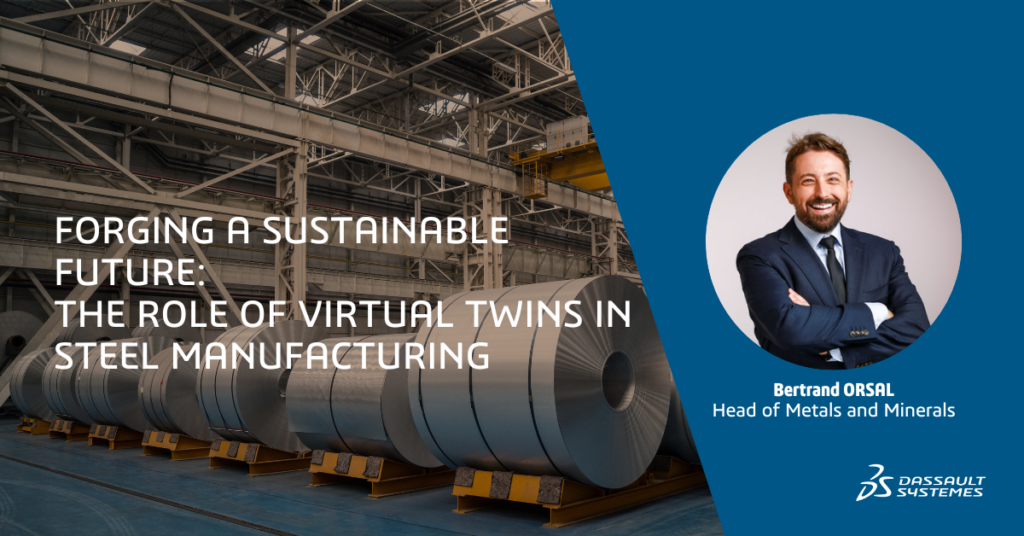
As the steel industry grapples with the pressing demands of decarbonization and sustainable practices, innovative technological solutions are paving the way for a transformative future. Among these advancements, virtual twins stand out as a game-changer, poised to accelerate the industry’s evolution toward greener operations. In this blog post, we explore the critical role of virtual twins in forging a sustainable future for the steel industry, based on insights from the Future Steel Forum 2024.
Embracing Digital Twins
Digital twins, a technology first conceptualized in the early 2000s, have now become integral to various industries, including steel manufacturing. By creating highly accurate digital models that represent real-world objects, systems, and processes, digital twins facilitate enhanced monitoring, analysis, and optimization. This sophisticated virtual environment allows for the testing and refining of scenarios, predicting outcomes, and implementing solutions in a risk-free manner.
The Four Dimensions of Digital Twins
The current advancements in digital twins incorporate 3D spatial dimensions and additional layers of predictive analytics, augmented by virtual and augmented reality (VR/AR). This multidimensional approach enables a comprehensive understanding of operations, making it particularly beneficial in sectors like steel manufacturing, where the complexity of processes demands precise and adaptable solutions.
Enhancing Predictive and Real-Time Capabilities
One of the significant advantages of digital twins is their ability to enhance predictive maintenance and operational efficiency. By using sensors and real-time data, these virtual models can anticipate equipment failures, optimize maintenance schedules, and reduce unplanned downtimes. This predictive prowess not only improves productivity but also extends the lifespan of critical assets, contributing to sustainability goals.
Real-World Applications in the Steel Industry
In the steel industry, digital twins are being implemented to address various challenges, from improving safety and operational efficiency to reducing environmental impact. For instance, Dassault Systèmes’ Steel manufacturing Control Tower software utilizes digital twins to monitor and manage steel production processes. By integrating real-time data and simulations, this system allows for proactive decision-making, minimizing waste, and optimizing resource use.
Collaboration and Innovation
The Future Steel Forum 2024 highlights the collaborative nature of digital twin technology. By enabling seamless communication and coordination among different stakeholders, virtual twins foster a more integrated and efficient production environment. This collaborative approach is crucial for tackling the multifaceted challenges of modern steel manufacturing, from energy consumption to emissions reduction.
A Sustainable Path Forward
As the United Nations calls for increased sustainability efforts, the steel industry must embrace innovative solutions like digital twins to achieve these goals. By leveraging the full capabilities of virtual models, steel producers can optimize operations, reduce carbon footprints, and improve overall efficiency. This transformation is not just about adopting new technologies but also about rethinking traditional practices and embracing a culture of continuous improvement.
The Future Steel Forum 2024 underscores the vital role of virtual twins in driving the steel industry’s sustainable transformation. As companies navigate the complexities of decarbonization and strive for operational excellence, digital twins offer a promising path forward. By harnessing the power of predictive analytics, real-time data, and collaborative innovation, the steel industry can forge a future that is both sustainable and resilient.
In conclusion, the integration of digital twins in steel manufacturing represents a significant leap toward achieving sustainability goals. As the industry continues to evolve, the role of virtual twins will undoubtedly become more pronounced, driving efficiency, reducing environmental impact, and ensuring a brighter future for steel production.