The following article is excerpted from Infrastructure Lifecycle Management Through Virtual Twins, a whitepaper developed by Dassault Systèmes. To read more and learn more about the details of virtual twin for construction simulation, download the full whitepaper here.
SFEG, Zhoujiazui Road Cross-River Tunnel: Virtual Twin for Construction Simulation
Background
A key goal in Shanghai’s bid to become a global city of excellence by 2040 is the reduction of average commuting times to less than 40 minutes. The 4.45 kilometers Zhoujiazui Road cross-river tunnel, currently under construction, is a key project that will help achieve these goals by reducing traffic congestion on the heavily travelled Yangpu Bridge.
Challenge 1
BIM was mandatory to tender a bid for the Zhaojiazhui Road Tunnel project.
Solution
Tunnel construction involves multiple parallel construction processes, such as transporting and installing tunnel segmental lining, advancement of TBM and installation of support structures.
CATIA was used to create a precise parametric 3D model of the tunnel, which is driven by 3D alignment. With advanced measuring technology, SFEG can measure the actual alignment by TBM and use the measured data to update the 3D digital model. Then the digital model will be used to fabricate tunnel segmental lining, so that SFEG can ensure the fabricated tunnel segmental lining will match the actual tunnels made by TBM. Also, the updated 3D model will be used to guide TBM, adjust its movement and control the overall tolerance from predefined alignment.
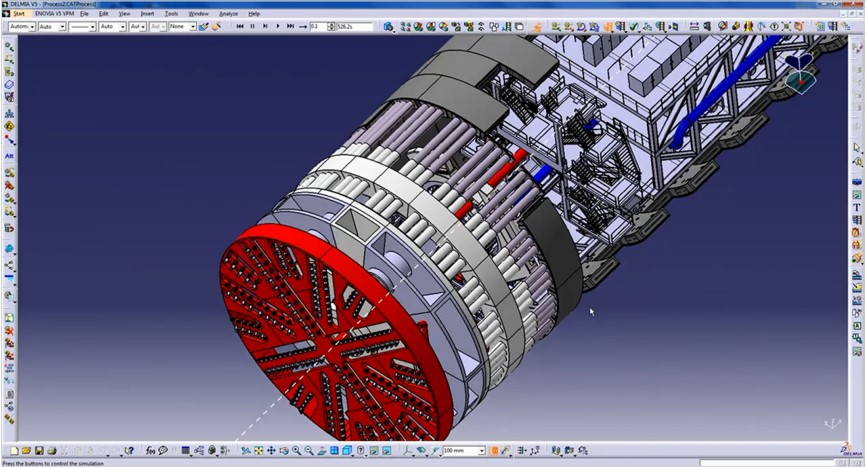
Success factor
SFEG efficiently translated the complex construction data and technical issues of the Zhoujiazhui cross-river tunnel project into intuitive digital references. The early identification of risks has drastically reduced problem areas, improved communication and collaboration among multiple parties, and optimized workflow, so that the project can be delivered on budget and on schedule without compromising quality.
Excerpted from Infrastructure Lifecycle Management Through Virtual Twins, a Dassault Systèmes whitepaper. Download to learn more.
