Virtual Commissioning (VC) is the practice of using virtual technology to assist with the commissioning of complex manufacturing equipment, automation systems and control software. Virtual Commissioning has been in use for more than 10 years, emerging from the digital manufacturing efforts in several industries. However, due to the lower digital maturity in Life Sciences manufacturing, this is still an emerging field for innovation. VC has been recognized as a potential game changer in the Life Sciences industry, delivered through the emergence of the Virtual Twin, which we will describe later in this article.
In VC, virtual 3D models are developed to realistically and accurately simulate every aspect of any potential operation of manufacturing production and management software systems prior to their physical implementation. Various aspects of the electrical, mechanical and software control systems are simulated in this virtual environment, making sure that all, including the kinematic and static equipment components are synchronized and will function together optimally once the entire system is deployed.
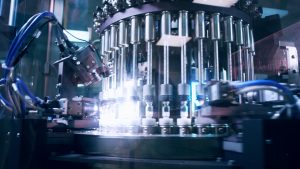
For such complex systems, especially in the highly regulated Life Sciences industry, traditional commissioning processes require teams from all engineering disciplines to work together in a staged, sequential and often iterative process to iron out problems and bugs- obviously time and resource intensive. VC significantly reduces the time and cost required for physical commissioning and therefore shortens the time and cost of system launch and time-to-market. Being able to simulate the final configuration also allows optimization of the process to reduce cost – both in financial and environmental terms.
Advantages of Virtual Commissioning
- Performed without interrupting production, preventing equipment and personnel downtime
- Ability to identify and resolve issues and bugs upfront and virtually, incurring significantly less effort to fix
- Exploration of what-if scenarios and testing of various design options before deciding on the best solution
- Can be used for effective training without the need for time on physical equipment
- Significant risk reduction after system go-live
Evolution of Virtual Commissioning with Virtual Twins
While Virtual Commissioning has been an established practice for years in a variety of industries, even more gains are now possible when it is combined with Virtual Twins. Originally introduced in 2002 by Dr. Michael Grieves as a virtual representation of a physical product, the Virtual Twin concept has grown in definition and use cases. Virtual Twins model and describe any system under development. The Virtual Twin is refined by data captured from sensors in existing operational systems, increasingly in real-time and thus, not only creates an accurate dynamic representation of corresponding engineering objects and processes, but is also dynamic and responsive to changes within itself. Virtual Twins can be used to simulate an entire system as it is operated, allowing real-time monitoring and virtual testing of modifications. This capability facilitates the application of actionable analytics which can in turn enable and test optimization strategies anywhere in the production system and at any phase of the manufacturing process.
Read about use of Virtual Twins for personalized medicine: Top Tech Trends Fueling Advances in Life Sciences and Healthcare.
Virtual Twins: Evolution of Data Representation
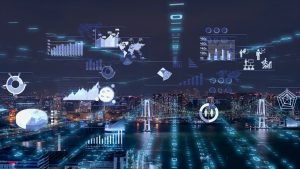
According to the Virtual Twins in Manufacturing 2021 Progress Report by Dassault Systèmes and IndustryWeek, digital transformation in manufacturing creates more data, including real time, and information than ever before. “The addition of virtual twins brings that data to life. It’s a 3D model of a plant and everything that’s within it. The modeling, simulation, and optimization reflect not only the physical behaviour of assets but how they are located in the wider context of the supply chain processes for producing goods.” Having this capability is important to help manufacturers evaluate and understand the impact of their strategic decisions. “The adoption of virtualization technologies will play a critical role in manufacturers’ ability to advance their Industry 4.0 goals of end-to-end visibility and flexible production.”
Virtual Commissioning in Life Sciences and Healthcare
According to a recent Dassault Systèmes eBook- The Virtual Twin Experience for BioPharmaceutical Manufacturing Commissioning, here is traditional commissioning by the numbers:
- The average time for the design and installation of a drug manufacturing production line in a good manufacturing practice (GMP) environment is 10 months
- 20% of a manufacturing line’s total delivery time is dedicated to mandatory commissioning activities
- 60% of commissioning time is spent fixing software errors
Virtual commissioning offers many real-life advantages to Life Sciences manufacturers, including:
- 40% reduction of commissioning time
- 15% reduction of total time-to-market
- 80% reduction of re-engineering deviation
- 40% risk reduction of test batch loss
- 25% reduction of full-time equivalent (FTE) resources
Additional Resources
- Watch Dassault Systèmes Line Virtual Commissioning webinar to understand how it helps Life Sciences companies to:
- See 6 Steps to Virtual Commissioning Infographic: Optimize your pharmaceutical plant systems with virtual simulation.