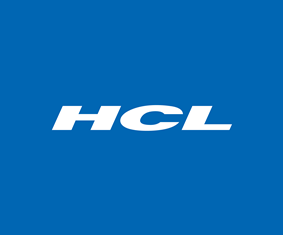
The digital age is firmly upon us and the traditional industries like manufacturing, and generally, all B2B industries, are finding it tough to be market-relevant in this new experience economy. Irrespective of the size of the company, some common challenges, like the lack of digital skills and infrastructure, inertia of existing pre-digital processes, and executive dilemmas on ‘digital strategy vs. roadmap vs. ROI’ exist. But, to top it all off, the rigid organizational structures driven by conventional workflows and dated processes remain the building blocks of all the enterprises across the design-build-operations lifecycle.
These impediments are not allowing businesses to seamlessly shift into the digital transformation model that can cater to businesses in the new C2B paradigm. Therefore, it has become crucial for companies to leverage product-level and process-level twins in realizing digital dreams. The true power of the digital twin can be realized when different twins are connected to each other – thus creating a Twin2Twin (T2T) ecosystem.
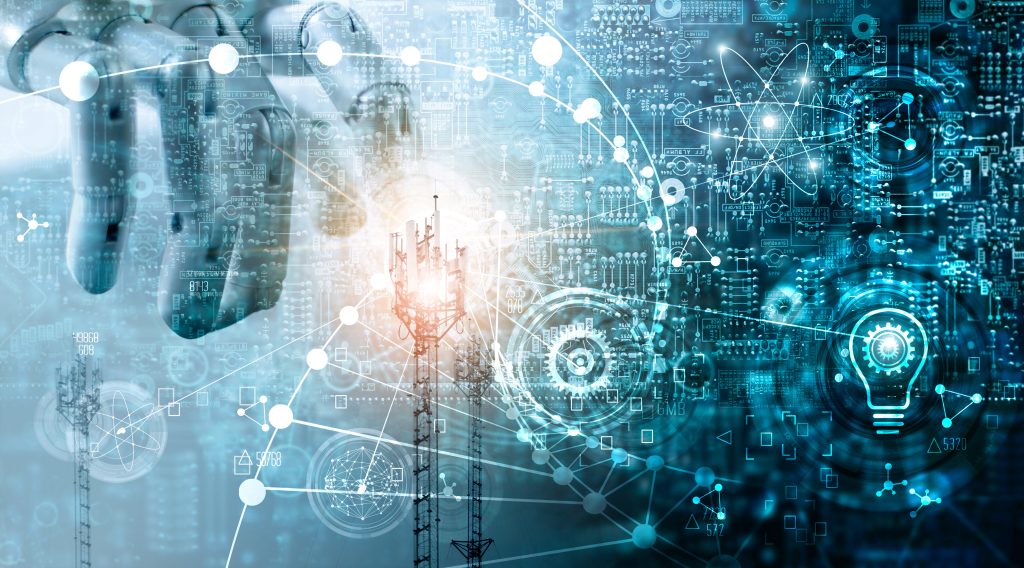
While M2M has helped generate terabytes of data, T2T will help put that data to effective use in a structured manner. T2T will not only help formulate the most effective digital transformation strategy for the enterprise, but also help visualize the benefits at each milestone of that digital transformation strategy.
The experience design phase has been using twins to ensure the best possible quality of experience (read product). The build-and-run phase of experience can derive benefits like best yield and precision of delivery through T2T approach.
At the machine level, the digital twin leverages real-time data at each step of production to ensure every operation is carried out correctly and that no equipment is drifting out of tolerance. With enhanced M2M2P, T2T interactions, the machine twin can thus cascade its decision to the rest of the plant seamlessly.
At the plant level, asset twins and process twins enable engineers to constantly improve product and plant quality, equipment performance, and reduce downtimes. For example, when an engineer needs to implement a fix, instead of wasting crucial time reviewing data from across the plant, the process twin helps him look at the entire downstream process and select the best time for repairs. With a process twin, the engineer can make this decision from any remote location. He can also coordinate with suppliers and other engineers from different locations simultaneously.
