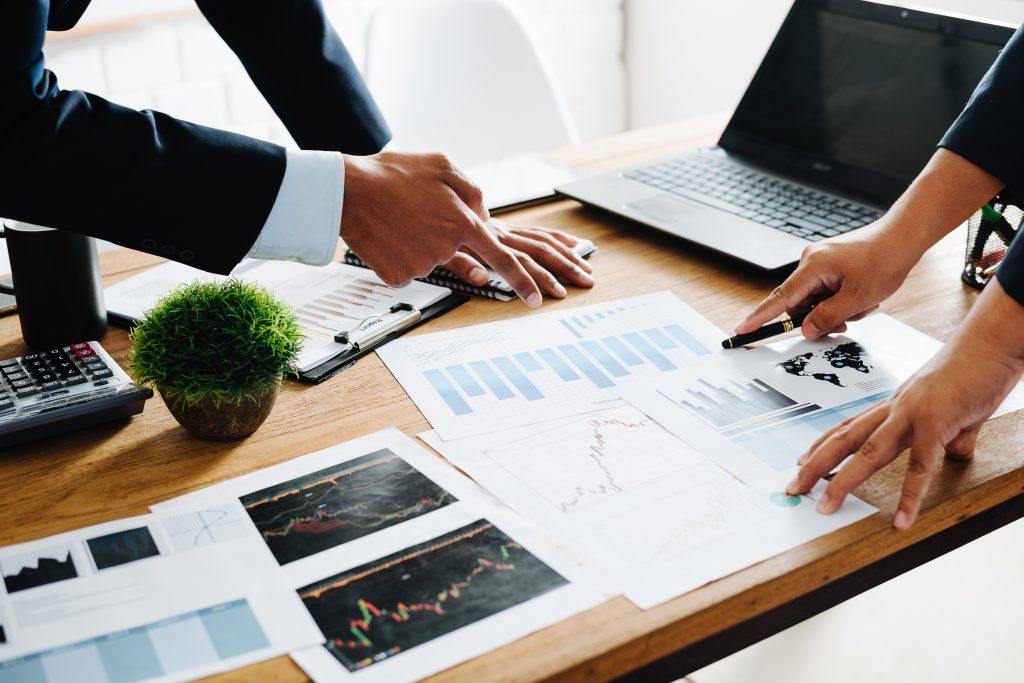
S&OP starts with a demand plan. The planning team – usually made up of executives from key functional areas including sale/marketing, finance, production, procurement, logistics and others – will meet and refine the demand plan so as to meet any concerns, restrictions, or objectives of any of the participation functions. Then an appropriate supply plan is developed. Note that this could well be a back-and-forth process with adjustments to the demand plan required to accommodate production and distribution concerns or limitations. The resulting operational plan is, as much as anything, an inventory plan – what production will make and distribution will move to the proper locations to be available to meet expected demand.
Inventory is a focus of S&OP even though it is not explicitly called out in the name of the process. The inventory plan is actually a by-product of the plan but an important one nonetheless. A prime objective of the planning process is to identify the ‘right’ amount of inventory i.e., the minimum amount needed, to support the customer service (availability or fill rate) goal. Let’s be honest: every company wants to reduce inventory. But inventory is essential to be able to satisfy customer demand while operating efficiently. Even companies that only make products to-order need inventory to synchronize and buffer the production cycle to the demand. They also need stores of materials, components and supplies to support production. So inventory is a ‘necessary evil’. But nobody wants any more than is absolutely necessary.
In S&OP, or SOIP if you prefer, the demand plan is the statement of what you expect the customers to take from your inventory. The supply plan outlines what inventory you will make available to support those sales. The difference is what inventory will be on hand (inventory ‘in’ from production minus inventory ‘out’ from sales). It’s as simple as that. The planning process is focused on finding the best arrangement of production and distribution activities that will satisfy demand with minimal inventory left over.
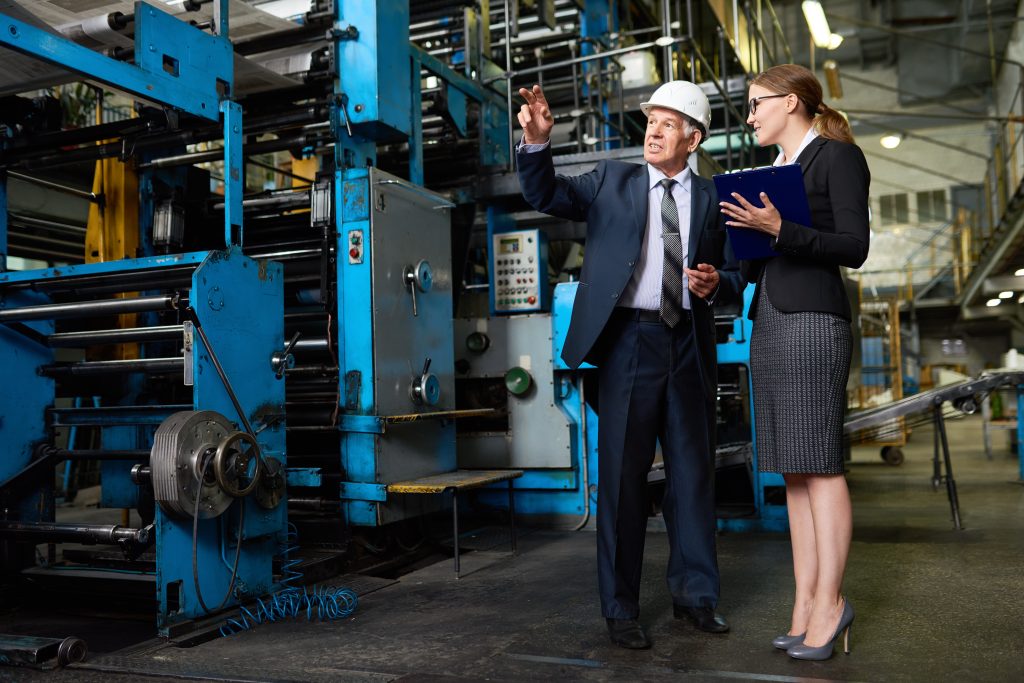
Of course, the reality of supply chain planning and optimization is a lot more complicated than that simple equation. The production plan should make the best use of all resources including people, equipment, materials, etc. by making the best mix of products on the most favorable schedules. Meanwhile, the demand and distribution plan must focus on getting those products to the right place at the right time to ensure that they are ready to ship when the customer wants them. Don’t forget to allow some extra inventory to compensate for demand variability, forecast error, and the inevitable surprises (supply chain risk) that are a part of everyday life in the real world. Oh, and you’ll also want to minimize costs by using the best transportation alternatives to move the most appropriate quantities of products over the best routes. And don’t forget that warehouses have capacity limits and resources (people, equipment, loading docks) that should be optimized as well.
Optimizing all of these resources, capacities, capabilities and limitations to come up with the best (lowest inventory / lowest cost) plan that delivers the desired level of customer service is the essence of supply chain management. S&OP is the process that brings supply and demand together as the basis for developing this coordinated plan. Inventory is arguably the most easily understood measure of success.
Editor’s Note:
Interested in learning more about trends in manufacturing? Check out our Online Manufacturing Summit and register for on demand access to more than 40 sessions covering the hottest topics across today’s manufacturing journey.
