The engineering community is buzzing over generative design, an emerging technology that promises to upend the slow and steady cycle of incremental improvement to help design teams unleash truly breakout innovation.
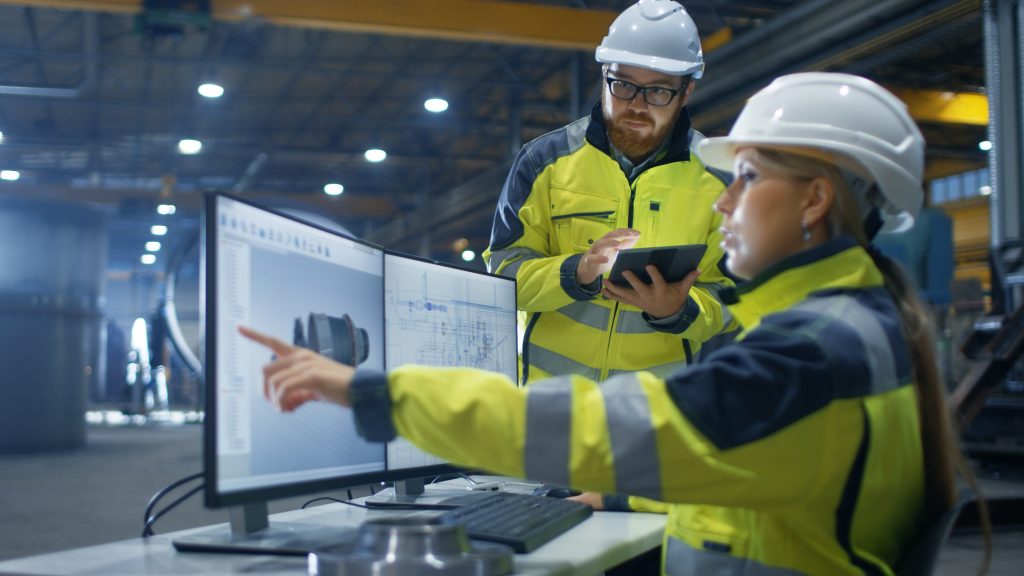
So what exactly is generative design and how does it newly empower engineers? Generative design tools harness the infinitely-scalable compute power of the cloud along with artificial intelligence (AI) and machine learning (ML) capabilities to solve complex engineering challenges that humans alone are not capable of solving.
While there’s little doubt that CAD and 3D design tools have delivered a huge productivity and creativity boost, these decades-old technologies, despite massive improvements, still put checks on the design process. An engineer, or perhaps a team of engineers, typically explore a design space that’s limited to what they know and understand about the problem, building on that finite set of knowledge to come up with a handful of best possible solutions.
That’s not the case with generative design, which combines the power of cloud computing and AI to bust open the number of design possibilities. Engineers input specific design goals into the software (performance characteristics or weight goals, for example) along with parameters having to do with cost, materials, or manufacturing constraints, and the tool cranks through all possible permutations, elevating design exploration to a whole new level.
Most leading CAD tools and design platforms are starting to incorporate generative design capabilities, delivering the sophisticated functionality once the province of simulation experts to the mainstream engineering community. With that in mind, here are four things to know about generative design before rolling up your sleeves and diving in.
It’s about creating new smart designs, not only optimizing old ones
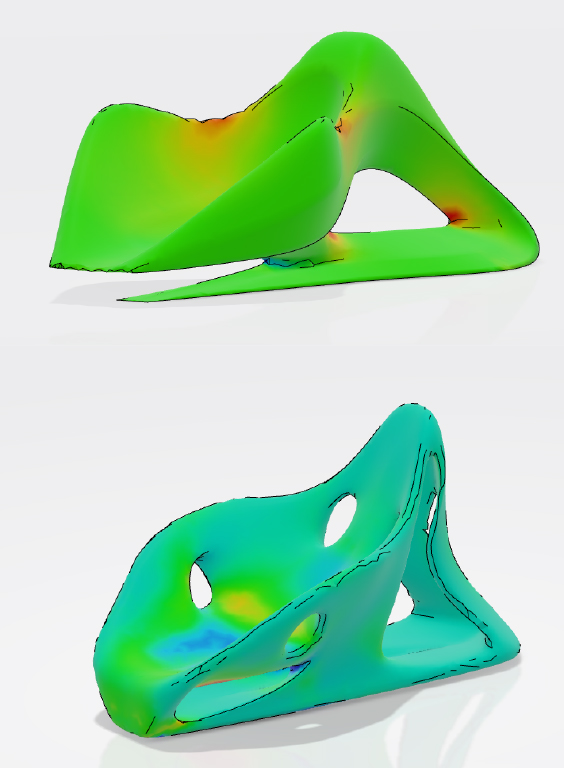
Don’t confuse generative design with other recently-hyped technologies like topology optimization. Topology optimization, which has been around for some time, is used to improve existing 3D part geometry like a bracket, for example. Based on engineers’ input, topology optimization recreates the shape by removing material typically in pursuit of light-weighting objectives. With a generative design approach, engineers input specific objectives and constraints, and the software’s algorithms automatically come up with a wide range of alternatives for design, material, manufacture, quality, and performance. The machine’s software automatically learns from the data of thousands of potential options and predicts in general the best choices, allowing the design team to choose wisely from a large number of possibilities.
