Did you know that the greatest basketball player of all time, Michael Jordan, was cut from his high school team? Or that Walt Disney was fired from his job at a newspaper early in his career for lack of imagination? And, of course, you know the Wright Brothers’ first few attempts didn’t go exactly as planned.
These famous setbacks serve to illustrate that failure is not only a part of life, but is actually an essential component of innovation.
From Thomas Edison’s famous quote about “finding 10,000 ways that won’t work” to the modern Silicon Valley mantra of “fail fast, fail better,” innovators have long understood the value of failure in pursuit of innovation. However, for many, the fear of failure can be daunting. While innovation is about trying new things and taking risks, fear of failing can stifle creativity and discourage the type of risk taking that’s vital to true innovation and advancement.
In the United States, risk-taking and entrepreneurship are admired, so failure tends to be tolerated as a learning opportunity and a “bump in the road” toward success. Think about Henry Ford, whose first two automobile companies failed, and who famously said, “Failure is simply an opportunity to begin again, this time more intelligently.” In the US, a common job interview question asks for an example of failure, so the applicant has a chance to share what they learned from the experience.
While American enterprises regard failure as a valuable learning experience, around the world, cultures have differing points of view on the value of failure. And some of them believe failing – even in pursuit of innovation – can hurt perceptions among investors, partners, potential employees and other key stakeholders.
In Asian cultures, however, failing in a business venture can be seen as an embarrassment and damage a person’s or company’s reputation. In Germany, failure is seen as weak and inefficient, and great care is taken to minimize its likelihood. And in France, where the culture prizes stability and predictable outcomes, there’s an aversion to risk and fear of failure that can hinder entrepreneurial efforts. A Les Echos article comparing the French perception of failure with the American model opined that failure in France equals defeat, and the one who fails is seen as one who did not work well or follow the rules.
While no one likes to make mistakes, fear of risk taking, of criticism, of uncertainty, of loss of control, can hold back advancement at the personal and corporate levels, leading employees and managers to avoid experimentation and risk-taking, eventually leading to apathy, conformity and playing it safe. The irony is that fear of failure leads to a failure to innovate.
It doesn’t have to be that way.
Creating safe-to-fail environments
For entrepreneurs, the ability to test, fail, pivot and restart without fear of losing funds or valuable partners is essential. In recent years, a number of initiatives have sought to normalize failure, while technological advances have begun to reduce the risks.
One creative way to destigmatize failure comes from Adam Kingl, author of “Sparking Success,” who recommends organizations embrace mistakes by throwing “failure parties.”
These quirky events provide opportunities for team members to discuss, in an informal atmosphere, situations in which they experimented with a hypothesis, tested a prototype, or explored a new avenue in which things did not go according to plan, and then share what they learned. To shift a team’s attitude toward failure requires fostering an environment of vulnerability, Kingl says, where colleagues are comfortable, even eager to share their learning from every experiment they attempt.
Rather than viewing failure as a personal shortcoming, teams can learn to consider it as a step toward progress. Analyzing root causes of failure and implementing lessons learned, can drive innovation and lead to positive outcomes, Kingl says.
A decade ago, the San Francisco startup scene birthed FailCon, a one-day conference designed to prepare founders, developers, designers and investors to learn from inevitable failures in order to iterate faster. The event has since grown to where Brazil, Hong Kong, Israel, Spain and several French cities are hosting FailCon’s of their own.
But even better than removing fear of failure is removing the risk from it. Enter: science-based modeling and simulation.
Science-based MODSIM minimizes risk
It used to be that you’d have to make it to break it. Not so anymore.
With science-based MODSIM, you have the ability to combine computational testing with physics-based simulation as a foundational part of the innovation process. The 3DEXPERIENCE platform is the only MODSIM space that allows combining the creation of a product in a virtual world with the ability to play things in context to understand the impact of the product.
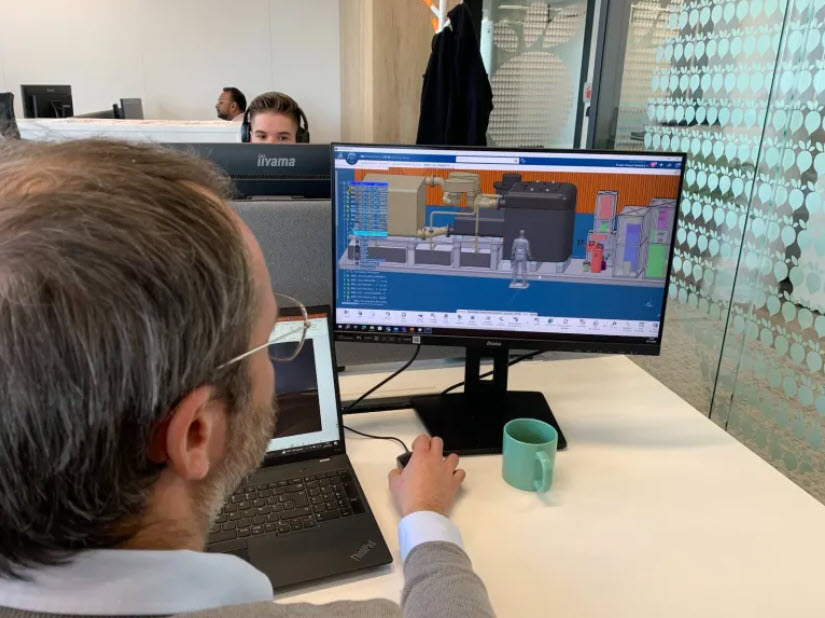
Incorporating MODSIM into the process requires less real-world testing and prototyping, lowers cost and, most crucially in terms of fear of failure, reduces risk. The value is huge. Experiencing the impact during the shaping helps ensure the right choices are made for all scenarios.
