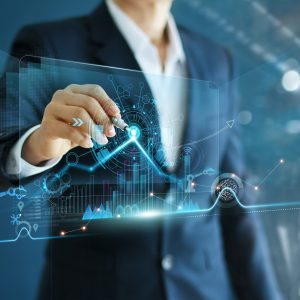
Lean manufacturing software occupies a storied place in the history of making things, a decadeslong drive to achieve efficiency and remove waste by streamlining operations and continuously improving processes. The mission that began with manual notations on clipboards has now reached fruition through digital manufacturing, which enables Lean through continuous communication of real-time data to help nip any wasteful excess, step or process in the bud.
Lean manufacturing was derived from the famed Toyoda Production System (TPS), with its relentless drive to eliminate waste. But if you submitted a swab of Lean DNA to an ancestry site, you’d find its roots go back to the early 20th century. Scientific management proponents such as Frederick Winslow Taylor and Henry Ford emphasized standardization and best practices to eliminate non-value-added actions from the manufacturing process.
Lean is built around continuous improvement, and the first teams walked around plants picking apart processes and taking notes. Think of digital transformation in manufacturing as the computerization and automatization of these continuous improvement crews. Enterprise manufacturing intelligence software is the key to today’s digital transformation of Lean, letting you extract data from your manufacturing processes for storage, collation, contextualization and analysis. Digital transformation enablers like Manufacturing Execution Systems (MES) software and Manufacturing Operations Management (MOM) software then let you transfer Lean lessons learned down to the machine, cell and production-line level.
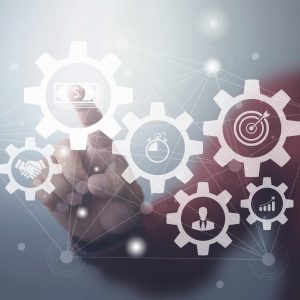
Lean reaches culmination when you tie everything together in a broader digital integration that moves the needle from tackling individual trouble spots to continuous improvement across the enterprise. Big data, analytics and machine learning are critical to this formula, leveraging widespread, bidirectional connectivity to individual assets, machines and devices via the Industrial Internet of Things (IIoT) to fill up the data lake for scrutiny.
A single, unified digital collaboration platform is also vital. It provides a single repository for all the data and initiatives tied to purging waste and continuously improving the manufacturing process. It also lets you train your sights further upstream and downstream, to design and engineering as well as to after-sales analysis, and digital twin feedback to product development, so Lean can embrace the lifecycle from ideation through consumption, recycle and reuse.
Companies are seeing the results of digital transformation to reach Lean. One multinational combined MES and manufacturing and business intelligence solutions to increase first-pass yield on production lines to almost 99.5%. Another focused digitization on a system that targets asset downtime to pinpoint the causes of machine breakdowns, highlight inefficiencies during shift changeovers and isolate anything having a deleterious effect on equipment efficiency. A Lean initiative at a third company connected the shop floor and enterprise digitally, decreasing lead times by 50% and reducing the time that inventory collects dust by 30%.
A top trend today in consumer technology is using wearables to track all the movements that make you more fit. Think of digital transformation as a massive, all-embracing wearable that lets you track all your manufacturing processes to keep you fit, Lean and competitive.