As the hydrogen economy gains momentum, companies involved in hydrogen production and distribution are increasingly turning to Virtual Twins to enhance their project execution, reduce risks, and speed up time-to-market. A Virtual Twin is a dynamic, integrated digital replica of a physical asset or system that allows engineers and decision-makers to simulate, analyze, and optimize processes in a comprehensive and risk-free environment. In the context of hydrogen projects, Virtual Twins offer a powerful tool for addressing the unique challenges of this emerging industry.
What is a Virtual Twin?
A Virtual Twin goes beyond the traditional concept of a digital twin. While a digital twin typically focuses on replicating the physical aspects of an asset, Dassault Systèmes’ Virtual Twin incorporates both the physical and non-physical elements, including the entire ecosystem surrounding the asset. This includes modeling capabilities, stakeholder networks, supplier relationships, and even market dynamics. The Virtual Twin is not just a 3D model; it is a fully integrated environment where all aspects of a project or operation can be simulated and optimized in real time.
By leveraging real-time data and advanced analytics in supply chain, Virtual Twins enable companies to monitor and manage their assets more effectively, predict potential issues, and make informed decisions that enhance project outcomes.
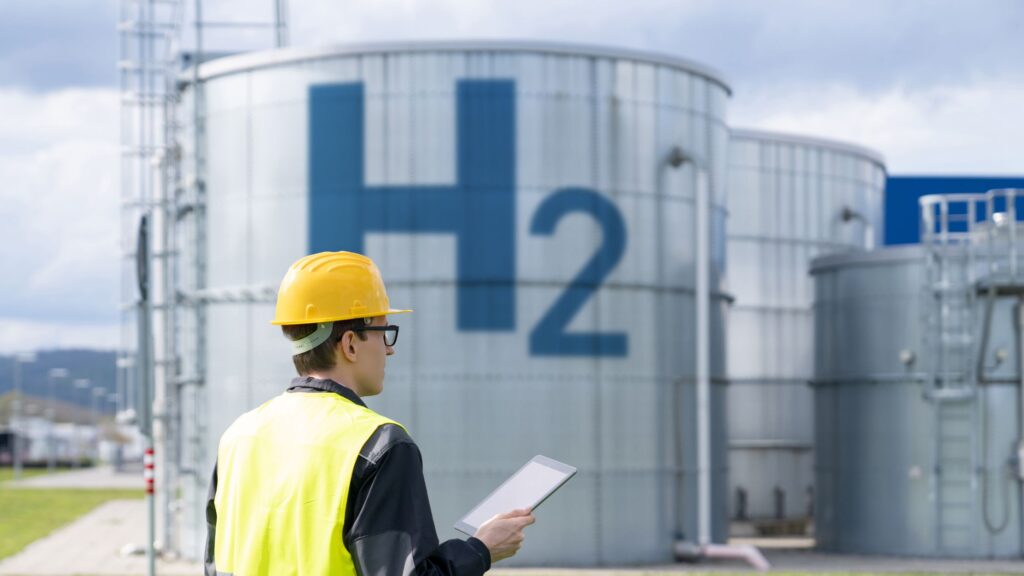
The Benefits of Virtual Twins in Hydrogen Projects
1. Risk Mitigation: Hydrogen projects involve complex systems with many interdependencies. Virtual Twins allow engineers to simulate various scenarios, assessing how changes in one system might impact others. This capability is crucial for identifying and mitigating risks before they become costly problems in the real world.
2. Optimized Design and Operation: Virtual Twins enable project teams to optimize the design and operation of hydrogen production facilities. By simulating different configurations and operational conditions, companies can identify the most efficient and cost-effective approaches to producing and storing hydrogen.
3. Enhanced Collaboration: Hydrogen projects typically involve multiple stakeholders, including suppliers, contractors, and regulatory bodies. Virtual Twins provide a common platform for collaboration, ensuring that all parties have access to the same data and insights. This transparency fosters better communication and decision-making throughout the project lifecycle.
4. Faster Time-to-Market: By using Virtual Twins to validate designs and optimize processes early in the project, companies can accelerate the development timeline. This agility is particularly important in the fast-paced hydrogen economy, where the ability to bring new projects online quickly can be a significant competitive advantage.
Real-World Applications of Virtual Twins in Hydrogen
Several companies are already leveraging Virtual Twins to drive success in the hydrogen space:
• Design Validation: Before breaking ground on a new hydrogen production facility, companies can use Virtual Twins to simulate the entire project. This allows them to validate design choices, optimize system configurations, and identify potential issues before construction begins.
• Operational Optimization: Once a hydrogen facility is operational, Virtual Twins can be used to monitor performance in real-time. By analyzing data from sensors and other sources, companies can identify inefficiencies, predict maintenance needs, and optimize production processes.
• Regulatory Compliance: Virtual Twins can also help companies navigate the complex regulatory landscape surrounding hydrogen projects. By simulating different compliance scenarios, companies can ensure that their projects meet all necessary requirements, reducing the risk of delays and fines.
What is next?
As the hydrogen economy continues to grow, the use of Virtual Twins will become increasingly important for companies looking to de-risk their investments and accelerate project delivery. By providing a comprehensive, data-driven view of hydrogen projects, Virtual Twins enable companies to make better decisions, optimize operations, and stay ahead of the competition. In a rapidly evolving industry, the ability to leverage Virtual Twins could be the key to long-term success.
Check more on https://www.3ds.com/industries/infrastructure-energy-materials/energy-transition/green-hydrogen-infrastructure
![]() Infrastructure, Energy & Materials Industry Business Value Consultant Expert, Dassault Systèmes |
Stefan Ceulemans joined Dassault Systèmes to lead the infrastructure, energy and materials industry solutions and technical teams before moving to his current role as an industry business value expert focusing on clean energy transformation. His industry experience is rooted in oil and gas through a wide variety of engineering and operational leadership roles. Sustainability has been a continuous point of focus and interest in his career, with successful leadership in energy efficiency programs. Over the last decade, Stefan Ceulemans has been an industry consultant, manager and director on the forefront of business development and customer engagement activities. He focuses on helping owner-operators leverage technology to improve project execution and controls, asset information management and other tactical and strategic initiatives, such as transitioning to a clean and sustainable energy economy. |