加速する製造現場のデジタル化の最前線で、変革者である企業のリーダーや製造現場の方々と、歩みを共にする弊社のメンバーだからこそ知っている、変革の舞台裏、成功事例集の行間に隠されたストーリーを垣間見る本連載。第四回目も前回、前々回に引き続き、製造DXの”目的”についてのお話です。今回は”QCD”のうち”D”、つまり納期管理と生産計画に関するDXのお話をさせていただきます。なお、過去の連載分もご覧になってみてください。
世界が目指した日本の生産システム
「海外は性悪説、日本は性善説」
ある大学の教授はこのように表現していましたが、日本と海外の生産システムでは、根本的な性格の違いがあると言われています。ジョブ型雇用で、転職ありきでキャリアを築くことが前提にある海外においては、SOW(労働契約書)で明確に定義された各自の業務をいかに怠けず、不正なく実行させるかが重要になってくる。そのためには全てを可視化し、管理者も現場の作業員に対しても、明確なプロセスを定義、強制することで、統制を取るというのが、海外企業における企業マネジメントシステムの主な考え方であり、その代表となるシステムがERPだという話があります。一方、日本企業はと言うと、従業員には「頑張り」を期待し、担当外の領域で困っている同僚がいれば「持ちつ持たれつ」の精神で支え合い、「チームワークで乗り切ろう!」、そんな企業が多いのではないでしょうか。そのような文化によって、今日のようにITシステムが普及するよりずっと前から、日本の製造現場は驚くほど効率的に回っていたと言われています。
日本の製造業が一つのピークを迎えたと言われる1970~1980年代。当時の日本が、「高品質で低価格」という圧倒的な競争力をもって世界の市場を席巻したこと。当時競争相手だった欧米の経済大国からも、「日本に学べ」「ジャパン・アズ・ナンバーワン」と言われるまでになったこと。こういった歴史は、今でも経済評論家やワイドショーのコメンテーターによって頻繁にメディアで語られ続けるため、当時を知らない就職氷河期世代の筆者にとっても馴染みがあります。
岐路に立たされる日本:納期や生産計画に関するDXが必要になっているのはなぜか?
現在の日本対アジアの新興国との競争に目を向けてみると、1970~1980年代の日本対欧米諸国と似たような構図になっているようにも見えることがあります。品質においては今でも「ナンバーワン」ですが、家電製品などにおいては新興国の製品も「問題ない」という認知が広がっているようにも思えます。また、品質よりもスピード感に重きを置き、次々とアジャイルに新しいものを生もうとする新興国の企業のスタンスは、製品のライフサイクルが短い現代の市場において、利するところがあるようにも思えます。その上新興国の国々は、安価な人件費を武器に価格競争に持ち込むことも出来るのですから、少品種・大量生産の市場はに日本の活路は見いだせないのかもしれません。そんな中で日本企業が10年先、20年先まで持続的に収益を確保していこうとすると、より付加価値が高い市場に主戦場を移さざるを得なくなります。付加価値の高い市場とは、半導体や、その製造装置に代表されるような製品のライフサイクルが短い市場や、マスカスタマイゼーションのような多品種大量生産の市場、より個別性の高い多品種少量生産品の市場、インテグラル型製品のような仕様の不確実性が高い製品の市場などが挙げられます。
