In a world where consumer prices are constantly on the rise, companies must take a close look at their supply chains to ensure they are cost-effective and efficient and always producing goods of a consistent quality. However, supply chain disruptions can happen at any time, and can be a major issue for manufacturers.
From weather to politics to resource depletion, these disturbances often have consequences that trickle down and affect consumers. But they don’t have to. With technology that enables companies to map out all the variables in their supply chain, pivoting between suppliers, transportation companies and more can be a simple process that doesn’t mean higher prices for shoppers.
From utilizing big data analytics to streamlining processes, here’s how companies can manage their supply chains to optimize costs and minimize price impacts for their customers.
What are supply chain disruptions?
There’s nearly no limit to the types of factors that can cause a disruption in supply chains. For goods produced from agricultural products or byproducts, weather can be a disastrous one. Droughts, cold spells and heat waves can damage crops or prevent them from growing outright, and climate change can affect the amount of crops that a particular supplier can expect to produce. Similarly, weather patterns or occurrences like floods and forest fires or hurricanes and tornadoes can destroy or affect manufacturing plants or transportation routes, slowing down production or the movement of goods.
Perhaps somewhat less predictable, political factors can also take a toll on supply chains. Changes in trade agreements – or outright trade wars – and embargos can wreak havoc on the ability for goods to be moved, as can violent conflict. Political shifts can wind up with materials either being physically or financially inaccessible, which can be disastrous for companies.
Other extenuating factors can disrupt supply chains, like depletion of natural resources or a supplier or vendor going out of business. Disease, whether it affects animals grown for meat or dairy, or humans – like the Covid-19 pandemic – can also impact supply chains drastically. Whatever the reason may be, these disruptions are common and can happen at any time, so it’s imperative that businesses be wary of all the ways things can go wrong and ensure their back-up plans are in place accordingly.
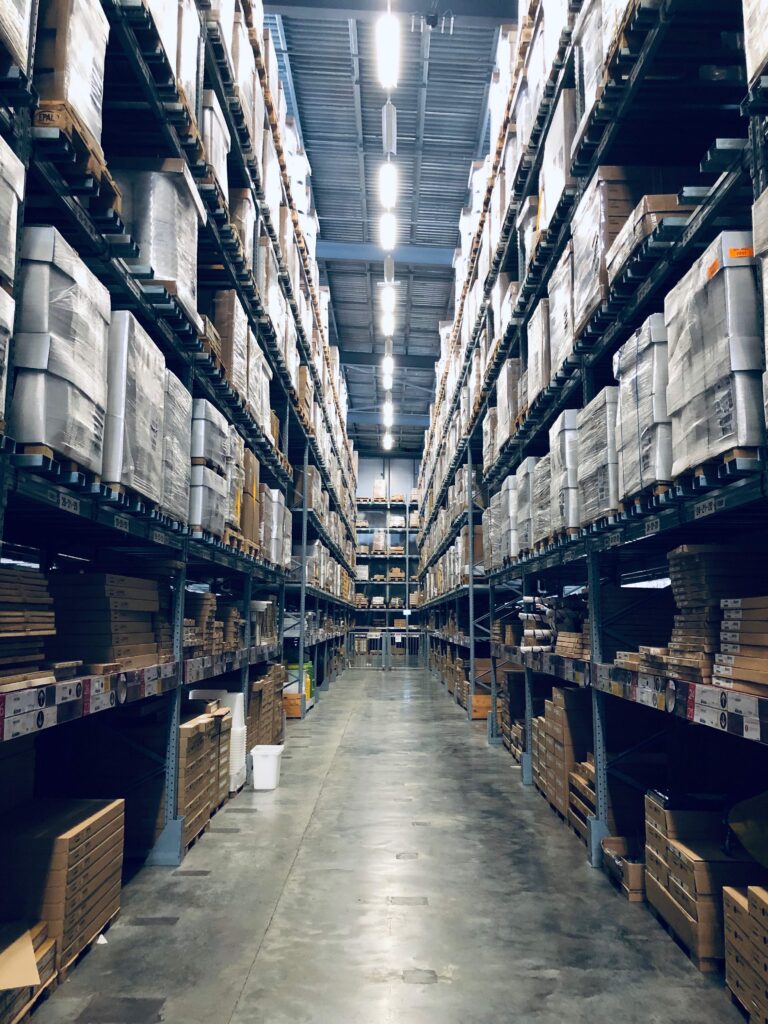
What are the consequences of supply chain disruptions?
Given that changes in supply chains are relatively common, manufacturers need to have plans to ensure that their processes aren’t affected by external events, or that those events provide as little an effect as possible. Disruptions to supply chains can mean that certain materials or goods are less readily available, and despite their decrease in supply, they may still be in high demand, thus forcing prices up. Transportation can also be hit, with the ability to move goods either slowed or prevented entirely, or a new need may arise in which goods may need to be sourced from an entirely different location, creating the need for new transportation processes.