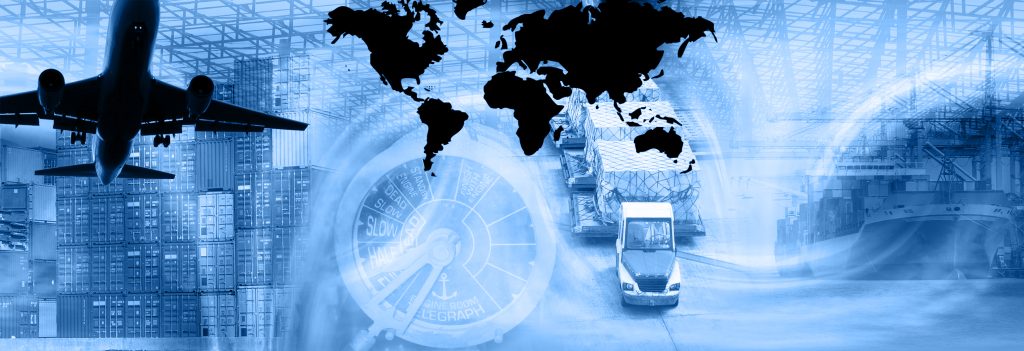
At the supply chain level, digital twins contribute the most value with hyper automation and real-time synchronization of demand vs delivery for parts to products. New suppliers or new logistics routes can be dynamically integrated and optimized for maximizing returns with minimal human intervention. Process twins warrant digital integration of internal factory processes and decision-making workflows to mass-customize the lines as well as ensure fulfillment to client sites with precision. This kind of T2T integration is crucial as manufacturers embrace one-size-fits-one business models creating customized products for each customer.
For GE Power & Water, a wind farm is firstborn as a digital twin on their platform. The digital twin is a cloud-based computer model of a wind farm at a specific location. This model allows engineers to customize the pole height, rotor diameter, and turbine output for each pad at the wind farm, and design its most efficient real-world doppelganger. The digital twin allows turbines that are tailor-made for each location, instead of having to choose standard configurations.
Wind farms then leverage the digital twin technology to monitor structural loads once the farm is in operation. Real-time data from on-ground sensors is fed into the cloud-based digital twin of the wind’s physical system and its integration with wind turbine twin helps visualize drifts in structural stresses.
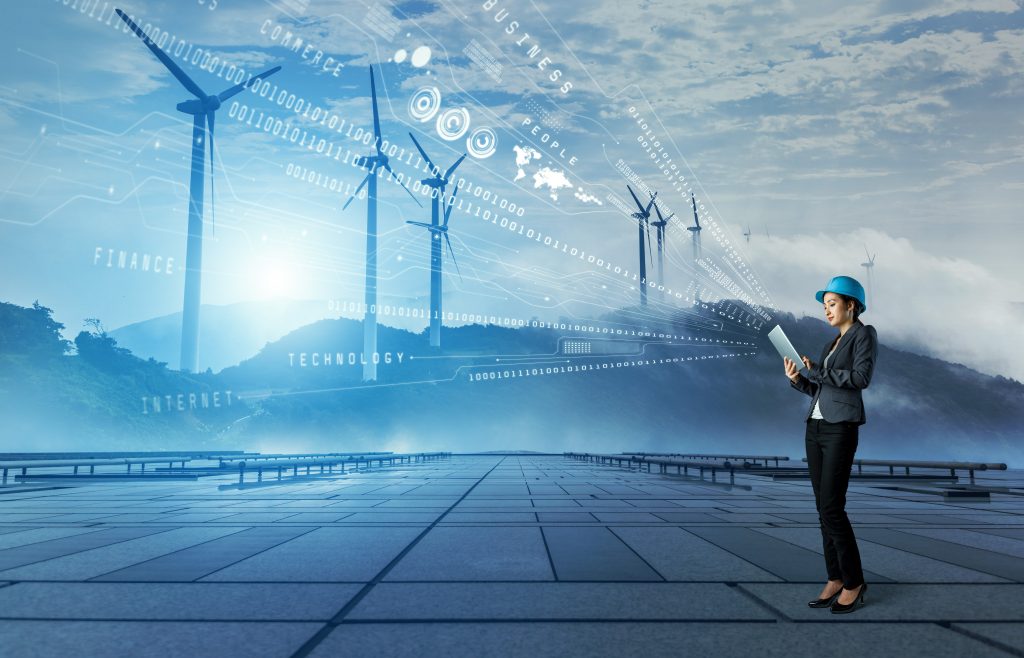
Hence, a ‘digital twin’ is not just a digital replica of products or physical systems, but also of processes and workflows visualizing the entire IP creation and consumption lifecycle. The twin can constantly analyze incoming data from thousands of sensors and systems distributed across the process. It then uses ‘performance fencing’ to determine improvements in each step or do impact-analysis to incorporate new material, machines, and methods.
“Comau developed a process twin solution that helps manufacturing companies improve efficiency and cut costs. Technicians are using the mixed reality of Microsoft HoloLens to remotely monitor factory machines, giving manufacturers a new way to interact with data on the factory floor via natural gestures and hands-free operation.”