製品のライフサイクルが短縮し、不慣れな新製品を頻繁にラインに流すようになると、長年作り続けている製品のように高精度な計画を立てるのは難しくなります。また、一工場あたりの生産品目が増えるほど、立案する計画数と変動要因は増えます。一品一葉の受注設計品は、業務フローそのものの定義も難しいです。それに、技術的な難易度が高い製品や仕様が曖昧な製品には経験則を利かせづらいですし、そのような引き合いの場合細かな変更も多く、時間見積もりが困難なことも少なくありません。加えてグローバル化が進み、国を跨いで複雑に物が行き来するようになったことで、物流のルート最適化も以前より格段に難しくなりました。これほどまでに複雑化した生産システムにおいて、どこをどう変えれば、正確に現場を把握し、精緻な計画を立て、無理のない納期を設定できるようになるのでしょうか。ここからは、現場の生の声から、納期や生産計画に関するDXを考えていきたいと思います。
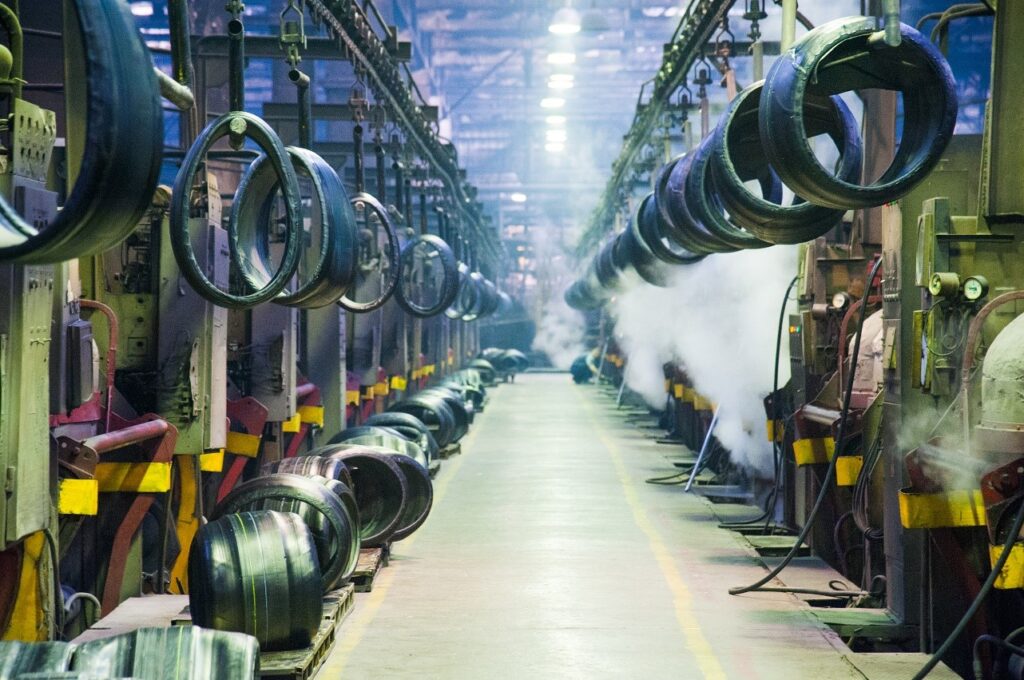
DXの目的①:素早く柔軟に、計画を変更できるようにする
「うちの生産計画の担当者が、日々の計画業務に取り掛かれるのは午後になってから。午前中はというと、工場内を歩き回って、数百という品種の在庫を一つ一つ確かめて回っている」
大手のタイヤメーカーでこれをお聞きした時は、とても驚かされました。
増え続ける品数に比例して、機械の故障や人的リソースの増減など、変動要因は増える一方ですし、顧客からのオーダーやオーダー変更も次々とシステム上を流れてきます。そのような環境で大切なのは、計画や納期を素早く柔軟に計算し直せることで、そのためにはリアルタイム性の高い新鮮な在庫データを、いつでも瞬時に確かめられるようにすることです。世界でも指折りの大手メーカーが、ここへ来てあらためて、このような基本的な部分に改革のメスを入れようとしていることの真意をつかみきれなかったのです。
その後お話を伺っていくと、当然きちんとした在庫管理システムはお持ちで、決まったプロセスで正確に在庫状況が入力・管理されていました。しかし、システムで確認できるのは倉庫にある完成品の在庫のみで、各工程脇のストックヤードにある中間品の在庫情報までは、取ることができていなかったのです。受注した製品のパーツや中間品のコンポーネントが今、どこに、いくつあり、あと何日でそれらが仕上がるのか、そういったことがさっぱり分からない。だから計画担当者が「ここにはこの段階の在庫がいくつあるのか、よしよし!」と、一か所ずつメモを取りながら工場内を歩き回るのが長年の習わしになってしまっていると・・・・・・。ここにこそ、改革のチャンスがあったのでした。
DXの目的②:計画を明文化し、より正確に納期を予測・回答できるようにする