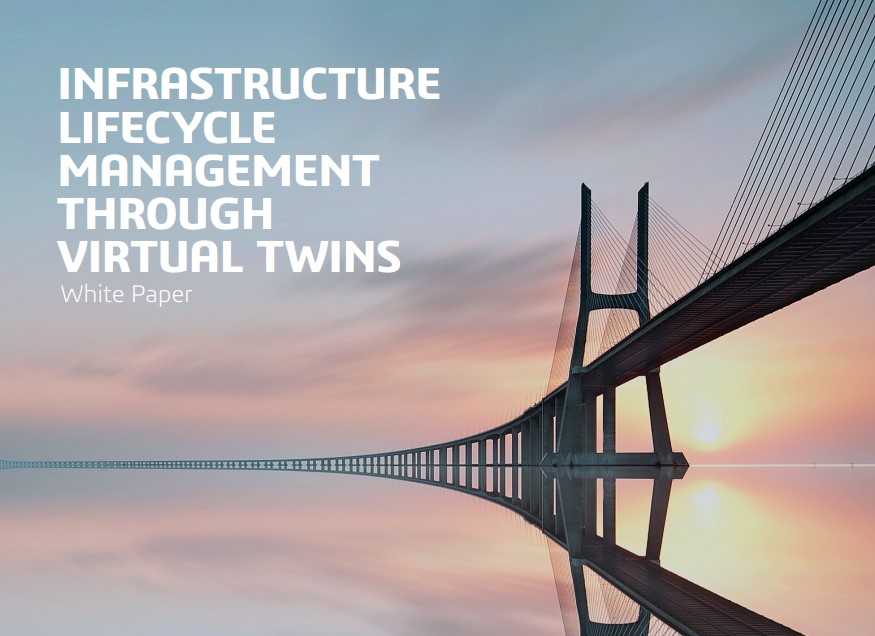
This white paper is presenting industry trends in Construction, Cities & Territories covering infrastructure lifecycle management through virtual twin. Building Information Modelling (BIM) is currently taking over the traditional methods for infrastructure developments, operation and maintenance. Using BIM and virtual twin allow collection, analysis, and aggregation of data and enhances collaboration between different stakeholders, from design to operation and maintenance.
Related links:
Dassault Systèmes Construction, Cities & Territories Industry
Solution
SIMULIA Finite Element Analysis (FEA) enables designers and engineers to create simulations of how the tunnel boring machine (TBM) excavation would impact on real world forces like vibration and fluid flow, and the other physical effects it would have on the surrounding areas. The software separates the geological model into finite elements and uses mathematical analysis to predict the behavior of each element and the overall impact on the surrounding areas.
As construction progresses, the 3D model with construction simulation will enable engineers to predict and resolve problems in advance. The data generated is stored in the BIM models, and the FEA results are retrievable at any time for added convenience and to enable speedy alterations.
Challenge 3
The movement of TBM may not adhere to the predefined alignment, so there is an allowable construction tolerance for re-calculation and redesign of tunnel segmental lining.
.
Solution
Tunnel construction involves multiple parallel construction processes, such as transporting and installing tunnel segmental lining, advancement of TBM and installation of support structures.
CATIA was used to create a precise parametric 3D model of the tunnel, which is driven by 3D alignment. With advanced measuring technology, SFEG can measure the actual alignment by TBM and use the measured data to update the 3D digital model. Then the digital model will be used to fabricate tunnel segmental lining, so that SFEG can ensure the fabricated tunnel segmental lining will match the actual tunnels made by TBM. Also, the updated 3D model will be used to guide TBM, adjust its movement and control the overall tolerance from predefined alignment.
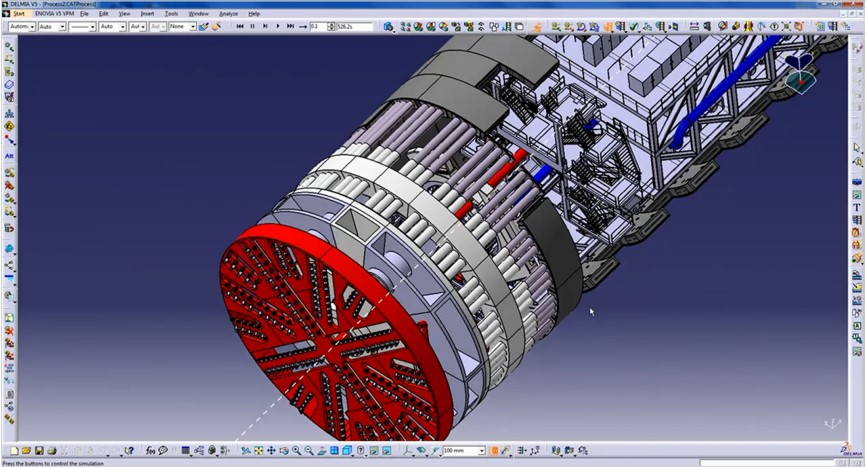
Success factor
SFEG efficiently translated the complex construction data and technical issues of the Zhoujiazhui cross-river tunnel project into intuitive digital references. The early identification of risks has drastically reduced problem areas, improved communication and collaboration among multiple parties, and optimized workflow, so that the project can be delivered on budget and on schedule without compromising quality.
