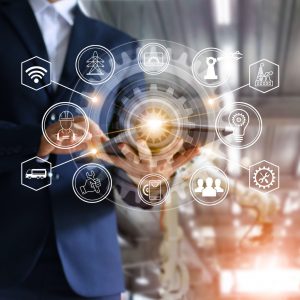
The Industrial Internet of Things (IIoT) promises a whole new world of sensors and smart devices collecting information and control, and extending visibility throughout the plant, warehouse and the entire supply chain. But the prospect of installing, integrating and managing an IIoT network can be daunting, indeed.
Every company will have to decide just how much IIoT technology they want to bring into their environment, and how fast. The first blog in this series offered some general advice and suggestions for those who want to experiment with a few IIoT devices before committing to a larger IIoT project. The second blog offers general advice for companies that are ready for a full commitment to IIoT in the plant and/or warehouse. This third and final blog applies to companies contemplating IIoT in the supply chain – outside of the local plant and warehouse. You may want to read part 2, even if you are only doing IIoT outside the plant (in the supply chain).
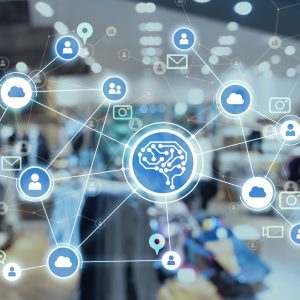
Adding IIoT in the plant is, in many ways, a continuation of a long-running process of bringing systems support closer to the realities of the plant floor. Manual reporting was supplanted by bar-code scanners and touch-screens; paper documentation is giving way to workstation terminals; voice recognition enables hands-free operation. Now IIoT is collecting more data (without additional burden on workers) and making more information available through wearables, tablets, smartphones and other devices.
It’s not quite so clear-cut beyond the walls of the plant and warehouse, however. When items ship – be it a small package, pallet, container or truckload – there is typically little or no information coming back to the plant or warehouse except notice of delivery… and even that is not common and usually not very timely.
IIoT changes all that. Location-aware devices coupled with detailed tracking of each item, case, pallet and container (and environmental conditions for manufacturing quality control) offers a whole new level of supply chain management including such capabilities as the redirection of en-route goods to places where they might be more needed. And that’s in addition to better management of the supply chain from knowing demand, inventory locations and levels, and shipment progress more precisely.
IIoT in the supply chain
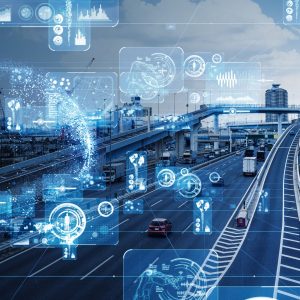
Adding IIoT into your supply chain can be more of a challenge than adding devices to in-plant networks. This is plowing new ground as there isn’t a history and infrastructure for reporting to work from; there are no existing networks and systems to add to; the devices will be installed and operating in locations outside of the plant/warehouse where there is little or no control. That said, the points made in the previous blog relative to in-plant IIoT apply here too:
- No company would (or should) expend money and resources without knowing how that investment will benefit the business – document the expected return on investment (ROI) as you begin to lay out the project plan.
- Scope. One of the biggest factors in failure to complete a project successfully is the phenomenon commonly known as “scope creep”. Lay out a plan and stay focused – don’t be distracted by additional opportunities that come into view. Save them for phase II.
- Existing systems and networks. While the interfaces to existing systems are still required and present challenges, it is a different situation with supply chain data. Activity reports can usually be brought in through open interfaces incorporated in most systems so that part should be relatively straightforward. The bigger issue is having software that can truly use the data. Modern supply chain systems – including inventory optimization, demand planning software, analytics, etc. – thrive on near-real-time data and the ability to apply advanced algorithms, simulation and machine learning to plan and manage supply chains.
- Technical issues. With supply chain IIoT, the biggest technical issues are communications (often relying primarily on cellular data communications), and security. As with internal data, carefully choose suppliers, protocols, and security that will serve your needs today and have the best prospects for moving with you into the future as your needs grow and technology evolves. Nobody can predict with any level of certainty how technology will change so choosing technologies and protocols is less important than choosing partners (suppliers) that show a commitment to keeping their products up-to-date, providing outstanding customer service and support, and have the financial strength and stability to succeed in their markets over the long term.
- The people side. Your organization may be new to the abovementioned supply chain systems and their value is so apparent that user resistance should be minimal – but even so, don’t neglect the need for education and training. No matter how “intuitive” or “user friendly” a system is purported to be, users will need an understanding of what the systems do and how. They will need to know what they are seeing and just what the systems are telling them in order to trust them and put them to effective use. Involve the users early on as the systems are initially envisioned and planned. Encourage a feeling of ownership among the user community so they will be invested in the systems’ success.
Modern supply chains in today’s global, highly competitive markets are complex and dynamic. The systems that have been developed to plan and manage these supply chains rely heavily, as all systems do, on data that is as accurate and timely as possible. IIoT helps gather and manage that data so IIoT has become a big component of supply chain management.