加速する製造現場のデジタル化の最前線で、変革者である企業のリーダーや、製造現場の方々。そんな方々と歩みを共にする弊社のメンバーだからこそ知っている、変革の舞台裏、成功事例の行間に隠されたストーリーを垣間見る本連載。第二回目は、製造DXの目的をどこに置くか、その一つとして”QCD”の”C”、つまりコストに関するお話をさせていただきます。なお、第一回目がまだ、という方は、【連載:製造DXー成功事例の舞台裏】Part.1 製造DXにおける、実績データの重要性も、ご覧になってみてください。
前回、製造DXの足枷となっている”固い組織の壁”を溶かすうえで、重要となる製造データのとり方や、そのデータを用いることで生産性が向上する、という話をさせていただきました。「この工程のタクトタイムが何分か」とか、「不具合のタイミングと件数の遷移はどうか」とか、「それに伴う手戻りの工数がどのくらいだったか」といった情報を普段から計測し、データとして貯めてリスト化する。そのために各工程の業務において、作業者自身が作業開始時に”着工”のボタンを押して、作業が終わったら”完了”のボタンを押す。不具合が起きたらそれを入力する。このひと手間で、実績データを自動的に出せるようになると、現場の管理者がシステム上で、日ごとの稼働率や何種類ものKPIを見比べて、編成効率をより良くしたり、作業負荷の山崩しをしたりという横串のカイゼンができるようになり、生産性が上がっていく。前回はそういった話をさせていただきました。しかしながら、そう簡単にことは進むのでしょうか。
目的がはっきりしていないと、現場は動かない
以前、とあるメーカーとのプロジェクトにおいて、工場のどこにボトルネックがあり、どこからプロジェクトをスタートすべきかというアタリをつけるため、いくつかの工場に足を運んだときのことです。そのうちひとつの工場からなかなかデータが出てこなかったので、何度かお願いをし、しばらく待つことになりました。するとやっと出てきたのが、作業時間や品質の記録に関する、大量の手書きメモの山でした。このメーカーでは、現場の情報をデータとして取っているはずだったのですが、色々と話を聞いてみると、「使う予定のないデータをひたすら取っているだけ」だというのです。管理する側が「データを取ることが仕事」になってしまっており、使われていないどころか、いざ使おうとしてもデータが読めないというありさまだったのです。それならば、データなど取らなくても回っているのだから、わざわざモニターを見に行って、デジタルデバイスにデータを打ち込むという、ものを作る作業に直結しない作業に手間暇かける必要なんてない。残念なことに、そういうスタンスになってしまっていたのです。
まずは工程を作る側の人たちが意味を理解し、丁寧に説明して、実際にデータを活用すること
今までは壁に貼ってある紙に鉛筆でぴぴっとチェックを入れるだけで済んだのに、わざわざモニターを見に行って、デジタルデバイスにデータを打ち込むというひと手間に、アレルギーを持つ方は少なからずいるようです。管理する側が作業時間をストップウォッチで計る代わりに、「毎回”着工”と“完了”を入力してください」と言ったら、「現場からものすごい反発されました」というエピソードを聞いたこともあります。「俺たちはこんなに忙しいのに、何を言ってるんだ!?」と。
その一方で、日本の工場の方々は、しっかりと作られた手順書をもとに丁寧に説明をすれば、それをルーティンワークにし、定着させてくれるという特徴もあります。面倒な手順、複雑な工程であっても、漏れなく、寸分の狂いなく遂行する、そんな”匠のDNA”が、日本の工場には受け継がれているのだと思います。ですから、工程を作る人が、その入力作業の意味をしっかりと理解し、丁寧に説明できれば良いのです。先述の「データを取っているだけで、使われていないというのが現場にバレてしまった」という話も、工程を作る側の人たちが作業者に対して、「皆さんがボタンを押すことで取っているこのデータは、本当に使うんです。無駄じゃないんです!」という理解を促すことができ、それがルーティンになれば、ゆくゆくは大きな生産性向上につながっていたかもしれません。では、こういったことをうまく推進できている企業では、現場のデータ入力やその活動に、どんな意味を持たせているのでしょうか。