It has a symbiotic relationship with 3D printing
Advances in cloud computing and AI are behind a lot of the generative design hype, but 3D printing is another factor. As new metals and other additive manufacturing software (AM) technologies flood the market and prices fall, there is finally a cost-effective way to produce the biomimicry-inspired organic shapes that result from a generative design process.
It’s about more than design
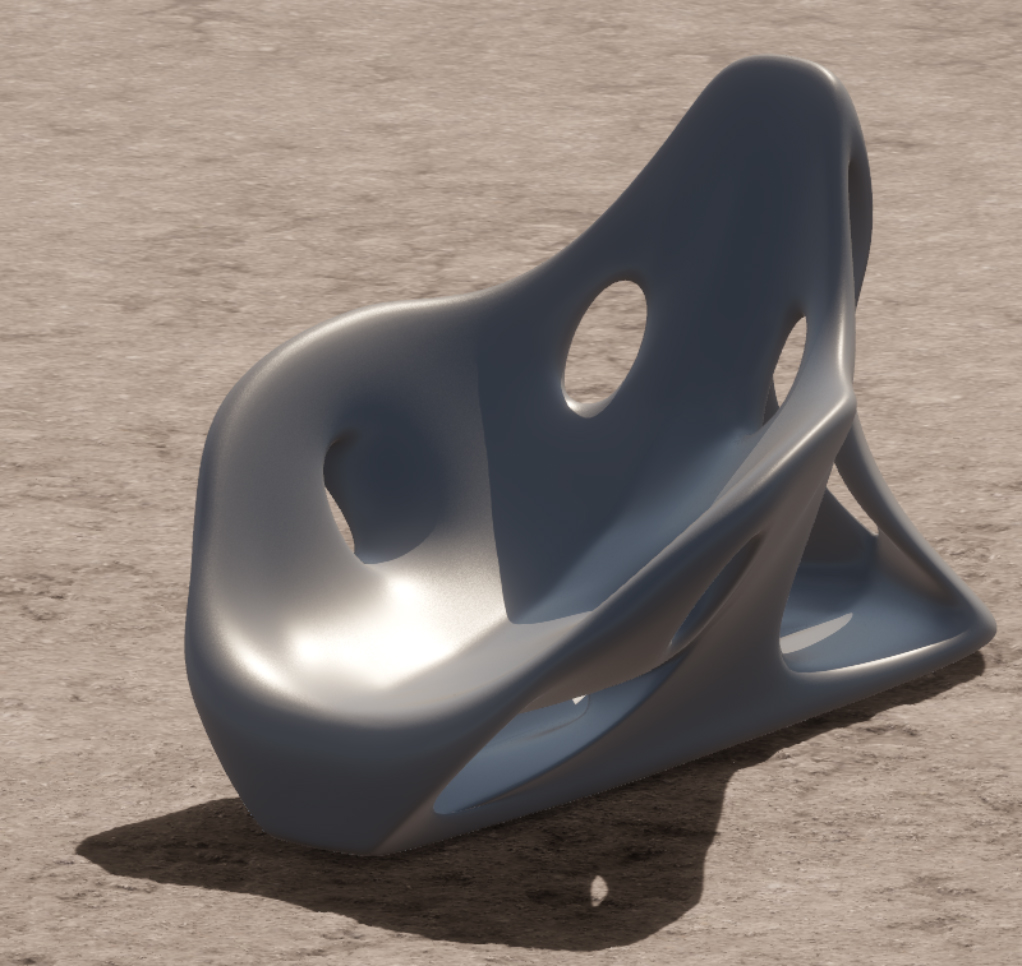
Much of the focus on generative design today is on the nature-inspired, lightweight shapes that don’t skimp on structural integrity or performance. Yet the real value comes when going beyond design parameters to consider manufacturing and materials objectives as part of the exploration process. “It’s more than about design—there is an impact on improving manufacturability,” notes Subham Sett, Director for Market Development and Strategic Initiatives for Dassault Systèmes. “No matter how good a generative design concept is, you still have to make it, and the part still needs to perform well in the field.”
It requires new skills and culture
While vendors are working to make the generative design capabilities work effortlessly behind the scenes, as of now, engineers need to be able to express their design problem as a set of parameters and constraints—for example, an acceptable weight range or a preferred manufacturing method. Not all CAD users are comfortable with such an approach so it may take some re-skilling, not just on the software, but on generative design methodology. Moreover, some may not trust the automated nature of the design results, so it’s likely to require some change management and education to get users over the hump.
No new approach comes without some pain and readjustment. The combination of generative design and 3D printing has the potential to unleash a wave of innovation and creativity not seen in engineering circles for quite some time.