Excerpted from Infrastructure Lifecycle Management Through Virtual Twins, a Dassault Systèmes whitepaper. Download to learn more.
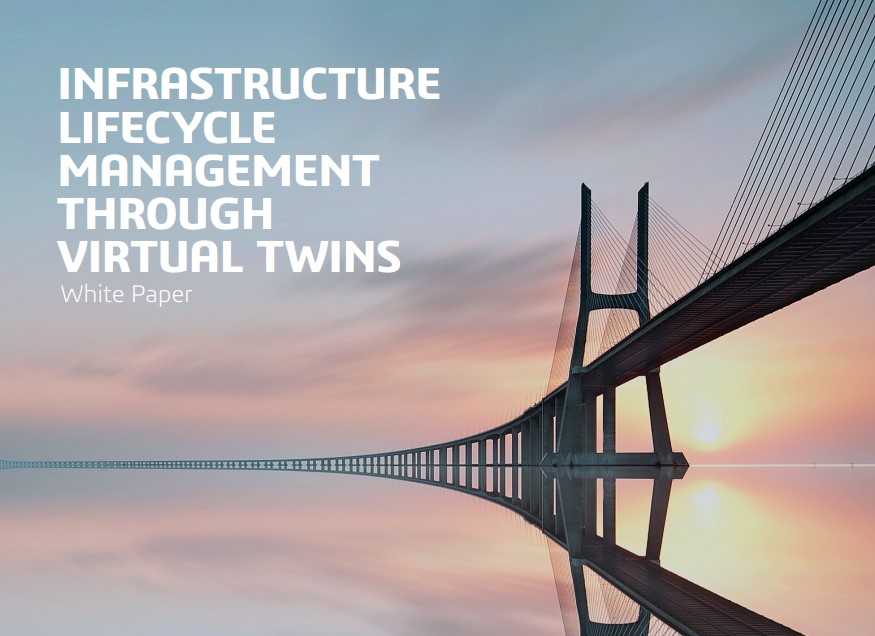
This white paper is presenting industry trends in Construction, Cities & Territories covering infrastructure lifecycle management through virtual twin. Building Information Modelling (BIM) is currently taking over the traditional methods for infrastructure developments, operation and maintenance. Using BIM and virtual twin allow collection, analysis, and aggregation of data and enhances collaboration between different stakeholders, from design to operation and maintenance.
Related links:
Dassault Systèmes Construction, Cities & Territories Industry
Solution
BIM was used to generate visual representations of the project construction process. Dassault Systèmes’ CATIA was used to create a 3D model of the tunnel, and DELMIA was used to simulate in vivid animation how the tunnel would be built. Decision makers were able to instantly understand the entire project, including constructability, resource estimates and the impact of the development on people and the environment. This eliminated the need to hire a design firm to create separate 3D visualization, a traditional route that incurs additional cost. At tender evaluation, scores were split between technical elements and commercial elements. SFEG scored the highest in technical elements and won the bid.