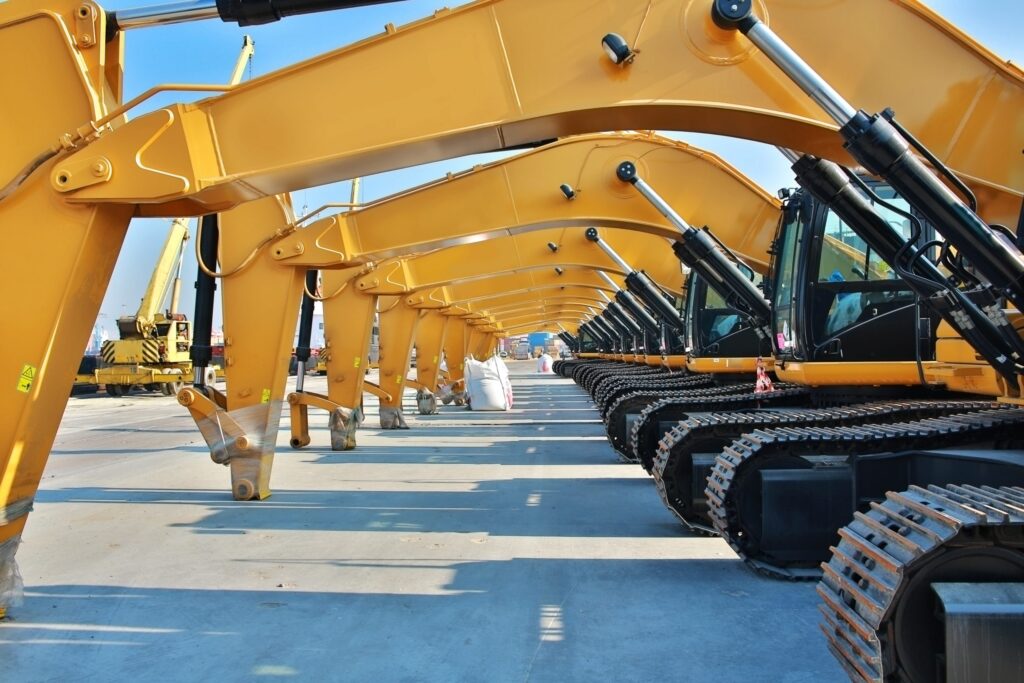
誰にでも理解でき、共感しやすいシンプルな目的がデジタル化を成功に導く
ここでひとつ、面白い話があります。ボタンの入力という現場の手間や、デジタル化という変化への反発などという様々な不満をすっ飛ばして、”予実管理”という切り口で製造DXを推進した企業の話です。こう聞くだけで、この取り組みが間違いなくキャッシュフローに直結することがわかります。読んで字のごとく、”予算(予定)”と”実績(実際)”をきちんと突き合わせて”管理”をおこなうという、至極シンプルな話なのですが、この「”実”がきちんと”予”のとおりになっているのか」というのに加えて、「もし仮に”予”のとおりにならなかった時に、その理由がわかっていることが大切」なのであって、デジタル化という変革の目的そのものを、それらが「わかるための努力」だと位置づけたのです。
つまり、今までは「なぜ予定より2台足りないんだ?」となると、「営業が緩い注文を取ってきたせいで、現場が逼迫したからです」などという話で終わってしまっていた議論を、定量的なデータをもって「どこを詰めていたら予定どおりになったのか?」とか、「どこを工夫したら予定どおりできたのか?」という議論に変えたいという目的です。生産ラインを分割して、より細かい単位で予実を管理していき、”予”の通りにできている部分とできていないところをはっきりさせ、できていない工程を分析していく。そうすることで、「この工程はナットランナーが悪かった」とか、「ここは設計が緩かった」とか、中には「最近新しい作業者が入ってきたため、一時的にパフォーマンスが下がっているだけだから、きちんと育成すればよい」とか、具体的な対策ができるようになり、工場全体のあるべき姿が見えてくるのです。
予実管理ができるようになると、今度はより細かい単位で積み上げ計算ができるようになってきます。たとえば、「製品タイプAは100の工程を経ることで完成するが、製品タイプBの場合はAにはない10の工程が加わる」とか、「製品タイプCには、この前の工程が抜ける」とか。各工程は個別に予実管理されているため、段々製品タイプごとにかかる製造コストがわかってくるのです。すると次に、見積が出来るようになってきます。「○○工場に、この時期に、Aタイプの注文が入ったら、いくらで作ることができるのか」という精度が上がってくるのです。こういったことができるのなら、やり方はなんでもよかったのですが、今のところ最も良い術が製造DXであり、それを正確性高く実現できる道具が、先ほどの”着工”や”完了”を人手で入力していく、MESソリューションだったという話です。この例で、変化をもたらすためには、組織全体が理解し、共感できる、シンプルな発想が大切だというのがわかっていただけたのではないでしょうか。
日本の製造DXは徐々に加速する
数年前までは、組織の上層部が鶴の一声で始めたために、よくわからずに製造DXのプロジェクトをやっているという状況に出くわすことがありました。また、「データなんか取らなくても、ちゃんとものは作れているんだ!」と、今までのやり方を変えようとすることに対する強い反発を目にしたことも多々あります。しかし最近は、時代の変化を感じる機会が増えています。今週、来週やらなければいけない目先の仕事を着実にこなしながらも、各自の守備範囲を超えて、将来会社がどうなるのかを考えている人。競合のメーカーがどんな取り組みをしているかとか、ほかの業界ではどんなことをしているのか気にかけている人。生まれ持ってデジタルという武器を持って日本を追いかけ、追い抜いてしまう新興国の企業を気にする人。中には「デジタル化なくして会社に未来はない」というくらい大胆にデジタル化を推進しようとする人もいたりします。こういった先見の明のある多くの方々が、それぞれの企業に合った旗を掲げ、力強く改革を推進する姿を目にするたびに、その行方に期待せずにはいられません。
さて、今回は製造DXを推進するために重要な目的設定、その一つとして、コストを目的においたお話をさせていただきました。次回も引き続き、目的の設定について、今度は”QCD”の”Q”、つまり品質についてお話できればと思います。
このブログに関するお問合せはコチラ
ダッソー・システムズ株式会社 マーケティング Japan.Marketing@3ds.com
関連リンク