3D printing seems a long way from the iconic paper crane of Japanese origami, but it’s now taken inspiration from that art form to make lightweight, complex structures that are strong and expandable, for potential use in applications like biomedical devices and space exploration.
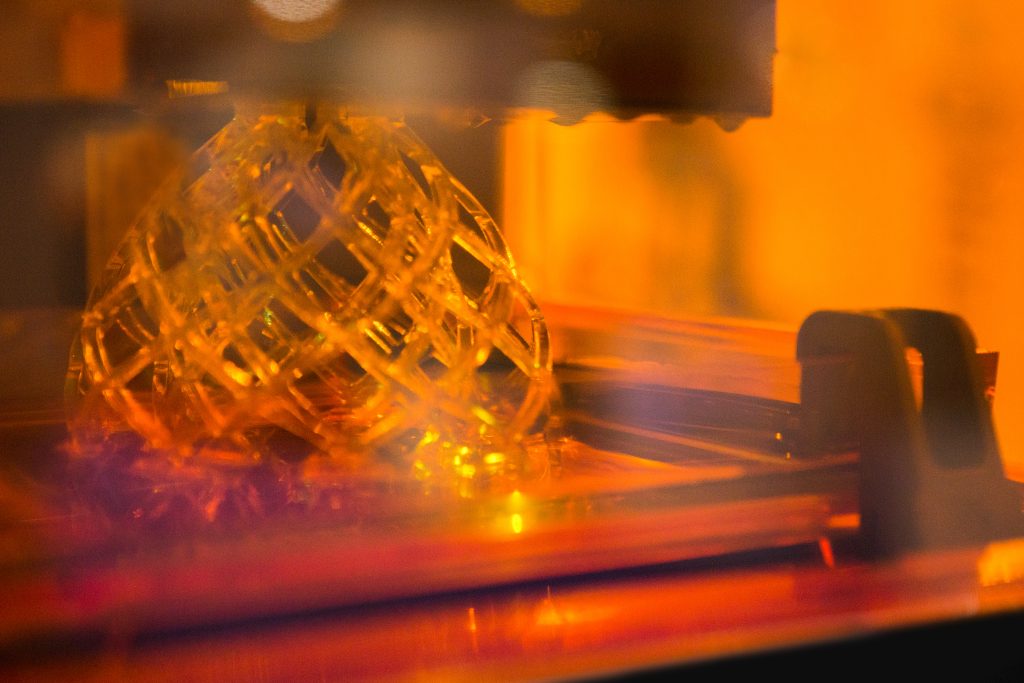
Typically, 3D printing of origami-like structures takes multiple steps and materials, plus some assembly to attach the parts together. 3D-printed structures have trouble replicating the detailed hollow features of an origami creation, because of the need to remove the “scaffolding” materials required to print the structures. It’s also a challenge to fold 3D-printed structures over and over again without weakening or breaking them from the stresses and strains.
Researchers now report they have developed an ultra-strong resin and tiny hinges that let them directly fabricate, without assembly of multiple parts, 3D-printed structures that can bear loads for engineering applications and be expanded and refolded. The findings, “3D Printing of Complex Origami Assemblages for Reconfigurable Structures,” were published in Soft Matter. The paper was authored by teams from the Georgia Institute of Technology, Peking University, and the Beijing Institute of Technology.
These tinkerers utilized Digital Light Processing, a 3D printing technique that prints layers of liquid resin that are cured and hardened by ultraviolet light. The researchers developed a new resin, a strong, yet soft and foldable material that can be stretched to a larger size. The elastic substance is critical for the hinges, which are placed along the creases where the structure folds, and are made of a thinner layer of resin than the panels to enable that folding. The researchers reported the structures could bear 100 times their own weight, and be folded and unfolded repeatedly without breaking.
“Computational origami” like this is relevant to numerous industries—think air bags and arterial stents. One type of origami fold has been used to deploy solar panel arrays for space satellites. The National Science Foundation established a program called Origami Design for Integration of Self-assembling Systems for Engineering Innovation, aimed at building a mathematical and material foundation for self-folding origami systems and commercialization. MIT researchers created a widely applicable algorithm for folding paper into a 3D shape, with possible use across other materials in 3D printing.
Professor Glaucio H. Paulino, one of the researchers and paper authors, teaches a class at Georgia Tech called Origami Engineering. Students designed and built an origami-inspired cast that’s easy to clean, breathable, and has the potential to reduce patient pain and infection rates; flat-foldable outdoor tents for fast deployment during emergencies; fold-flat kits that can be rapidly assembled into temporary hospitals, rescue centers and group shelters; and a self-cleaning solar array, with folds and drainage holes to prevent damage during sandstorms.
Being able to 3D print an origami-type device would be icing on the cake in situations where something needs a compact form to get to where it’s going and a different shape to do the job when it gets there.