Twins clearly help create efficient, industry-specific products (e.g., once you have twins of pumps and twins of different industrial applications, you can quickly create and validate industry-specific variants. The digital twins of all value chains can be networked to get a detailed digital twin at the enterprise level.
This can help identify OFIs (opportunities for improvements) to constantly align all value chains to customer-defined value. Visualizing and controlling business risk is the biggest need for any enterprise. It can maximize returns through ‘modeling the risk’ to push each value chain to its last bit of productivity without hampering its quality or integrity. This is what digital twin aspires to offer and, hence, will be a vital initiative for the 21st Century Enterprises.
To embrace and utilize the different workflow transformations, it is essential for any company to understand the maturity of the digital twin causing these transformations. A light twin uses a small number of data sources and contains just enough data to create derivative data. The next level ‘clone’ is not data- or power-constrained. It can support prototyping. The ‘augmented’ twin contains a high level of information about the asset and environment. It cascades more intelligence into the twin with ML/DL algorithms and improvises its prediction by self-healing.
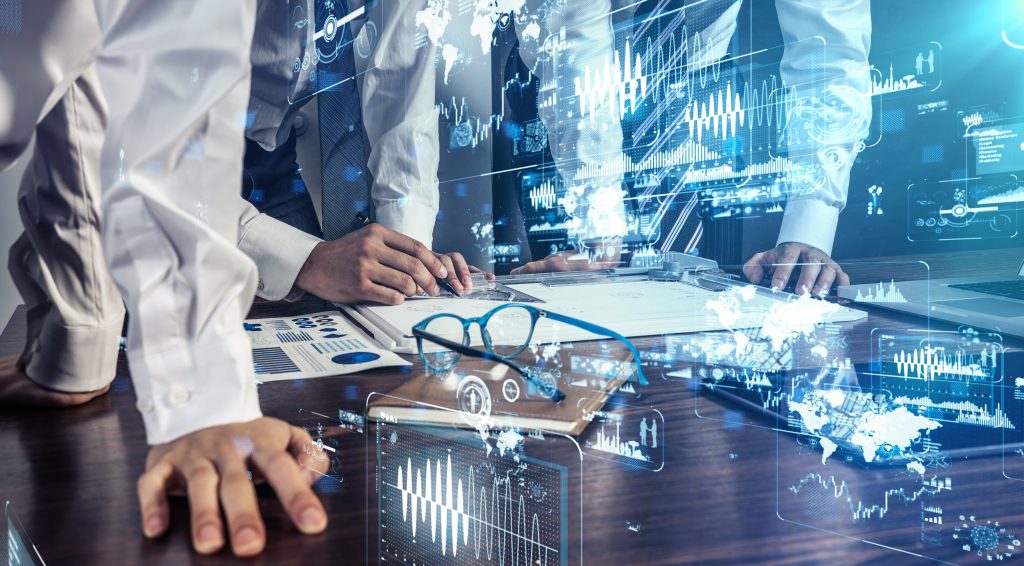
Twins with varying degrees of capabilities and functional maturity can be leveraged to predict the impact of changes in different workflows while adopting a digitalization strategy and deciding important customizations of generic strategy. All Industry 4.0 initiatives can be implemented well by seamlessly integrating them with process digital twins. For example, Augmented Reality apps can be implemented to monitor the changes in shop floor processes. When a problem is detected, the twin can be used to identify the corrective action flow that can be visualized on the lens.
Direct Data Monetization is the Holy Grail among all growth drivers in 21st Century Enterprises. T2T offers a mechanism to package the product and process data in a meaningful way that one can share and charge with substantial validation of its value. There are business models and protocols evolving to monetize each data unit that is shared. So, in the future, if a power plant needs a transformer before it creates the plant, it will look for a supplier who can provide the best twin that suits its dimensional, functional, and operational requirements. They may even get manufactured locally, but they will pay for the best TWIN transformer!
Products will offer a finite experience to customers when commissioned. At the same time, once deployed, they will tend to live much longer due to better predictive maintenance. Hence, both customers and manufacturers will have to leverage twins to constantly generate new value spins. Next-gen enterprises will have to embed digital twin labs as a core enterprise group that will innovate and maintain the inventory of live twins. Twins from various enterprises will work together to create a vibrant T2T economy. Digital twins and the federated T2T methodologies are thus the new set of vital IPs that will keep an enterprise on the competitive edge with a virtual factory software to constantly harvest new experiences.
In fact, I believe that twins will be reported as assets in an enterprise’s balance sheet, very soon!
Editor’s Note:
HCL Technologies is a trusted 3DS partner. As a global company, HCL Technologies brings IT and engineering services expertise under one roof to solve complex business problems for its clients.