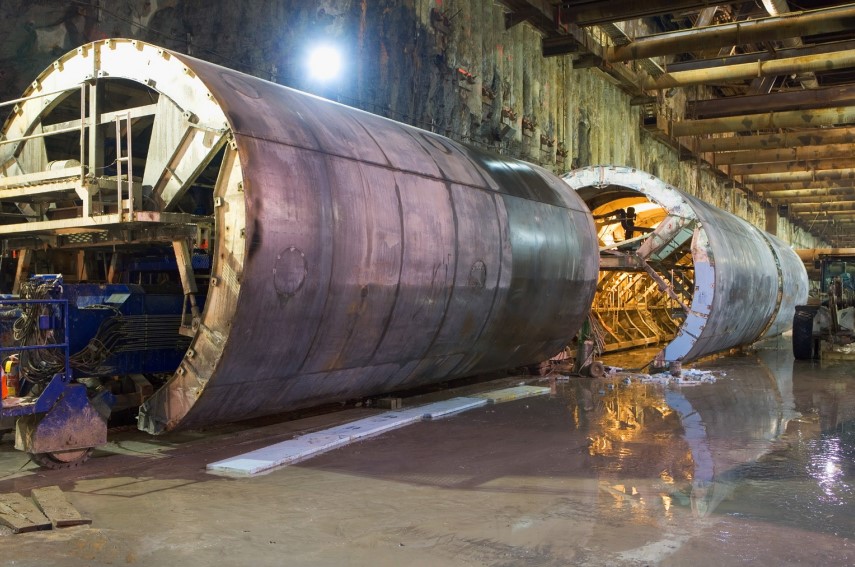
Challenge 2
The tunnel passes through several sensitive areas, such as the Academy Building of Shanghai Polytechnic University, the foundation piles of a pier and a residential area near the construction site.
Solution
SIMULIA Finite Element Analysis (FEA) enables designers and engineers to create simulations of how the tunnel boring machine (TBM) excavation would impact on real world forces like vibration and fluid flow, and the other physical effects it would have on the surrounding areas. The software separates the geological model into finite elements and uses mathematical analysis to predict the behavior of each element and the overall impact on the surrounding areas.
As construction progresses, the 3D model with construction simulation will enable engineers to predict and resolve problems in advance. The data generated is stored in the BIM models, and the FEA results are retrievable at any time for added convenience and to enable speedy alterations.
Challenge 3
The movement of TBM may not adhere to the predefined alignment, so there is an allowable construction tolerance for re-calculation and redesign of tunnel segmental lining.
.
Solution
Tunnel construction involves multiple parallel construction processes, such as transporting and installing tunnel segmental lining, advancement of TBM and installation of support structures.
CATIA was used to create a precise parametric 3D model of the tunnel, which is driven by 3D alignment. With advanced measuring technology, SFEG can measure the actual alignment by TBM and use the measured data to update the 3D digital model. Then the digital model will be used to fabricate tunnel segmental lining, so that SFEG can ensure the fabricated tunnel segmental lining will match the actual tunnels made by TBM. Also, the updated 3D model will be used to guide TBM, adjust its movement and control the overall tolerance from predefined alignment.
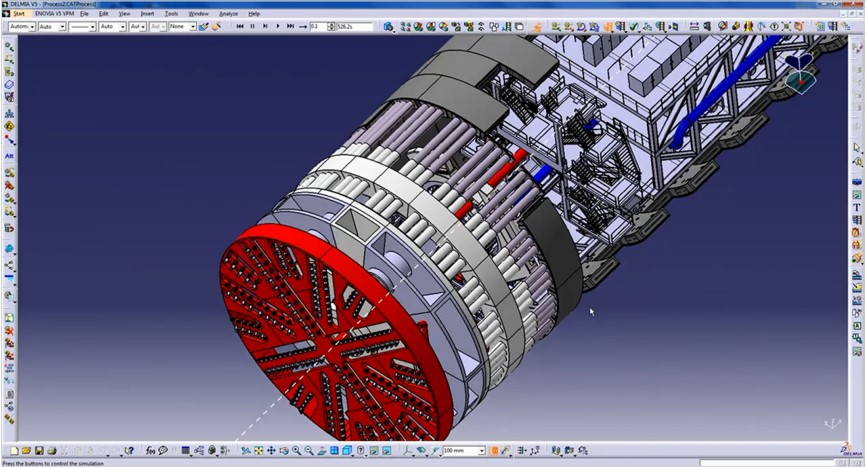
Success factor
SFEG efficiently translated the complex construction data and technical issues of the Zhoujiazhui cross-river tunnel project into intuitive digital references. The early identification of risks has drastically reduced problem areas, improved communication and collaboration among multiple parties, and optimized workflow, so that the project can be delivered on budget and on schedule without compromising quality.
