5G is the blazing fast, fifth generation of mobile internet connectivity that’s promising much quicker download and upload speeds for data-rich digital factories. 5G’s high bandwidth and low lag times will pipe the gushing data across sensors, edge computing, and the cloud to slash times for ferrying executable commands and actionable intelligence. This should allow digital manufacturing to more fully exploit the interconnectivity between mobile devices, production assets, and machine cognition.
AT&T and Samsung recently announced that they are collaborating on what they’re calling America’s first manufacturing-focused, 5G “Innovation Zone.” Set up in Samsung’s Austin, Texas semiconductor fabrication facility, the goal is to understand how 5G can impact digital manufacturing. Among the 5G use cases at the testbed are Industrial Internet of Things (IIoT) sensors for monitoring and augmented reality (AR) and virtual reality (VR) for training and assistance—for example, so experts can guide a process remotely via 5G networks, “walking” a worker through the needed steps via 3D animations.
Others are also focusing on 5G-supported augmented reality for troubleshooting. Ericsson is using 5G-powered AR to sense problems and mitigate breakdown costs, with a goal to jettison instructional documents for technician training. At its Tallinn, Estonia plant, workers are using 5G AR with an Android tablet or Microsoft HoloLens—a self-contained, holographic computer that lets you engage with digital content and interact with holograms in the world around you—to identify faults through the extra detail overlaid onto the real-world image. This helps solve problems faster, with the bonus that solutions get shared sooner across other sites that face similar production equipment issues.
Mihkel Tedremaa, product technology manager at the facility, likes the time savings. “We found out while working on a faulty unit that roughly half of a technician’s time goes to non-value-added activities such as finding and linking schematics and layout files, fault info, and troubleshooting instructions.”
SKF and Chalmers University of Technology also worked with Ericsson on Phase 1 of the 5G Enabled Manufacturing (5GEM) project, envisioning digital manufacturing’s loftiest goal—individualized product customization at mass production throughput rates. They built a 5G network to gather, analyze and disseminate data in real time, seeking the benefits that come from “connecting all the tools, machines, robots, and people,” said Professor Johan Stahre, who headed the Chalmers team.
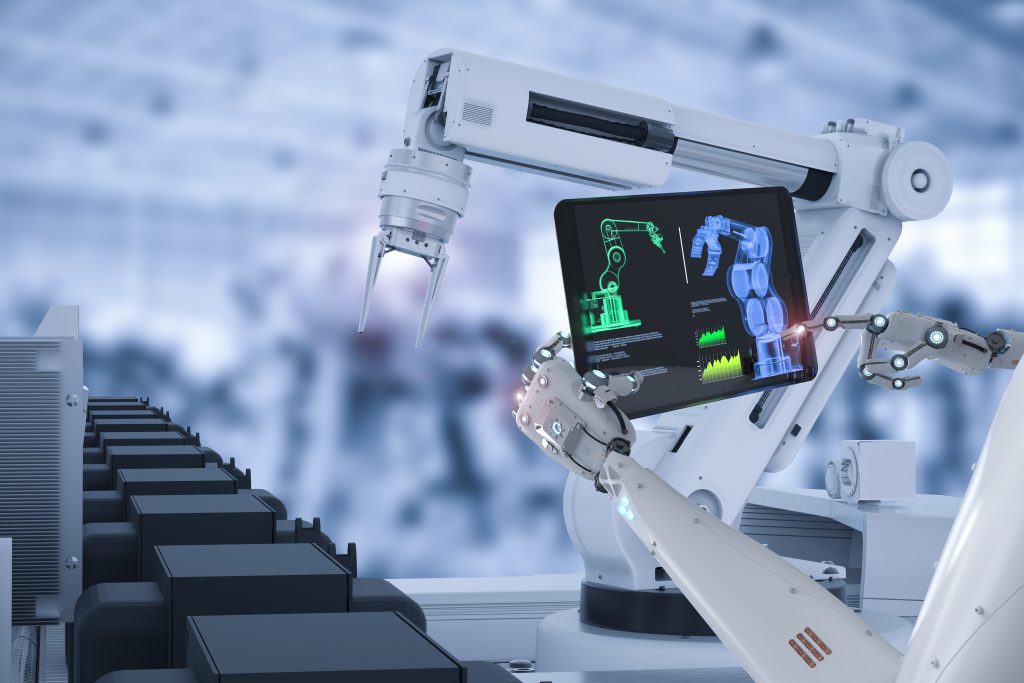
5G may be the fuel additive that helps accelerate the development of digital, smart manufacturing—what the National Institute of Standards and Technology (NIST) defines as “fully integrated, collaborative manufacturing systems that respond in real time to meet changing demands and conditions in the factory, in the supply network, and in customer needs.”
5G should also turbocharge AI and machine learning. As plant data volumes surge, 5G can populate AI and ML engines more quickly to analyze information, issue instructions and offer predictions that zip back to the mobile devices, control systems and intelligent equipment for self-optimizing production.
These 5G pilots aim to show its potential as a bedrock element of today’s Industrial Renaissance.