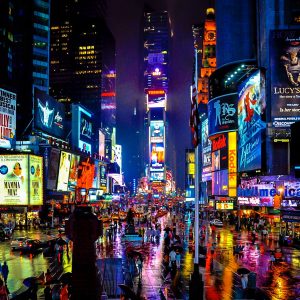
Times Square in New York City has nothing on the digital factory. But the hustle and bustle in tight quarters of the iconic New York landmark is an apt metaphor for the buzzing digital manufacturing facility, with its mix of workers, robots and machines operating in close contact and constant motion in a blur of physical activity, augmented reality and artificial intelligence.
Simulation is the key to understanding these interactions and shared environment—for productivity, flexibility and safety, as well as to prep the workforce for a tech-powered, data-driven, collaborative workspace where people, robots and machines work side-by-side.
This is more than an individual company imperative—it’s been elevated to the status of national need. A project called “The Future of Work at the Human-Technology Frontier” is one of the National Science Foundation’s “10 Big Ideas for Future NSF Investments.” The undertaking, a collaboration between Purdue University, Indiana University and the Massachusetts Institute of Technology, is based on the consensus that manufacturers, especially small and medium size businesses, are having a tough time staying current with rapid advances in digital manufacturing.
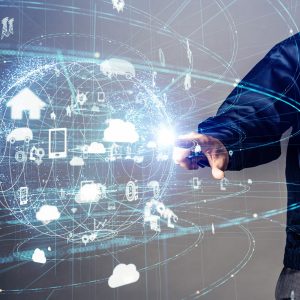
The goal is to simulate interactions between “workers, robots, and machines in future factories, and at the same time, improve factory agility and productivity,” the NSF says. “This project will provide new insights into workers’ spatial, multitasking, and predictive task abilities in manufacturing, and their performance in shared and smooth workflows.”
NSF project participants want to leverage those insights to construct a better augmented manufacturing environment—augmented, in this instance, meaning an increase in the overall “cognitive capacity” of the digital factory. One way to do this is to transfer some of the burden of instant decision-making and execution to artificial intelligence and smart automation, to increase output and the experience of the worker in the plant.
The project team of mechanical and electrical engineers, psychologists, computer scientists, education researchers and economists will use simulation to capture interactions, shared workflows and collaborative tasks in a digital form that closely mirrors a real manufacturing environment. This will let them design flexible representations of collaborative intelligence workflows and metrics to simulate how to best share work between humans, robots and machines.
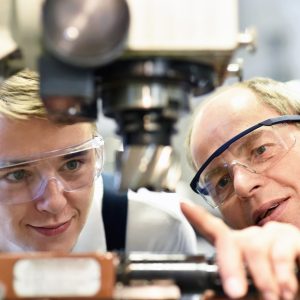
The project has a baked-in educational component, aiming to assist workforce development via educational plans and outreach to ready workers for the manufacturing workplace of the future. In a nod to our skills shortage and disadvantaged communities, researchers intend to give underserved young people access to toolkits and curriculum created during the project, as well as make the materials available to educators across the country.
Individual companies can take a similar knowledge management approach with their own simulation initiatives. Realistic simulation applications like SIMULIA and DELMIA on the 3DEXPERIENCE platform let you simulate manufacturing scenarios and interactions, capture and share insights with others and publish best practices. Other business users can then access a corporate library of standards derived from simulation to strengthen decision-making on digital factory projects prior to costly capital commitments.