Excerpted from Infrastructure Lifecycle Management Through Virtual Twins, a Dassault Systèmes whitepaper. Download to learn more.
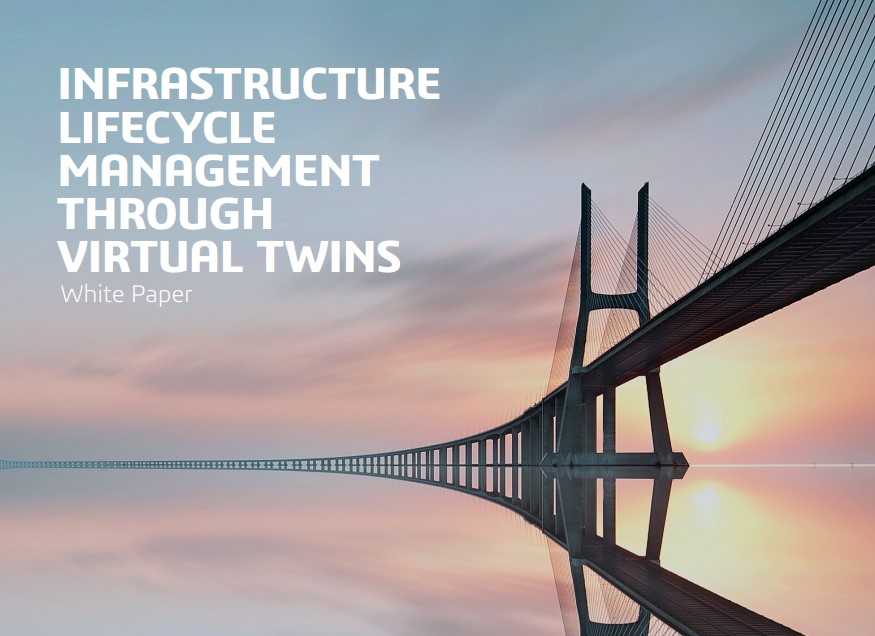
This white paper is presenting industry trends in Construction, Cities & Territories covering infrastructure lifecycle management through virtual twin. Building Information Modelling (BIM) is currently taking over the traditional methods for infrastructure developments, operation and maintenance. Using BIM and virtual twin allow collection, analysis, and aggregation of data and enhances collaboration between different stakeholders, from design to operation and maintenance.
Related links:
Dassault Systèmes Construction, Cities & Territories Industry
Solution
SIMULIA Finite Element Analysis (FEA) enables designers and engineers to create simulations of how the tunnel boring machine (TBM) excavation would impact on real world forces like vibration and fluid flow, and the other physical effects it would have on the surrounding areas. The software separates the geological model into finite elements and uses mathematical analysis to predict the behavior of each element and the overall impact on the surrounding areas.
As construction progresses, the 3D model with construction simulation will enable engineers to predict and resolve problems in advance. The data generated is stored in the BIM models, and the FEA results are retrievable at any time for added convenience and to enable speedy alterations.
Challenge 3
The movement of TBM may not adhere to the predefined alignment, so there is an allowable construction tolerance for re-calculation and redesign of tunnel segmental lining.
.
Solution
Tunnel construction involves multiple parallel construction processes, such as transporting and installing tunnel segmental lining, advancement of TBM and installation of support structures.
CATIA was used to create a precise parametric 3D model of the tunnel, which is driven by 3D alignment. With advanced measuring technology, SFEG can measure the actual alignment by TBM and use the measured data to update the 3D digital model. Then the digital model will be used to fabricate tunnel segmental lining, so that SFEG can ensure the fabricated tunnel segmental lining will match the actual tunnels made by TBM. Also, the updated 3D model will be used to guide TBM, adjust its movement and control the overall tolerance from predefined alignment.
