In the recent McKinsey report “Behind the mining productivity upswing: Technology-enabled transformation”, the firm looks at the progress the mining industry has made in improving productivity through the adoption of new capabilities such as automation. In Western Australia, for example, miners have achieved a 20% productivity improvement through autonomous haulage. However impressive the improvements from digital transformation in mining, there are still significant impediments to greater productivity benefits from being realized.
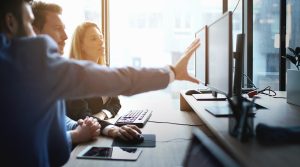
Overall in the industry, productivity rose between 2014 to 2016 by 2.8%, but much of it was achieved through labor productivity, headcount reduction, and tighter capital spending control. McKinsey argues that mining companies must embrace digital transformation if they are to gain more productivity improvements, especially in light of declining ore grades. In short, they outline that mining companies need to:
- Use technology and automation in all aspects of their business, including for productivity, supply chain management, safety, and customer satisfaction.
- Configure management systems and work processes to realize the full potential of new technology.
- Change the company culture to become more agile with the new technology.
Ultimately, to achieve digital transformation in mining industry, there must be a change in mindset, behavior and capability, says McKinsey. A new type of mining organization, enabled by change management must also evolve to underpin what they call the new digital organization. Old ways of doing things, where individual groups have responsibility for different functions like planning, production, maintenance, etc., must be replaced by a more holistic, collaborative way of thinking and working. Siloed teams result in slow, subpar decision-making: “Most importantly, teams that work in siloes know only what they know; they are isolated from the data that drives innovation.”
In outlining an approach mining companies can take to working in this new way, McKinsey posits that companies should organize workers into “squads” focused on different processes such as safety or leaching. Doing so, they argue, would result in more informed, more meaningful changes that occur faster.
Dassault Systèmes’ 3DEXPERIENCE platform provides the type of capabilities that McKinsey outlines. It connects people from different disciplines to the data they need to perform their jobs, and the collaborative capabilities they need to work together to solve problems faster and more effectively. It also offers the applications required for modeling, planning, and execution across the mining value chain, allowing for a holistic understanding of how well everything is performing. With this, and its simulation capabilities, workers can ideate and discover improvements to the processes they are responsible for, while seeing what the impacts will be.
An important aspect to underpin new ways of working is ensuring there is a governance process in place to allow for review oversight. With the 3DEXPERIENCE platform, governance enables new workflows to be adopted and the new ways of working they bring to become consistent. Workers will always know what the next step of a process is and how to engage with one another, including with those who need to review and approve deliverables.
Risk management is a key function of every mining enterprise whether it is geared toward ensuring safe operations, ensuring productivity, or profitability. With the 3DEXPERIENCE platform, problem identification, ideation how to solve issues, and tracking through to resolution is enabled through collaborative dashboards and workspaces. Workers, from executives to frontline workers have access to the data they need, in the form that they need it to track issues and the progress made to resolve them.
A VP of production, for example, can monitor operations target objectives and raise issues to be followed up on when output dips. There is a clear line of action downstream, a means to identify what the root causes are, collaborate on resolutions, and then implement them and track progress. For example, the production team may identify that a different approach to maintenance will improve production downtime, resulting in higher output. With the 3DEXPERINCE platform, they can simulate the production schedule changes, optimize changes and then rapidly deploy it to operators.
Together with new ways of working is the recognition that new skills must be brought into teams and veteran expertize tapped into more effectively. Whether its connecting to data scientists who will find new patterns in data or to engineers with decades of experience, a 3DEXPERIENCE platform approach to mining allows these scarce resources to support operations from anywhere in the world. By being able to work together using a single source of truth, and collaborative workspaces, problems can be shared and solutions to them found more readily.
To reap full productivity rewards, sustainable digital transformation in mining industry is required. Once silos have been broken, innovative approaches to addressing problems can be more readily found and then continuously improved upon. Having a platform in place that embeds transformation into a company’s culture and way of working is therefore key.
To learn more about Dassault Systèmes’ 3DEXPERIENCE platform and solutions for mining,
On the web: 3DS.com/natural-resources/