Perhaps one of the most glaring examples of the effects of a disruption recently has been the price of eggs. For shoppers in the United States, the cost of this kitchen staple rose up to 70% over the course of 2022, compared with the year before. While the most obvious culprit would appear to be avian flu – it killed millions of birds throughout the year last year – there’s more at play. Wheat, a significant Ukrainian export, is a key component in chicken feed, and with the conflict in the country slowing the movement of goods, this necessary ingredient’s supply has slowed, increasing its price. These factors, combined with rising inflation, and increasing necessary operating costs, like the additional expenses associated with disinfecting bids and coops from avian flu, has caused a rapid and noticeable increase in price for eggs for consumers at the store.
While the uptick in egg prices represents a fairly localized issue – it affects consumers on an individual level and companies that produce goods using eggs – there’s one material shortage that’s affected more than 150 industries and counting. Supply chain disruptions in the production and manufacturing slowed down the output of semiconductor chips on a massive scale.
Unlike eggs, semiconductors have countless uses, from electronic equipment like cell phones and computers to household appliances to cars and more. The inability to get these chips has slowed innovation and prevented companies from producing and manufacturing goods, therefore increasing their cost as supply decreases yet demand rises. The ripple effect from the loss of access to this single component was estimated at more than €220 billion ($240 billion), indicating just how valuable a smooth supply chain can be.
The uptick in cost represents one of the most common ways that producers and manufacturers deal with the consequences of supply chain disruptions. When things go south, companies can attempt to continue their business practices as they had before the disruptions occurred, or they can try to find ways to offset the costs.
When done incorrectly – say, using a lower quality component or ingredient when the original becomes unavailable – this can cause a final product to be less valuable to consumers. A product of lesser quality or of original quality but at a higher price won’t be an acceptable outcome for long; shoppers will soon enough change their habits in accordance to what’s available.
One recent example of this issue comes from a British fashion company famous for their highly-recognizable rubber rain boots which recently filed for bankruptcy. A variety of factors contributed to their dip in sales, including warmer-than-usual weather and inflation, but the real kicker was a decrease in customer satisfaction. Like many companies, they struggled to find solutions to maintaining procurement, production, manufacturing and shipping speeds during the pandemic, and this, coupled with a reportedly lower quality product whose price remained the same, led to their goods becoming less appealing for consumers.
How can companies address disruptions with minimal effects on consumers?
A number of outcomes can occur from supply chain disruptions. Consumers may find consistent quality being priced higher than normal, or lower quality goods at their previous cost, or they may simply be faced with shortages of goods, or significant shipping delays. None of these options are the best-case scenario for buyers or sellers.
So, what is?
To tackle disruptions to the supply chain, technology is a company’s best friend. Mapping out the entirety of a manufacturing supply chain with a virtual twin, including all variables related to quantities and locations of supply, transportation costs, tariffs, formulations and more can ensure manufacturers are prepared for all situations.
DELMIA’s Quintiq Perfect Supply Chain Industry Experience enables exactly that.
While once upon a time supply chains may have looked like relatively straightforward flows of goods, today, they’re more like highly complex webs. Companies may have dozens, hundreds or even thousands of suppliers or vendors for a particular material or component in a larger product, and each of those could be sourced from a different location and be of varying quality.
Imagine that, for a given product, one ingredient is transported via truck from location A, and must arrive at plant B within a given timeframe. If that ingredient’s quality or availability changes, or war, weather or another factor affects the ability to transport it in time, the manufacturer must remain agile and be able to pivot to supplier B in location B to ensure they’re meeting the production goals.
Because of the dynamics of the global economy, it’s not uncommon for companies to have manufacturing facilities producing the same goods in different places around the world. Doing so cuts down on the need to ship products to far locales, meaning lower operating expenses for transporting them.
However, doing so also means that the raw materials for those goods are being sourced from different vendors. To ensure that every final product is of the same quality no matter where it’s being produced, companies have different formulations for the same products that are tailored to the places where they’re produced. To keep track of these variables, the Perfect Formulation Solution enables easy and simple management of product specifications to maintain all the different inputs and outputs required.
To give an example, product X is produced by company Y in locations A, B and C. Locations A and B are quite similar in terms of weather, and particular humidity, but location C has a completely different climate. Because the climates are different, the plants that produce the goods must be attuned to the changes that weather can have on the final product. The raw materials needed to produce the same goods consistently across multiple facilities may also differ, depending on the local factors that can affect its quality; changing a percentage needed here or there can make a world of difference.
Having a tool that empowers companies to see exactly how to make these adjustments allows for the most effective supply chain management.