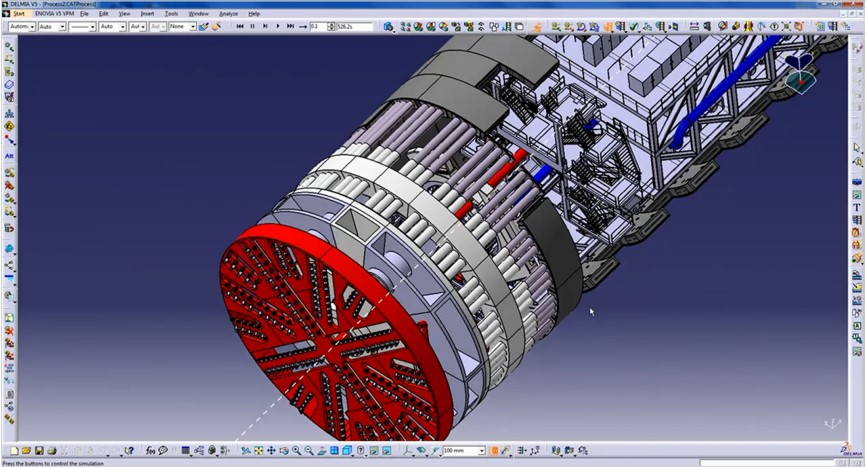
Success factor
SFEG efficiently translated the complex construction data and technical issues of the Zhoujiazhui cross-river tunnel project into intuitive digital references. The early identification of risks has drastically reduced problem areas, improved communication and collaboration among multiple parties, and optimized workflow, so that the project can be delivered on budget and on schedule without compromising quality.
Excerpted from Infrastructure Lifecycle Management Through Virtual Twins, a Dassault Systèmes whitepaper. Download to learn more.
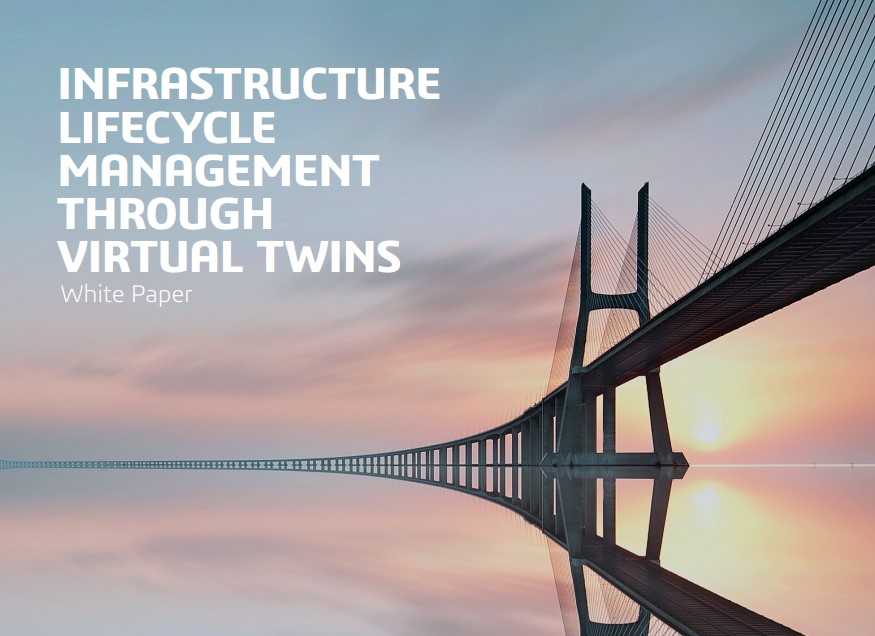
This white paper is presenting industry trends in Construction, Cities & Territories covering infrastructure lifecycle management through virtual twin. Building Information Modelling (BIM) is currently taking over the traditional methods for infrastructure developments, operation and maintenance. Using BIM and virtual twin allow collection, analysis, and aggregation of data and enhances collaboration between different stakeholders, from design to operation and maintenance.
