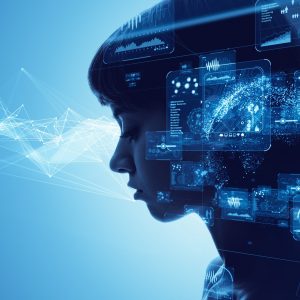
Keeping current with good pharma manufacturing practice is… well, a good practice. Unless you’re the United States Food and Drug Administration—then it’s the law. The FDA helps safeguard the quality of drug products by monitoring drug manufacturers’ compliance with its Current Good Manufacturing Practice (CGMP) regulations. The CGMP regs for drugs, contained in Title 21 of the Code of Federal Regulations (CFR), lay out minimum requirements for the methods, facilities, and controls used in manufacturing, processing, and packing of a drug product. The regulations help ensure that a product is safe for use, and that it has the ingredients and strength it claims to have.
The CGMP obligations cover a wide range of elements that impact manufacturing practice, including organization and personnel, buildings and facilities, equipment, control of components and drug product containers and closures, production and process controls, packaging and labeling controls, holding and distribution, laboratory controls, and returned and salvaged drug products.
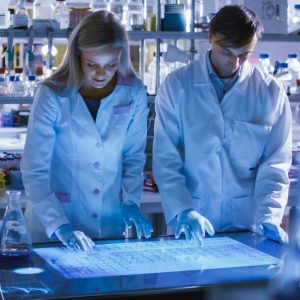
The regs drill down into each category that constitutes current good manufacturing practice. For example, Buildings and Facilities covers design and construction features, lighting, ventilation, plumbing, sewage and refuse, washing and toilet facilities, and sanitation and maintenance. Equipment focuses on design, size and location, construction, and cleaning and maintenance. Production and Process Controls include procedures and deviations, yield calculations, process materials, drug product sampling and testing, and control of microbiological contamination.
One of the most critical elements is Subpart J—Records and Reports. Its general requirements (Section 211.180) simply state that companies must maintain production, control or distribution records. More specific instructions detail requirements in areas like master production and control records, batch production control records, production record review, production and process controls, etc.
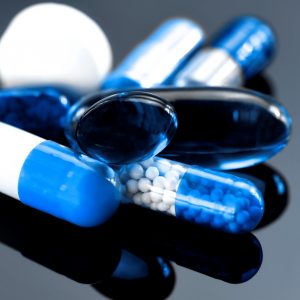
For example, Section 211.188 states that “Batch production and control records shall be prepared for each batch of drug product produced and shall include complete information relating to the production control of each batch.” This requires documenting each process step, dates, individual equipment and lines, in-process and laboratory control results, inspection packaging and labeling, actual yield as a percentage of theoretical yield, and so forth.
The CGMPs are flexible: each company decides which controls and technologies it will use to comply with regulations for quality management, process repeatability, and quickly retrievable documentation on each step of the production process. But one thing is certain—life sciences companies need digital solutions to make it work, including the foundation stone of a digital collaboration platform to snare all the data and manage the documents electronically to ensure conformance with the regulatory process.
For life sciences businesses seeking compliance and competitiveness, digital transformation of manufacturing practices can’t come fast enough. The “C” in CGMP stands for current, “requiring companies use technologies and systems that are up-to-date in order to comply with the regulations,” the FDA states. “Systems and equipment that may have been ‘top-of-the-line’ to prevent contamination, mix-ups and errors 10 or 20 years ago may be less than adequate by today’s standards.”