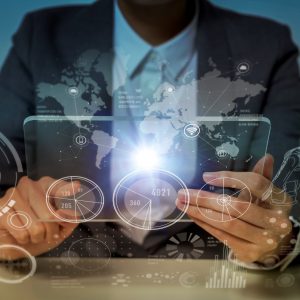
There is considerable buzz these days about the use of Digital Twin technology for manufacturing, especially for additive manufacturing software with 3D printing. By definition, a digital twin is the digital, virtual representation of a physical object. In nature twins are born at the same time, while in design one twin essentially begets the other. Early use of digital twins was to create the digital/virtual twin as a descriptive version of the existing physical object. Now the focus is shifting to modeling the complete product and all processes in the digital realm first, then use it as the basis for manufacturing.
This shift means the digital twin has advanced from being a description of the physical object to being the dynamic representation of every design intention, guiding how the object is made. The shape is digital, the materials are digital, the functions and stresses are digital. As industry increases its use of additive manufacturing, there is increased emphasis on the use of digital twins. The value of dynamic representation extends all the way to the 3D printer without being reduced to a drawing or service BOM software for manual review and execution.
Three design process tasks
Moving to digital twins is part of a larger story in manufacturing, of digital transformation. This transformation is an evolutionary, continuous process of adding digital competency to transform existing workflows and business models.
Leading product development researcher Dr. Michael Grieves (Florida Institute of Technology) is considered the father of the digital twin concept. Grieves has identified three common yet essential tasks that can be more successfully exploited with digital twin technology. He refers to them as the Three C’s: Conceptualization, Comparison, and Collaboration. How products are conceptualized, how design ideas are compared, and how design teams collaborate will all need to be re-examined and reinterpreted as part of digital transformation.
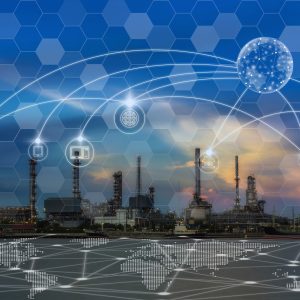
Conceptualization is the act of forming and interpreting a concept. Humans don’t process data line by line the way computers interpret software, we put information into a meaningful context. This is why we use drafting and modeling instead of lists. The CAD model improves the ability to conceptualize the geometry of a product, while the digital twin improves the ability to conceptualize all aspects of the product. It brings an immediacy of understanding to both form and process, and allows for rapid group assimilation of product information. Dr. Grieves notes, “With the digital twin to build a common perspective, we can directly see both the physical product information and the virtual product information, simultaneously.”
Comparison is a powerful intellectual tool. If the only way to evaluate a product is to create a physical prototype, engineers then have to test, measure, record the data, and manually compare with design specifications. Dr. Grieves says a digital twin model means engineers can “view the ideal characteristic, [and] the tolerance corridor around that ideal measurement.” When the digital twin use is extended into manufacturing, comparing production with the digital twin becomes an automated process.
Conceptualization and comparison can be seen as solo activities. Collaboration amplifies the two within the work group for the greater good of manufacturing. “The most powerful thing that humans do is collaborate with each other,” notes Dr. Grieves, “in order to bring more intelligence, more variability of perspectives, and better problem solving and innovation to situations.”
Collaboration doesn’t exist only in the engineering department and the factory floor. Using a digital twin with supply chain partners enables a product-centric view. Dr. Grieves notes that sharing information digitally improves communication: “Information is highly granular, meaning we do not need to share all or nothing like we do with physical things; we can share specific pieces of information with suppliers so that they can do their tasks more efficiently and effectively.”
Dr. Grieves believes the highest value of digital twins lies in their ability to replace the physical resources of time, energy, and material with information. “Since we live in a capitalist society, we translate the physical resources of time, energy, and material into monetary cost.” Eliminate the need for physical examination of time, energy, and material by making it digital, and total engineering and manufacturing costs are reduced.
Editor’s Note: Discover more about digital transformation in manufacturing and how this powers The Factory of the Future.