Steel is the most commonly used metal in the world and is widely considered one of the most sustainable materials.
Once made, it can be recycled over and over again without losing any of its properties. Yet the current process for producing steel is less environmentally friendly. In fact, steel manufacturing is one of the worst culprits for greenhouse gas pollution, responsible for 8% of total carbon emissions and the biggest producer of CO2 than any other heavy industry. The term green steel refers to a breakthrough manufacturing process of using hydrogen instead of fossil fuel, creating a minimal carbon footprint.
Facing pressure to meet global net zero targets, policymakers are calling for urgent action across the steel manufacturing sector to switch from coal-blast furnaces to low carbon production methods. That’s why we’re hearing more about green steel, which has the potential to cut carbon emissions by as much as 95%.
How can green steel help us reach net zero?
The International Energy Agency (IEA) says that if we are to meet the world’s climate goals, steel-related emissions must be reduced in half by 2050. Should steel makers be successful in transitioning to green steel production, the impact would be transformational.
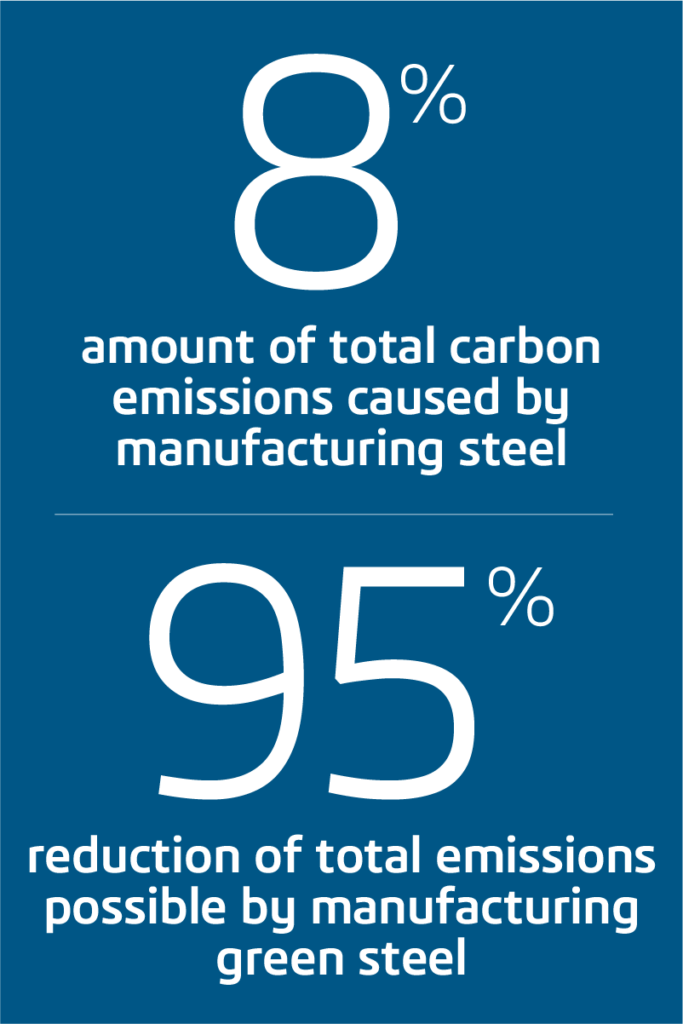
In 2021 alone, global production of steel reached almost 2,000 million metric tons, the majority of which was made in coal-fired blast furnaces. These furnaces are heated to over 1,000 degrees centigrade, requiring vast amounts of energy and pumping huge amounts of carbon dioxide into the atmosphere.
“Until now, fossil fuel-powered plants have been the only viable way to obtain high-quality iron at the scale needed to produce enough steel,” reported Mitsubishi Heavy Industries (MHI) Group’s Spectra magazine. “This energy-intensive process means the industry actually produces more CO2 than steel — around two [metric] tons of CO2 are emitted for every ton of liquid steel produced.”
Green steel essentially eliminates the use of fossil fuels in production by replacing them with hydrogen, which emits only water when burned. If steel makers use “green hydrogen” – generated with just water and renewable electricity – then the complete process could be entirely carbon emission free.
As global demand for steel continues to soar, steel makers face the dual challenge of ramping up production and reversing their carbon emissions trajectory. Key players across the industry have begun to explore how to do this, with the first commercial-scale green steel plants expected to enter operation within the next three years.
How is green steel produced?
Fundamental to the production of green steel is the transition from blast furnaces to hydrogen. Primetals Technologies (part of MHI Group) has already successfully produced green steel using hydrogen at its HYFOR green steel pilot plant in Donawitz, Austria, which has been in operation since mid 2021.
Meanwhile in Boden, Sweden, construction is underway on H2 Green Steel’s new plant, which will generate its own green hydrogen on site and plans to make the first commercial batches of green steel by 2025.
In both of these cases, green steel is made from direct reduced iron (DRI) created using hydrogen instead of coal. This means that the iron ore reacts with hydrogen rather than carbon atoms, creating water as a by-product instead of CO2. To further reduce energy consumption, the steel is melted, cast and hot rolled in a continuous process.
