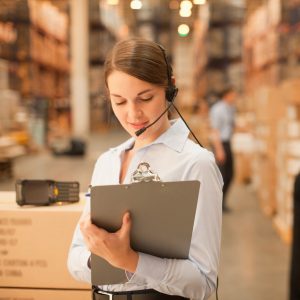
Last Friday morning I ordered 3 items from Amazon. I didn’t pay for shipping because my Prime membership includes free 2-day delivery on virtually everything ordered from the e-tailer. One of the items qualified for free one-day delivery and I received it on Saturday – shipped from Nevada to my address in New Hampshire. The other two items arrived on Sunday, one from Kentucky and the other from Tennessee. Fast, free delivery is a major component of Amazon’s market strategy, essential to competing with brick-and-mortar retailers. But how can this possibly be affordable?
One might think that the most efficient (lowest cost) supply strategy would be to ship all three items together from a single location, in one box. But that would require centralized warehouses with enormous inventory as well as (expensive) shipping infrastructure and resources to be able to ship items long distances within one or two days to meet their delivery objectives. Amazon has chosen to stage various items in strategic locations and handle each item separately, if that’s what it takes.
Complex Supply Chains Need Planning Software
And how did they know that would be the low cost solution? How did they determine where to put the warehouses and which items (and how much of each) to store in each location? I have no inside information on how Amazon does it, but these and many other questions can only be answered with the help of supply chain planning and optimization software. The number of factors to be considered, the complexity of the supply network, the sheer volume of items and transactions, the interaction between factors (speed versus cost for transportation alternatives, for one simple example) make it simply too much for one person or even a team of talented and dedicated individuals to understand and manage successfully.
Dynamic Planning Requires More Than Spreadsheets
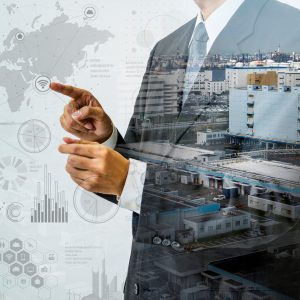
I’ve known some planners who could do some amazing things with spreadsheets including laying out a plan for multiple plants producing large quantities of product and coordinating supply and distribution on a global basis. But the resulting plans were simply adequate and not particularly efficient, did not “optimize” the use of resources, and resulted in too much inventory throughout the network to accommodate uncertainties, keep the plants running, and deliver reasonable (but not great) customer service. And worst of all were not at all dynamic. Whenever there was any change in demand, factory operations (production disruption from any cause), disturbance in supply or delivery, quality issue, or any of a thousand other things causing a variation from the expected, the spreadsheet could not suggest an adjustment to correct the situation. Yes, the planner could enter changes and see the expected results but that’s more a matter of bookkeeping than planning.
The Power Of Simulation And Machine Learning
Today’s supply chain planning systems do more than just apply math to basic data – like in traditional MRP or DRP. Modern planning systems use simulation and machine learning to ‘understand’ the dynamics of the supply chain and determine the most likely result of current conditions and directives. When a deviation is detected, the planning system can project the effect into the future using an extensive base of history to determine what is most likely to happen. If the result is less than optimum, the simulator can try literally thousands of possible corrective actions, in seconds, and suggest the best alternative to bring things back into line and get the product made and into the hands of the customer at minimal cost and disruption.
In today’s global business world, with ever increasing customer expectations and demands, there is constant pressure to deliver faster and more reliably. Supply chains are more complex than ever and are constantly asked to do more for less, and do it faster. Modern transportation resources are a critical link in the supply chain but, like all other resources, they must be planned and managed effectively with a critical eye on the other resources – inventory, production, warehousing – to make sure that the entire mix is truly optimum, that is, used most efficiently to deliver the desired level of customer service and the lowest practical cost. The complexity is far beyond what mere humans can manage, even with a desktop full of spreadsheets. Fortunately, Integrated planning systems are getting smarter and more comprehensive every day to harness IIoT, machine learning, simulation and Big Data to help planners keep up with the dynamics of real world supply chain planning and optimization.