Electric vehicles (EVs) offer a quiet, economical way to travel without polluting the planet. Over the vehicle’s life, EVs are also much more sustainable than traditional gas-powered vehicles. But focus on how the cars are manufactured and the sustainability picture becomes more complex.
An EV contains five times the amount of minerals of a traditional gas-powered vehicle, including copper, lithium, cobalt and various rare earth metals. These minerals are the critical building blocks for EVs and other clean energy technologies, which are vital in achieving global sustainability goals. And, as the world races to meet its net zero targets, demand for these minerals is soaring. By 2050, for instance, the World Bank predicts that production of graphite, lithium and cobalt will increase by 500% – purely to meet the demand for clean energy technologies.
This is not the first time we’ve seen surging demand for metals and minerals. In the past, factors ranging from the Industrial Revolution to global conflicts, technological innovation or population growth have escalated demand. Responses have included exploration and innovation to find new supply sources, and recycling or using substitute materials to help make up for any shortages. But today, several factors are making the problem more complex.
For a start, there is no shortage of minerals in the ground – but the quality of the ore is declining as high-quality deposits have already been depleted. It takes more energy and water to extract the minerals from lower-grade ores, which ramps up CO2 emissions. And because there is less metal in the rock, getting it out creates more waste.
For the environment and populations around mine sites, soil erosion, sinkholes, pollution, loss of biodiversity and water stress caused by mining activities can have a devastating impact. Because deposits for some minerals, like cobalt, are concentrated in just one or two countries, mining companies are forced to extract in these locations, regardless of the costs they may come with.
For mining companies, the challenge is not only to deliver the materials that EV manufacturers need. They also must find sustainable ways to produce those materials. After all, an EV’s sustainability credentials will not stand up to scrutiny if dirty or harmful processes were used to make it.
Sustainable mining in the spotlight
Calls for more sustainable mining are well established. Global agencies including the United Nations (UN), World Bank and International Council on Mining and Metals have consistently highlighted the industry’s importance in achieving the UN’s Sustainable Development Goals. And investors are putting well publicized pressure on mining firms to adopt stringent sustainability policies. But the rapidly growing EV industry brings those issues closer to home.
Transitioning to EVs is a major part of many governments’ net zero targets, and regulations are emerging that recognize the close relationship between the EV and mining industries. The US Inflation Reduction Act, for instance, specifies that to qualify for EV tax credits, 40% of the value of critical minerals used in an EV must be extracted, processed and/or recycled either domestically or in a country that has a free trade agreement with the US.
But perhaps the loudest calls for sustainable mining – and the most difficult to satisfy – are coming from consumers. They are the ones buying the EVs, and their decisions to purchase are increasingly driven by sustainability issues. In developed and developing economies alike, consumers are putting their money behind cleaner, greener products and supply chains.
But they’re also wary about greenwashing. And since many people even within the mining industry itself still see it as a dirty, dangerous industry, convincing consumers that things have changed for the better represents a significant challenge.
In addition to finding sustainable ways to meet growing demand, mining companies must be able to demonstrate to different stakeholders how they are doing so. There are several steps they can take to meet both those requirements.
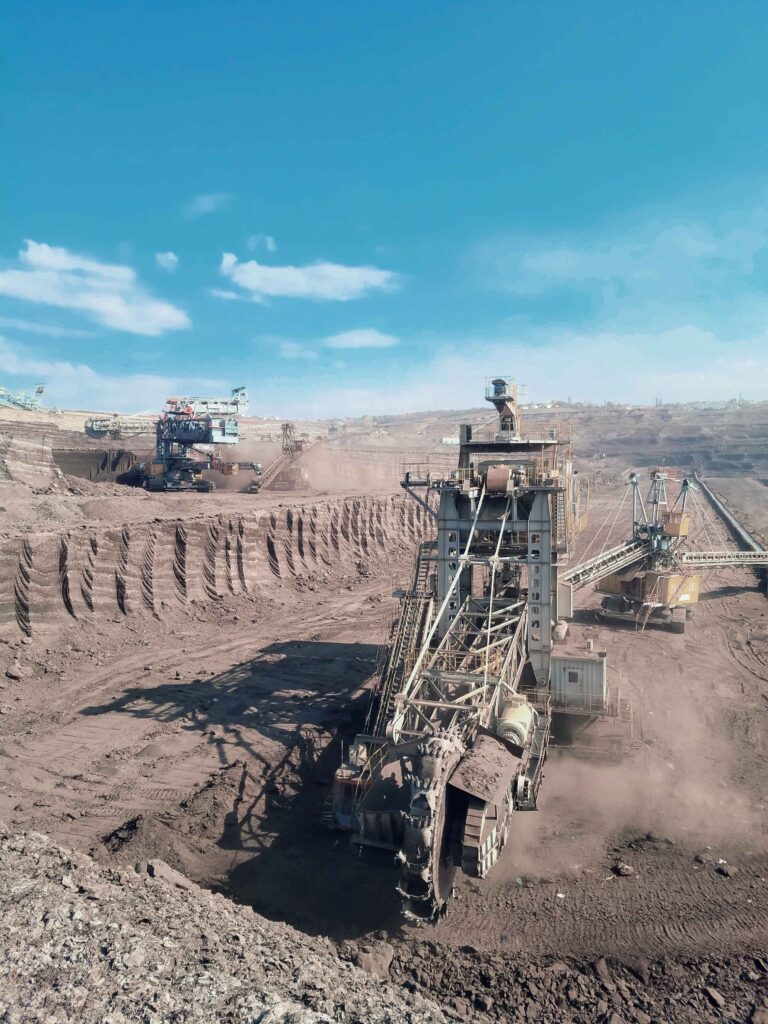
How is mining meeting the sustainability challenge?