Related links:
Dassault Systèmes Construction, Cities & Territories Industry
Solution
BIM was used to generate visual representations of the project construction process. Dassault Systèmes’ CATIA was used to create a 3D model of the tunnel, and DELMIA was used to simulate in vivid animation how the tunnel would be built. Decision makers were able to instantly understand the entire project, including constructability, resource estimates and the impact of the development on people and the environment. This eliminated the need to hire a design firm to create separate 3D visualization, a traditional route that incurs additional cost. At tender evaluation, scores were split between technical elements and commercial elements. SFEG scored the highest in technical elements and won the bid.
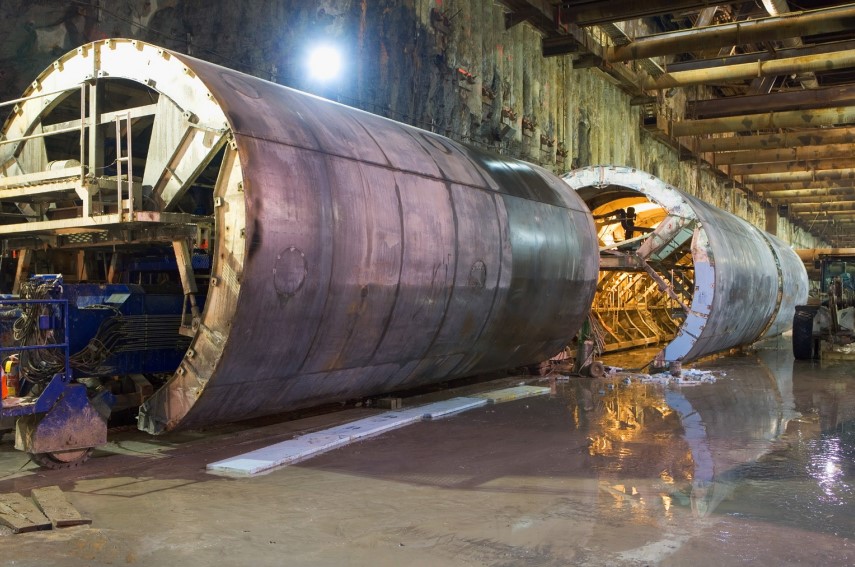
Challenge 2
The tunnel passes through several sensitive areas, such as the Academy Building of Shanghai Polytechnic University, the foundation piles of a pier and a residential area near the construction site.
Solution
SIMULIA Finite Element Analysis (FEA) enables designers and engineers to create simulations of how the tunnel boring machine (TBM) excavation would impact on real world forces like vibration and fluid flow, and the other physical effects it would have on the surrounding areas. The software separates the geological model into finite elements and uses mathematical analysis to predict the behavior of each element and the overall impact on the surrounding areas.
As construction progresses, the 3D model with construction simulation will enable engineers to predict and resolve problems in advance. The data generated is stored in the BIM models, and the FEA results are retrievable at any time for added convenience and to enable speedy alterations.
Challenge 3
The movement of TBM may not adhere to the predefined alignment, so there is an allowable construction tolerance for re-calculation and redesign of tunnel segmental lining.
.
Solution
Tunnel construction involves multiple parallel construction processes, such as transporting and installing tunnel segmental lining, advancement of TBM and installation of support structures.
CATIA was used to create a precise parametric 3D model of the tunnel, which is driven by 3D alignment. With advanced measuring technology, SFEG can measure the actual alignment by TBM and use the measured data to update the 3D digital model. Then the digital model will be used to fabricate tunnel segmental lining, so that SFEG can ensure the fabricated tunnel segmental lining will match the actual tunnels made by TBM. Also, the updated 3D model will be used to guide TBM, adjust its movement and control the overall tolerance from predefined alignment.
