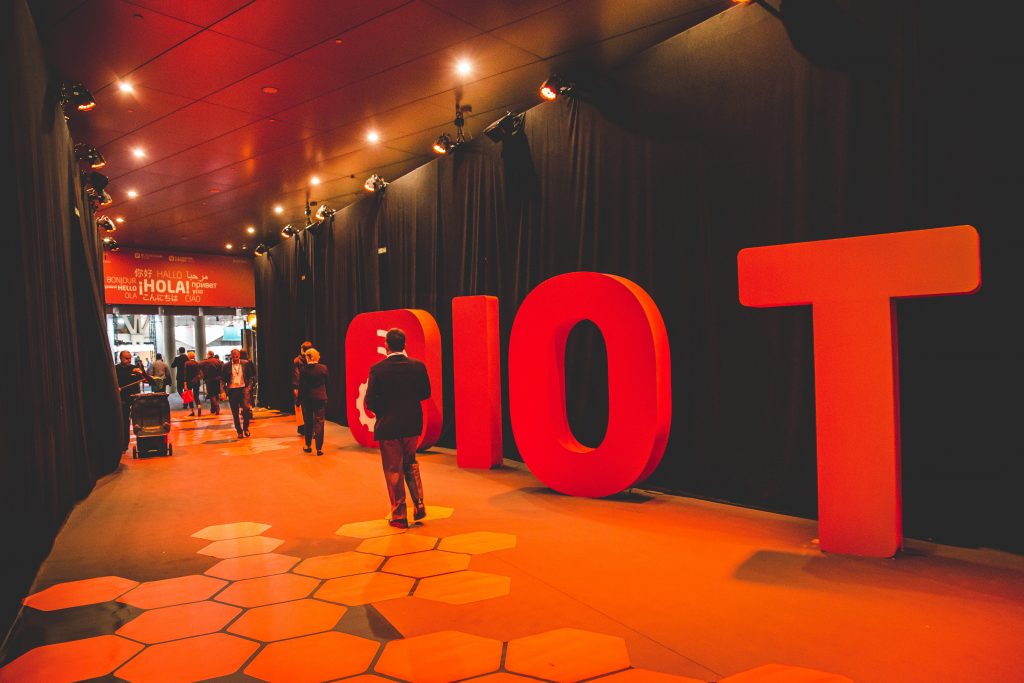
As a key player in the IoT ecosystem that is focused on changing the game by moving beyond IoT to IoE (Internet of Experiences), we were excited to take part in the IoT Solutions World Congress, October 16-18 in Barcelona.
The IoT Solutions World Congress is dedicated exclusively to bringing together IoT providers with representatives from a range of industries to find approaches to increasing productivity via this disruptive technology. We had one booth, one testbed, 20 IoT experts and two speakers.
Morgan Zimmerman, CEO of NETVIBES–EXALEAD, and I presented on the topic of Flexible Manufacturing with Predictive Maintenance. This talk and the associated interactive experience are focused on how manufacturers can improve agility, productivity and quality to achieve operations excellence and sustainable innovation. The solution proposes to leverage the Virtual World for manufacturing design, IoT data interpretation, AI learning, collaboration, decision support and flexible production rescheduling.
Attendees to the booth experienced first-hand how to approach what Morgan’s talk covered, along with two other interactive experiences. First, participants were able to discover how Dassault Systèmes collaboration platform enables continuous connected device and service innovation.
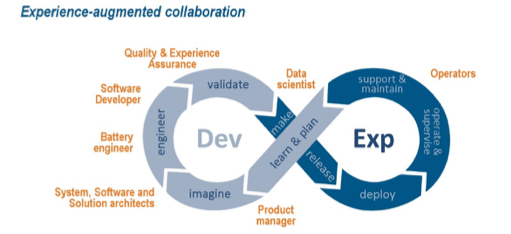
This demo showed how hardware, software and data teams can iterate in real time at same pace and with full transparency in a common V+R (Virtual + Real) environment. It demonstrated how the 3DEXPERIENCE platform supports agile and iterative design, validation and improvement of connected products and services, with testing in the virtual world for execution in the real world.
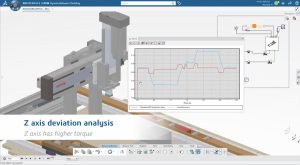
Participants were also able to check out the “Modeling and Simulation for Line Builders” demo, to discover how users can validate design early and assist or automate calibration to augment troubleshooting capabilities. To do so, kinematics and trajectories are generated from 3D high-fidelity models that are calibrated from real data, and execution deviations get interpreted in a virtual world. Specifically, it looked at how the 3DEXPERIENCE Twin provides the perfect virtual environment for agile and iterative design, optimization and support of manufacturing systems and how Line Builders can capitalize on their knowledge in virtual models, and leverage them later for rapid troubleshooting.
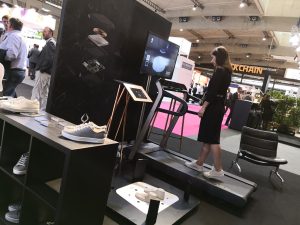
Additionally, shows attendees were able to check out QUANT-U: Data-Driven Customized Footwear Experience with ECCO’s Innovation Lab and our Consumer Goods & Retail Industry team. This testbed, which was up for an award, looks at data-driven customized footwear pilot by renowned Danish shoe brand ECCO and its Innovation Lab (ILE) partners with Dassault Systèmes Fashion Lab. An individual’s bio-mechanical data is combined with in-store additive manufacturing to create customized silicone midsoles for each wearer. The pilot experience is available at the Innovation Lab’s ECCO office and flagship store. Discover more about this story in a recent video.