As a result, by the time you’re building physical prototypes or conducting testing in the real world, you’re primed for success and high-quality products can get to market faster.
Examples of innovation through MODSIM
Consider, for example, the German company, EVUM Motors.
EVUM Motors wanted to be first to market with its aCar, a modular electric utility vehicle. The goal was to develop a green, affordable 4×4 work truck that could handle a variety of tasks, run on rugged terrains, and be easily manufactured and financed in developing and emerging countries.
“There is a short window of time for entry into electromobility. You have to be quick with a reliable, full developed product on the market,” said Martin Ŝoltès, co-founder and managing director of EVUM Motors.
As it worked to establish itself in the highly-competitive EV industry, EVUM Motors used CATIA on the 3DEXPERIENCE platform to connect design, engineering and manufacturing teams to quickly deliver access to digital design and simulation applications. Today, EVUM Motors is getting ready to produce the aCar from its manufacturing facility in Bayerbach, Germany.
Ŝoltès credits the 3DEXPERIENCE on cloud for helping EVUM motors “accelerate development.”
The MODSIM approach was also critical for the French start-up NAAREA, which used the 3DEXPERIENCE platform to develop a virtual twin of XAMR, its pioneering micro nuclear reactor.
Virtual twin technology enabled the company to simultaneously design and simulate, managing all design, engineering and manufacturing processes within a centralized ecosystem, developing the project from the ground up in just 18 months.
To achieve its ambitious objective of delivering carbon-free and decentralized energy, French startup NAAREA created a version of the reactor in a virtual environment on the 3DEXPERIENCE platform. They were then able to run laboratory tests and feed data from the experiments into XAMR’s virtual twin to test safety features and analyze performance ahead of its prototype production.
“We want to be on the market by 2030, so we need to move fast,” said Jean-Luc Alexandre, NARREA’s CEO. “The best solution to achieve our goal is the virtual twin. One of the best features is that we can design and simulate as we go, so we can test our ideas and see if they’re worth progressing. The 3DEXPERIENCE platform also supports us to work together in a really collaborative way.”
Did you know it costs about $300 million dollars to develop a rollercoaster? Theme park operators are always seeking faster, bigger and more extreme thrills to lure visitors to their parks, but at that price, they want to be sure the design will be safe and successful before it is even built.
Extreme Analyzes Engineering, an Italian amusement parks and rides engineering company, is using the 3DEXPERIENCE platform to virtually create and test rollercoaster twists and turns to develop new rides, test prototypes and, in turn, reduce development time and running costs.
“Using virtual twin experiences, we can clearly define a new concept and virtually create and test a prototype to determine exactly how a ride will behave before physically building it,” said CEO Simone Bernardini. “Our simulations accurately recreate real conditions to support decision making.”
The largest class of boats to compete in the grueling Transat Jacques Vabre yachting race are the 32-meter long trimarans, which reach speeds high enough to allow the boat to literally fly over the surface of the water. In its debut race, the SVR-LAZARTIGUE, built by MerConcept, came in second place. To improve the aerodynamics, MerConcept used the 3DEXPERIENCE platform to build a virtual twin of the SVR-LAZARTIGUE and its systems, allowing the team to design and test the boat in limitless scenarios, to anticipate its behavior at sea better.
To design a boat like SVR-LAZARTIGUE takes about 150,000 hours of work, with more than 150 external collaborations happening around the world, explained Thomas Normand, CEO of MerConcept. The 3DEXPERIENCE platform provides a common data environment, where everyone can work together on the same model, from design phase, through construction and testing, ensuring technical modifications are correctly implemented and everyone can see what has been done.
“The virtual twin allows all relevant stakeholders to access the current model in real time and focus on the part or the system that interests them,” Normand said.
The virtual twin is also used to manage the boat through its lifecycle and make improvements based on data collected through tests and races. The fact that it is cloud-based, has been crucial for collecting and retrieving data when the boat is at sea.
“Thanks to the cloud, we are able to connect from anywhere with an internet connection,” said Antoine Gautier, design office manager at MerConcept. “When we’re on the water, we can access the 3DEXPERIENCE platform and see the boat’s plans and 3D model – critical if we experience any damage or otherwise. We can read the plans and try to understand in more detail what has happened. Thanks to this system, we can bridge the gap between virtual and reality.”
Failure may be part of the process of innovation, but it is only a blip in the big picture. Using the 3DEXPERIENCE platform to simultaneously create and test a new product is a practical way to reframe failure as an opportunity to learn and grow. As Walt Disney, Thomas Edison and Henry Ford knew, failure is just a steppingstone toward future success.