業界問わず、この手の話は頻繁にお聞きするようになりました。とある重機械メーカーでは、先述したような多品種生産の時代が訪れる以前から、量産品の世界とは比べ物にならないほどの製品バリュエーションがあり、一度しか作らないような受注設計品がラインに流れる機会も少なくありませんでした。そんな中で作業時間を計測しようと、カイゼンの担当者がストップウォッチを持って1日現場に張り込んでも、その日にラインを流れたものの時間しか計ることができません。そうなると、厳密な工数や作業時間を見積もることもできません。その結果、工程を設計する人たちは、これまでの経験則をもとに10分とか20分という大雑把な目標タクトタイムを導き出して、あとは現場に頼み込んで頑張ってもらっていたそうです。ひとつひとつの工程が大雑把だと、計画や、顧客に回答する納期もどんぶり勘定にならざるを得ず、「最後は人が何とかするしかない」生産システムの典型的な状態になっていたと言います。そういった中で、顧客からの要求は年々パーソナル化が進み、更にIoTの潮流から製品に占めるソフトウェアの割合が増えたことで、仕様も曖昧になりつつありました。ようやく決めたはずの仕様に「ちょっと待った」が入ることも増え、引き渡し期日ぎりぎりになって初めて、「ダメです、間に合いません」という羽目になり・・・。「さすがに何とかせねば」という空気が生まれたそうです。
このメーカーにとってのDXの目的は、納期を正確に回答し、ヘルシーな生産活動をできる状態にすることであって、そのためには「計画が明文化されていること」が大事でした。工程表に記載された作業の一つ一つについて、今まではどんぶり勘定になっていたStandard Time(=標準作業時間)を精緻に定義し、新規品を含む全ての引き合いに対して、現実的な計画を策定出来るようにする。そのために、まずラインを流れるすべての製品バリュエーションの、すべての工程において、網羅的かつ正確性高く実績を取る必要がありました(その方法については、本ブログのPart.1をご参照ください)。そして、実績データをデジタルな環境に貯めて、過去の実績データを瞬時に出したり、データを分析したりして今後の計画に活かせるようにし、ゆくゆくは真新しい仕様の引き合いが来ても、過去にラインを流れた類似の仕様や要素技術のタクトタイムを参考に、今までよりも正確に作業時間を計算できるようにする。そういった世界を目指して、この重機械メーカーのDX推進が始まりました。
改革は一筋縄にはいかない
さて、こうして勢いよく始まった2社のDXですが、イノベーションの現場では、日々多くの壁があるようです。納期の話一つを取って見ても、納期通りに確実に物を作り切るために、常に十分な部材を持っておきたい製造部門と、少しでも安く買うために、まとめて沢山の部材を調達してしまいたい購買部門の間には、意識の乖離が。そこに、キャッシュフローと在庫のバランスを見ながら安全在庫をジャストインタイムで届けてほしい計画部門が加わると、時に三つ巴のような構図になることもあります。それぞれが性善説に立って積み重ねてきた知恵の塊やこだわりのようなものがある中で、横断的な視点での最適化を進めようすると、時には彼らの「より良くしたい」という想いの積み重ねを、否定せざるを得ない場面にも出くわします。
一筋縄にはいかない製造DXプロジェクトのイノベーターは、このような壁とどのように向き合っているのでしょうか。第5回目となる次回は、改革の舞台裏に迫っていきたいと思います。
このブログに関するお問合せはコチラ
ダッソー・システムズ株式会社 マーケティング Japan.Marketing@3ds.com