Sticking with old methods is not an option if mining organizations are to feed a hungry EV industry. Companies are already looking for new ways to sustainably boost and accelerate production. One way to approach this is to look at mining productivity through sustainability-focused lenses. Dassault Systèmes, for example, works closely with mine operators with a focus on three key areas:
- “Waste-less” mining – shifting away from practices like bulk ore excavation, which depletes the earth and generates tons of waste as precious minerals are separated from their host material
- “Water-less” mining – using innovative processes to eliminate water waste and stress
- “People-less” mining – automating labor-intensive processes using software, robots and autonomous vehicles to boost efficiency, improve safety and enable people to focus on high value tasks
Precision mining is one approach that can boost productivity and sustainability while reducing waste. Just like laparoscopic surgery in humans, it avoids creating unnecessarily large holes and uses precisely targeted incisions instead.
In terms of sustainability, precision mining promises impressive gains. Precision drilling is much less disruptive to the earth and creates less waste. In copper mining, for instance, conventional methods involve extracting the solid ore and then crushing the metal out of it – and more than 99% of that crushed rock is waste. Recovering the metal without digging up the rock avoids almost all that waste. Doing so also minimizes damage to the surrounding geology.
In addition, precision mining offers a much safer way to operate because the underground part of the operation is people-less. All the equipment stays on the surface where employees can operate it from the safety of a cab. Add in automated processes that eliminate repetitive tasks and reduce errors and injuries, and you have an operation that leaves humans free to innovate and validate while technology does the heavy lifting.
Unsurprisingly, this method of mining also uses less water than traditional options, making it an all-around attractive technique for companies looking to extract minerals sustainably. However, it’s not the only way to achieve the goal of using – and wasting – less water.
Water-less mining is a significant focus of industry research, with companies looking at how they can develop mining methods that do not cause water stress. Companies are looking at closed-loop water recycling systems, for example, and close monitoring of evaporation rates. Innovative new processes and technologies which use less water to extract, separate and process ore are also in the pipeline. In lithium mining alone, traditional methods use around 500,000 gallons of water for every metric ton produced, so measures like these, along with accurate measurement and reporting, can have a huge sustainability impact.
Planning to support industry, people and planet
Precise, intricate planning is essential to meet the EV industry’s growing demand for sustainable minerals. As well as finding profitable ways to operate and adhering to industry regulations, mining firms must also honor an informal social contract with their surrounding communities and other stakeholders – known as a “green” or “social” license to operate. The use of both “green” and “social” to describe that license underlines the fact that truly sustainable mining must include social, as well as environmental, responsibility. And those concerns must be part of the mine’s DNA. Now, more than ever, environment, social and governance (ESG) tenets are at the heart of mine planning and operation.
To manage their sustainability journey, organizations need the ability to locate ores, analyze the materials surrounding them and devise the most sustainable way to extract them in the volumes the EV industry needs. Increasingly, they are using advanced technology to model every aspect of the mine’s operation, from concept to closure, measuring every emission and key performance indicator along the way. Crucially, those same tools allow them to demonstrate their processes to regulators, investors and communities.
At one gold and silver mining company, for instance, advanced modeling and simulation tools are helping to create accurate and detailed mine plans that factor in elements such as geology, topography and ore grades. The company can rapidly create mine designs using productivity and sustainability targets, while making sure everything aligns with schedules and available resources.