Creating the next-generation green steel manufacturing plant
Similar ventures focused on hydrogen-based steel production will only help to raise awareness and investment in green steel manufacturing. As momentum grows, it’s hoped that more steel manufacturers will make the switch to carbon-cutting processes rather than reinvesting in their existing coal-fired infrastructures. When you consider that 71% of blast furnaces are due for major refurbishment before 2030 and the remainder before 2040, we face a crucial window of opportunity to go all-in for green steel production rather than facing “carbon lock-in.”
Of course, the considerable task of replacing every blast furnace around the world must not be underestimated. Steel manufacturers will need to commission new plants and engineer completely new steel production lines, at great effort and cost. And they must have access to abundant supplies of net-zero hydrogen.
To speed up the transition, McKinsey recommends that steel manufacturers follow a clear decarbonization road map. “This could entail first optimizing blast furnace processes, then switching to electric arc furnaces (EAF) using scrap and DRI powered with natural gas – and ultimately adopting carbon-neutral EAF production using a mix of scrap and hydrogen-based DRI,” said the report.
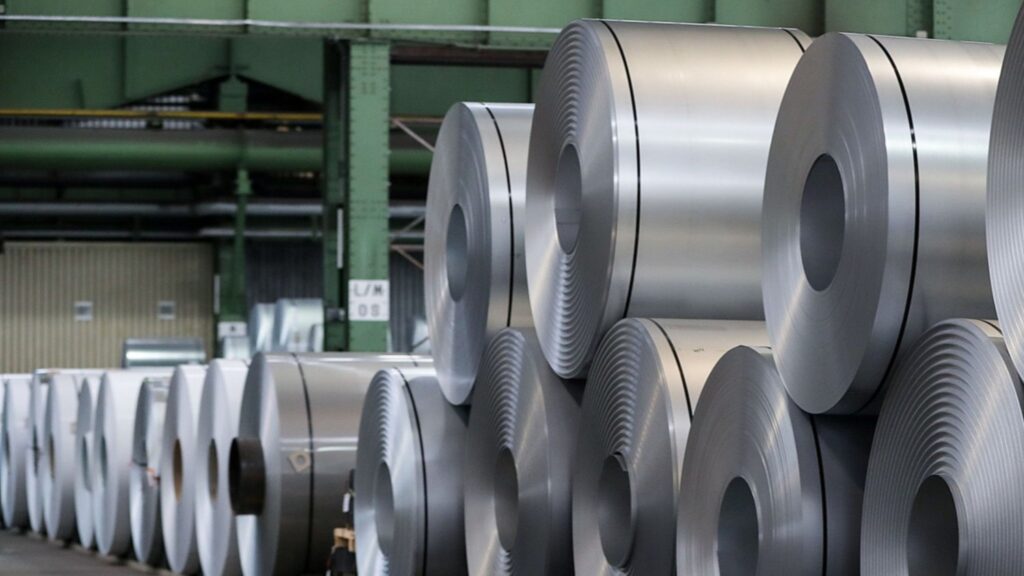
How does Dassault Systèmes help the transition to green steel?
Amongst all this radical transformation, digital technology will play a critical role in helping steel producers redesign and optimize their manufacturing plants and create fully integrated production processes.
Dassault Systèmes is already having conversations with movers and shakers across the industry about how they will make the transition to green steel production and the technology they will need to support them. In particular, they will require powerful tools to design and engineer their new facilities and simulate their processes in the virtual world ahead of live production. They will also need strong product lifecycle management and short-term production planning software capabilities to optimize their resources and achieve full transparency across the value chain. Two key technological developments will play a key role in this:
– Virtual twin experiences:
To manage thecomplexities of designing, building and running new facilities, steel companies will model, test and optimize their entire operation setup in the virtual world. This virtual twin will follow the plant at every stage of its lifecycle, from commissioning to ongoing maintenance. It will allow companies to track all physical assets and systems, and capture and store knowledge related to the plant, helping to simplify production, reduce costs, minimize downtime, improve worker safety and more.
– Lifecycle assessment (LCA):
As sustainability targets move higher up steel companies’, buyers’, investors’ and policy makers’ agendas, the ability to monitor and measure the environmental impact of steel throughout its entire lifecycle will become critical. Built on the 3DEXPERIENCE platform, the dedicated Sustainable Innovation Intelligence solution will allow steel companies to carry out an in-depth LCA and accurately measure the end-to-end environmental impact of the steel they make.By combining LCA data with virtual twin technology, they’ll be able to set optimal process parameters to prevent energy loss at every stage.
Dassault Systemes is a key partner in the transformation of steel manufacturing
Over the coming years, key stakeholders across the industry, including Dassault Systèmes will make critical decisions that will define the entire future of steelmaking. New innovations will bring down cost barriers, new ecosystems will form, new workforces will need to be trained and new policies will put sustainability well and truly in the spotlight. The green steel race has already begun, and the winners will be the ones who are ready to adapt, embrace digital transformation and invest in the right technologies to make net zero a real and viable possibility.
Find out more
Green Steel: Can We Make Heavy Industry Have a Lighter Impact?