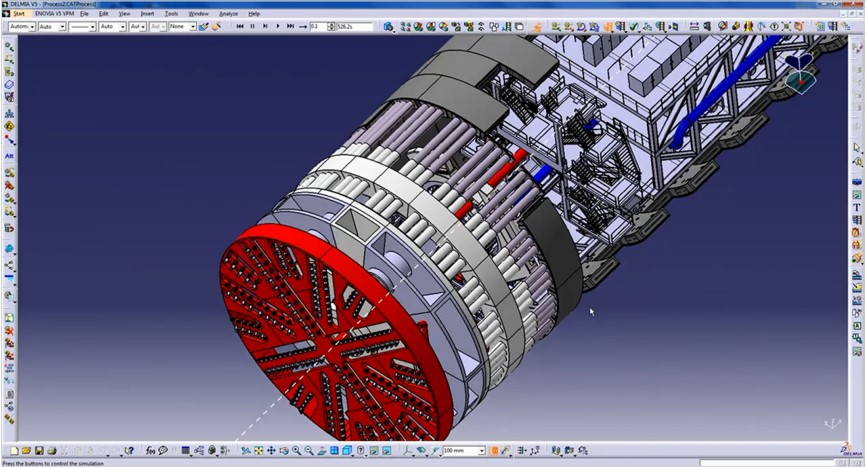
Success factor
SFEG efficiently translated the complex construction data and technical issues of the Zhoujiazhui cross-river tunnel project into intuitive digital references. The early identification of risks has drastically reduced problem areas, improved communication and collaboration among multiple parties, and optimized workflow, so that the project can be delivered on budget and on schedule without compromising quality.
Excerpted from Infrastructure Lifecycle Management Through Virtual Twins, a Dassault Systèmes whitepaper. Download to learn more.
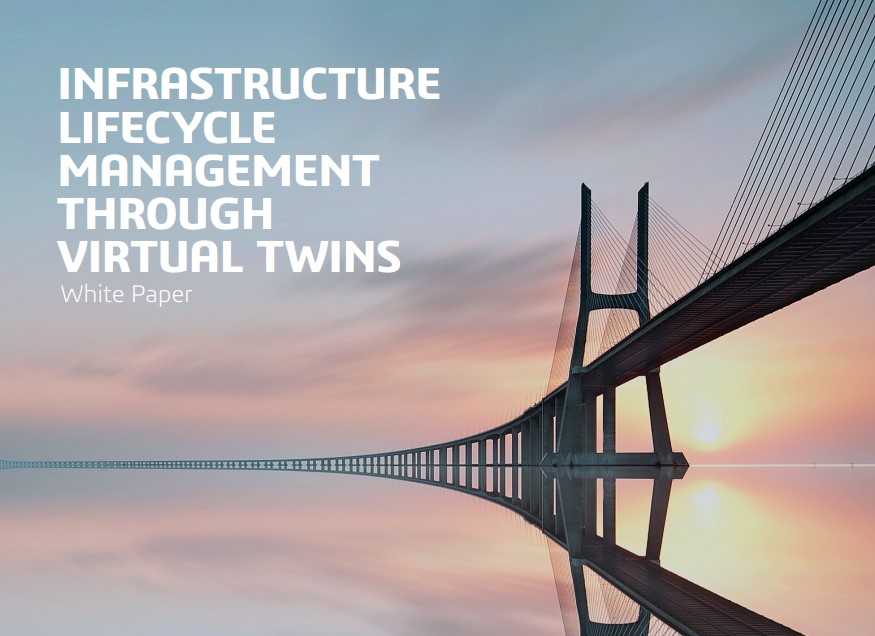
This white paper is presenting industry trends in Construction, Cities & Territories covering infrastructure lifecycle management through virtual twin. Building Information Modelling (BIM) is currently taking over the traditional methods for infrastructure developments, operation and maintenance. Using BIM and virtual twin allow collection, analysis, and aggregation of data and enhances collaboration between different stakeholders, from design to operation and maintenance.
Related links:
Dassault Systèmes Construction, Cities & Territories Industry