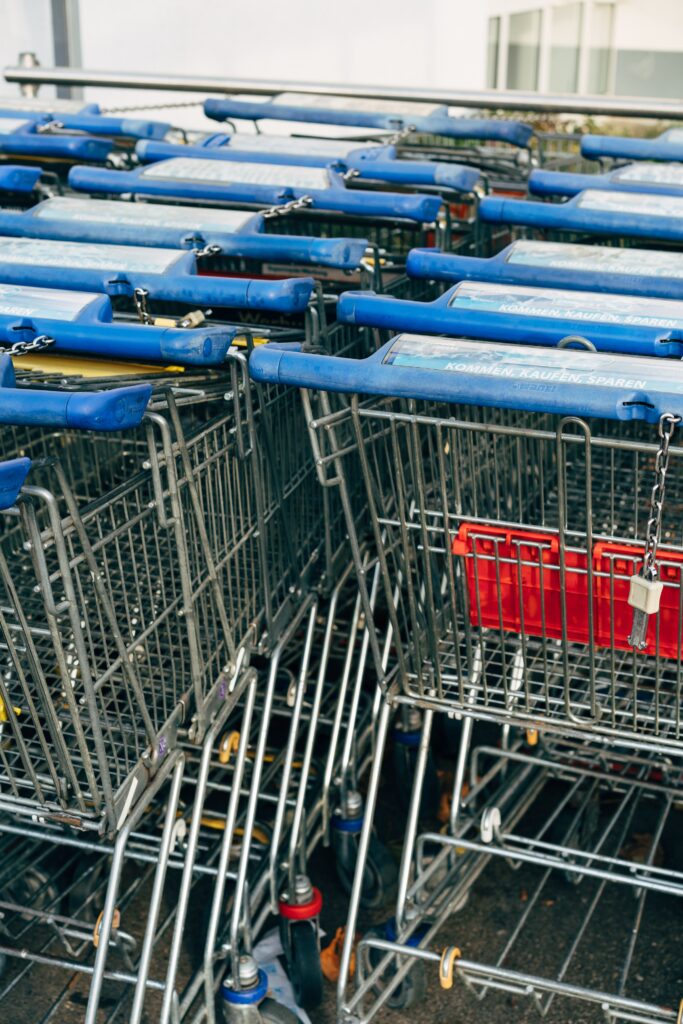
How does effective supply chain management benefit consumers?
An optimized supply chain creates consistency, a necessary outcome for consumer satisfaction. Producing the same quality product at the same price point – or reasonably close to it – is the goal of any company manufacturing goods, and technologies that enable this are invaluable.
The very visible rain boot company was unable to retain customers when its quality dipped despite prices remaining the same. Consumers in the U.S. have turned to a variety of methods of getting eggs, from smuggling them across the Mexican border to buying chickens to lay them at home – though the vast majority have simply purchased fewer eggs or just dealt with the consequences and cut back on grocery expenses elsewhere.
Neither of those solutions are long-lasting. Consistent quality and pricing are two incredibly important aspects to customer retention, and as an extension of that, brand loyalty.
Putting supply chain management to the test
For one global niche food brand, ensuring a disruption-free supply chain is an essential part of business.
Amy’s Kitchen, which produces frozen vegetarian meals, prides itself on using only organic and locally-sourced ingredients from small farms. While that shortens transportation costs and times, it means that any localized event can affect their ability to produce their meals. The company has more than 300 suppliers for each individual good they sell, dozens of processes and thousands of SKUs, meaning there are a nearly endless number of variables in their supply chain. Not to mention, because they’re dealing with foodstuffs which could spoil, the speed with which they need to handle their goods is of utmost importance.
That’s why mapping their supply chain with DELMIA Quintiq was a necessity for the company. Moving from an antiquated spreadsheet-based system to a supply chain virtual twin has allowed them to remain agile, especially in the face of disruptions. The company implemented the solution over 4 phases, and were able to hone it to increase response times to changes in product demand, improve material forecasting and simplify order fulfillment, shipping and more.
Integrating all these tasks in an easily manageable software allowed Amy’s Kitchen to streamline their business practices to be able to pivot and remain profitable, regardless of external factors. The company was able to avoid the pitfalls that others have experienced, raising prices for consumers or producing lower-quality goods. Using technology helped them stay consistent and successful.
Whether it’s a family-owned company like Amy’s Kitchen, or hundreds of thousands of egg producers, or a single fashion company, it’s clear that supply chain disruptions can be a serious burden to businesses. They’re impossible to avoid, and can happen at any time. What is possible, though, is ensuring manufacturers have the tools they need to mitigate the consequences of these disruptions, no matter how difficult they may be. Technological solutions like virtual twins give companies the ability to confidently handle any situation with ease, and that in turn gives consumers peace of mind.
Learn more about the Consumer Packaged Goods – Retail industry