This approach, which uses virtual twin technology to create a real-time, working model of the whole operation, allows organizations to measure every facet of their ESG performance and run simulations to see how different scenarios will make a difference. It’s been widely adopted in industries like aerospace, life sciences and manufacturing – including EV makers. Now, the same technologies are being used to support geology modeling, mine design and tactical mine planning for the sustainable supply of minerals that are vital to the EV industry.
“Modeling a whole operation, from conception through to mine closure, is a big undertaking, but building a virtual twin of the mine provides so much capacity,” said Bradley Hay, worldwide VP of GEOVIA sales and services at Dassault Systèmes in a recent mining-focused LinkedIn Pulse interview. “From a governance standpoint, companies can understand much better how their operations impact ESG. They can better understand what is required from an investment perspective. And they can more effectively communicate their part in the shift towards renewables with the public. This empowers mining companies to better present, position and charm the industry and the investment community around what they’re doing.”
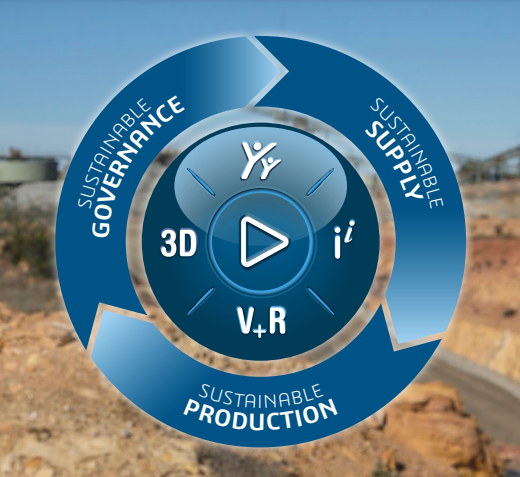
An environmentally and socially sound supply chain
Sustainable mining isn’t only about getting materials out of the ground. It’s about delivering the quantity of materials that EV manufacturers need in a way that will positively impact the vehicle’s sustainability footprint. That’s especially important for minerals like lithium – a key component of EV batteries that is not currently produced in the volumes this growing industry needs. And it’s leading to close collaboration between automakers and mine operators to ensure the supply chain is sustainable, resilient and transparent.
General Motors, for instance, has made several investments in lithium mining companies in return for exclusive access to supplies. BMW is also sourcing its own lithium for high-voltage batteries and making it available to its battery cell supply chains.
Meanwhile Tesla, which still retains significant EV market share despite growing competition, is shortening the journey from mining to manufacturing by sourcing a substantial chunk of its lithium, nickel and cobalt directly from mines. This arrangement means it can refine the materials on-site instead of shipping them elsewhere. Tesla’s direct relationship with miners serves its business needs by ensuring a supply of critical minerals for making batteries. In addition, it means the company can closely monitor quality and ensure environmentally and socially responsible sourcing.
“While cobalt, nickel, and lithium go through multiple processing steps by different companies, some of the more important environmental and social risks in this supply chain are present at mine sites,” Tesla explained in its 2022 Impact Report. “Direct sourcing from mining companies allows Tesla to engage directly in local contexts instead of having to rely on multiple midstream companies that typically sit between EV makers and mining. It also enables more transparent and traceable supply chains and better environmental and social data.”
Driving planet-smart practices
Through the EV revolution, the automotive and mining industries are driving closer together with sustainability in their headlights – and that is accelerating innovation. Leading mining organizations are collaborating to find ways to decarbonize their operations and create fully electrified, emissions-free mining. As well as adopting electric and autonomous vehicles and renewable energies, they’re creating opportunities for innovative mine designs alongside better health and environmental outcomes.
Alongside these mining innovations, the quest for more powerful, faster charging and cleaner EV batteries continues. Researchers are looking at how non-mined materials – derived from seawater, sand and even barley husk ash – might help to reduce reliance on mined minerals in the future. But while innovations like these may help to shape tomorrow’s mining practice, there is no doubt that the mining industry plays an essential role in delivering clean energy transportation options.
For mining firms, the sustainability commitment is not optional: firms that fail to engage meaningfully with the SDGs will deter investors and put their operations at risk. Meanwhile, those that develop more sustainable, productive processes will enhance their relationships with governments, investors and, crucially, consumers. As the EV revolution makes clear, sustainable mining is essential to our planet’s future. And technology can help to achieve it.